-
-
News
News Highlights
- Books
Featured Books
- smt007 Magazine
Latest Issues
Current IssueWhat's Your Sweet Spot?
Are you in a niche that’s growing or shrinking? Is it time to reassess and refocus? We spotlight companies thriving by redefining or reinforcing their niche. What are their insights?
Moving Forward With Confidence
In this issue, we focus on sales and quoting, workforce training, new IPC leadership in the U.S. and Canada, the effects of tariffs, CFX standards, and much more—all designed to provide perspective as you move through the cloud bank of today's shifting economic market.
Intelligent Test and Inspection
Are you ready to explore the cutting-edge advancements shaping the electronics manufacturing industry? The May 2025 issue of SMT007 Magazine is packed with insights, innovations, and expert perspectives that you won’t want to miss.
- Articles
- Columns
- Links
- Media kit
||| MENU - smt007 Magazine
Industry 4.0: Creating a Standard
December 31, 2015 | Barry Matties, I-Connect007Estimated reading time: 18 minutes
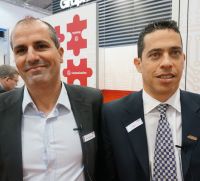
In this interview, I sit down with Mentor Graphics Valor Division's Dan Hoz, general manager, and Ofer Lavi Ben David, product line director, to discuss where Industry 4.0 is taking the industry, and the changes it will bring to both large and small companies, customers, and the supply chain, including how Mentor connects different machines on the shop floor to provide universal Industry 4.0 visibility.
Barry Matties: Please start by telling me about your positions at Mentor Graphics and what you're responsible for.
Ofer Lavi Ben David: I'm responsible for the shop floor products from the Valor division of Mentor Graphics.
Dan Hoz: I'm the general manager of the Valor division.
Matties: Good, so what does that mean? I will start with you Ofer.
Lavi Ben David: I look after everything from product development and marketing activities, to sales and business responsibilities for the products within the division. I work with our sales department, our marketing department, and of course our factory R&D resources.
Hoz: I'm the General Manager of the Valor Division within Mentor Graphics. Mentor Graphics acquired us six years ago. I was the CEO and the President of Valor Computerized systems. It was a listed company. The goal or the strategy for Mentor was to get into an adjacent market and expand their solutions—not just within the design market and the design space, but also into other spaces and markets. They found the design for manufacturing flow to be a very interesting one, and so far it has proven to be a successful one.
That was Valor’s strength. Today, we are still a division within Mentor. I'm responsible for both R&D and marketing. We have a direct sales channel, which is the FPO. We also sell through our World Trade organization, which is the largest sales department within Mentor. We also have customer support and a legal department and all the other things we get from the corporate side.
Matties: From the Valor side, obviously you've been affiliated with Mentor for many years. What sort of changes have you seen recently, from your perspective, and what are the real shifts going on there?
Hoz: One of the most recent changes is Industry 4.0. Its six design principles are perfectly aligned with the way we developed our solutions quite a while ago because of business needs that came from our customers. As such, we are a company that can really deliver solutions for Industry 4.0. I'm not just talking about technical solutions, but also at the business level starting from design all the way down to manufacturing. If it's okay with you, I want to show you and walk you through a short presentation.
We are talking about the design for smart factories of the future, and basically the need or the driver in the market is of course to address increased level of complexity and customization, shorten product lifecycle and increase process globalization. This is about designing in one place and manufacturing in the same place versus designing everywhere and building anywhere. The six principles I mentioned are connectivity, decentralization, human-machine interactions, virtualization, modularity and real-time capability. If we talk about connectivity, this is the ability of all the players to connect via the internet of things—I'm talking about humans, machines and factories. Decentralization is also important.
Matties: That's probably the largest area.
Hoz: You're right. This is the ability of systems to make decisions on their own and this is what we calla “single machine factory”. Now, we look at the solutions to support the needs of the six principles. We start with the NPI—a very early stage in the design flow. Taking the design, going down through the machine programming to understand which machines you want to use. You schedule it and then you start manufacturing it. There's process preparation where you do the machine programming, the documentation, and production portability, which is extremely important for this industry 4.0., which is just about software. Industry 3.0 was about hardware.
Matties: It's about software and data.
Hoz: It's about the data—where you can collect the data and then how you normalize the data, so everyone can speak the same language.
Lavi Ben David: In that aspect, I think we are also in a very good position because over the years we have had machine vendors where everyone comes in with their own proprietary interface. What we were doing on the shop floor was connecting and cooperating with those big providers to connect and communicate with their machines and overcome this challenge of a big environment with many protocols, many languages and different capabilities from the machines that are a separate ecosystem in the factory. We are coming to them with our ability to connect those machines and then provide a single, universal communication protocol for these interfaces. I think although we are not an equipment or hardware provider, with our capabilities to connect to the different machines on the shop floor we are in a position to provide this universal Industry 4.0 visibility.
Matties: It sounds like you're coming in as a package or a total solution, from design to completed product.
Hoz: If you look around through software providers that might have an Industry 4.0 solution, most will only talk to you about the manufacturing, per se. We are taking it a few stages earlier, from design. That's the advantage and this is what we call the left shift concept—every time you can identify something at an earlier stage, it will probably save you 10 times the amount it would cost to repair an error detected at later stage.
Yesterday, there was a very nice NES panel discussion here. There were six people talking from different companies and the last question was, "I work through so many processes and so many machine vendors in so many spaces. Everyone speaks different language. Can we have a standard language for everything like in other spaces, like the semiconductor spaces?" In the past, we used a format called ODB ++. That's a very elegant way of saying 'getting the data'. We came up with that. Now we are going to do the same for manufacturing. It's going to be a standard language for everyone that will enable them to get the data, collect the data, normalize it and share it between the different machines.
Page 1 of 4
Suggested Items
SEL Receives Purdue Senior Design Partner of the Year Award
05/01/2025 | Schweitzer Engineering LaboratoriesSchweitzer Engineering Laboratories (SEL) has been awarded the Senior Design Partner of the Year Award from the Edwardson School of Industrial Engineering at Purdue University.
A Look Into the Future With Futurist Kevin Surace
04/07/2025 | Barry Matties, I-Connect007In this interview after his keynote address at IPC APEX EXPO 2025, futurist Kevin Surace reflects on important lessons learned and how they shaped his own future. He also makes some bold predictions for the use of AI in PCB board design, fabrication, and assembly—and what the common household will look like in 10 years. It’s an exciting and adventurous step into a future where humans work alongside robots, all for the betterment of everyone.
Networking and Growth: Highlights from the IPC Emerging Engineer Reception
03/19/2025 | Marcy LaRont, I-Connect007It was my first day in Anaheim for IPC APEX EXPO, and I arrived at John Wayne airport on Saturday to cool and sunny weather, which, coming from Arizona, is my favorite. The show starts with technical and standards work over the weekend as we prep for the show floor opening in the days to come. Exhibitors and union workers get busy building the impressive booths that make up the exhibition, which started on Tuesday and saw a steady flow of attendees all day long.
Mind Meld: Brian Chislea and AJ Arriaga Share Their Fascinating Experience in IPC's Mentorship Program
01/28/2025 | Michelle Te, IPC CommunityIPC’s Emerging Engineer program provides professionals an opportunity early in their careers to learn from dedicated industry volunteers participating in standards development. Two participants in the program—Brian Chislea, Dow Chemical, mentor to AJ Arriaga, Summit Interconnect—share their experiences in the program in a series of articles. We will follow them through their three years in the mentorship. This is the first in the series.
'Qualcomm AI Program for Innovators' Launched to Foster On-Device AI Innovation in the Asia-Pacific Region
12/27/2024 | Qualcomm Technologies, Inc.Qualcomm Technologies, Inc. announced the launch of the Qualcomm AI Program for Innovators (QAIPI) 2025 - APAC, a new initiative aimed at supporting professional developers and startups from Japan, Singapore, and South Korea to create cutting-edge on-device AI solutions across diverse sectors.