Rex Rozario, Part 3: The Future Beckons
March 16, 2016 | Barry Matties, I-Connect007Estimated reading time: 14 minutes
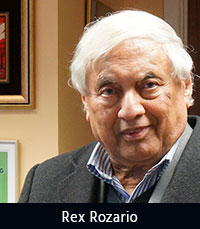
In Part 3 of our multi-part interview with industry veteran Rex Rozario, we begin with the future. Having achieved success in China, could Rex and the Graphic team have their sights trained on the U.S.? Also in this installment, Rex weighs in on China’s future, and we discuss the value of automation. Is it for everyone?
Click here for Part 1 and Part 2.
Barry: Rex, what can you tell me about what’s on the horizon for Graphic?
Rozario: We have a lot of possible plans in mind of where to go, so we are still looking around. We feel our next journey is to the U.S., because it's a huge marketplace. With our expertise and once they get to know what we do, we’ll be successful and it will open doors for us. I think the proof will be in the pudding once they try out our services. Also, we're the first company in the UK to offer application engineering as a free service. If somebody is designing something, we will go in there, provided we get the prototypes and the order to follow up on. And that gives them confidence. We can technically design it to manufacture and we can manufacture it much faster, more economically and at a cost saving. Now if someone is designing something really special, very high tech, we would send their favorite engineers and they could be there for two weeks with them to discuss it.
Matties: That was a big advantage in the early days for you.
Rozario: It certainly was.
Matties: Now other companies have followed suit.
Rozario: Anything you start, everybody will follow. It goes without saying that everybody claims all sorts of things and people only find out that it's not true when someone asks a question. But like I mentioned before, we have always worked on approvals. If there is one available we have to get it. Then they follow up like the managing director of BAE did in 1994, when he said our product had the best performance and all of his sites are open for our product and so forth. That's only one supplier. There are so many others at that level who are talking to us.
The only challenge is if for some reason they feel they want to split the order for security reasons, then somebody else gets it. Now we have so much choice here [UK], we can spread it out between UK, China, Italy and the U.S. It’s a safety net; if a factory burns down it doesn't make any difference to the customer.
We’re not putting all the eggs in one basket. That was a fear that most people had in the past, but they can come to us now for a one-off for any quantity they want. Obviously, we are competitive, otherwise customers wouldn't stay with us.
Matties: When you talk about the future and your strategies and looking to America, what is left to do there? In terms of strategy, what do you see?
Rozario: We start with the marketplace. We know rigid-flex could take off there. At Graphics USA, we would obviously think about putting a real facility in there at Santa Fe Springs, or we could look at combining it with someone else, like we do in China, at the DSG facility. We have the room there to expand.
Matties: Are you looking to do volume production in the U.S.? With automation it seems like volume production can be done anywhere in the world these days considering your expertise with automation.
Rozario: When you talk about automation, the volume is unlimited. In China, if you want half a dozen boards, it's not good to do it here in the UK and ship it over there. They can do it. China is geared up for large, consistent volume, so that's available, whereas other companies in the UK, and Italy, are medium-sized. We're talking about thousands, but not the full run of tens of thousands boards. Fortunately, I think when global customers realize that there is a company that with one phone call, text, or e-mail can look after all their needs of any type of board they would want, it’s hard to turn down.
Some people specialize in flex, rigid-flex or PTH and so forth. Not many people have the experience to do everything. We have worked on carbon fibre and have lots of experience with it because we feel it’s the material of the future. People will be looking for tougher materials in heating systems and so forth. It's a bit expensive for people to actually change over from epoxy glass now. At some stage there could be requisites that people would need. All the body work for planes is now done with carbon fibre, and some of the top cars. That's something on which we are in close liaison with Exeter University. We're constantly developing and experimenting and looking at what else is there, so that we can offer it to the customer, hopefully better than anybody else
Matties: What I hear you saying is, wherever you're at, it's never good enough, because the future is constantly changing.
Rozario: It's changing overnight, really. Whatever you have today is different on the following day.
Matties: You could easily sit back as a company and just enjoy the success that you've already achieved and ride off into the sunset so to speak.
Rozario: Easily, for myself personally, but for the company itself you have to compare us to the large companies who were competing with us when we first started—BAE, Marconi, IBM, Motorola—all these companies had their own PCB manufacturing. There came a time when they had to decide to just stay put or keep developing, and they decided, “Why should we spend money on R&D? Let those guys do it. Let's go to someone who has the facility and the experience. It’s cheaper than employing people and buying the raw material up front and all that hassle.”
Matties: Then the environmental impact came along, too.
Rozario: Yeah, I remember so many board shops being closed in the early days. I also remember people moving from one state to another to save cash, because the laws were different in the other state.
Fortunately, like most of the guys who started together back then, there are names that we still relate to, although they might not have been PCBs. Those were the pioneer days. You had to go looking for things and make things happen. It's a bit easier now, because you can go and buy a machine that will do the job. With the availability of all the facilities for manufacture now, you don’t have to reinvent the wheel. When somebody realized they wanted a double-sided board connected, nobody thought about through-hole plating. You just put an eyelet in there and that did the job. Someone said, "Gosh you have to put it in a mechanical device, why couldn't we do it in the plating?" Those things have all been done, but there are areas like buried capacitance where we are still doing that now. There will come a time for the future materials, like graphene. I think that's the way things will go, but hopefully we will be there and constantly be aware that these things are happening.
Again, fortunately with my connections to all the federations like IPC, I’ve been very much involved. We are fully aware of what's going on and also are constantly talking to suppliers and so forth. As long as that continues, I think we should be okay. We're always aware that there comes a saturation point, and then how do you carry on? The only way is technology. I feel the only way we can survive and make a profit is by constantly developing new technology, because customers will always pay for something that's going to save them cash, and probably pay a little bit more. We did a conference with IPC many years ago and called it “Circuits on the Cheap.” The hall was packed because people came in there looking for a cheap solution.
We were saying that what we manufactured 25 years ago, the same thing can be had cheaper than before. That was the idea, but they got the wrong impression with Circuits on the Cheap. Things are getting cheaper and cheaper due to the competition and if there's a recession, people are just cutting prices. Even now, to my knowledge, several small companies are struggling and some of them sadly might disappear.
Matties: There's no doubt some are going to disappear.
Rozario: Also, the new trend is amalgamation, and obviously if you look at the large companies like TTM, Viasystems and DDi, they are one company now, because that's another way of sustaining and keeping the levels going and keeping the marketplace. Obviously, the bigger you are, the more service you have. You don't want to stay where you are. You must look at the next stage. That's another thing that one can look at, and we've got a very good partner we are working with now. Those are other areas we might look at very closely as we develop.
Page 1 of 2
Suggested Items
Hunting for Clues: Feng Xue Solving Circuit Board 'Crimes' With AOI Standard
05/08/2025 | Linda Stepanich, IPCWhen residents in sleepy English villages needed a top-tier detective to solve a murder, they called on Belgian super-sleuth Hercule Poirot, author Agatha Christie’s fictional detective famous for using his “little grey cells” to solve crimes. In the same way, IPC standards development committees, when creating a standard to detect defects in circuit boards using Automated Optical Inspection (AOI), call on IPC A-Team, Hercule.
IPC Strengthens Global Focus with Promotion of Sanjay Huprikar to Chief Global Officer
05/08/2025 | IPCIPC, the global electronics association, announces the promotion of Sanjay Huprikar to chief global officer. This newly created position reflects the association’s forward-looking strategy and industry needs to strengthen the electronics supply chain.
Navigating Global Manufacturing in an Era of Uncertainty
05/07/2025 | Philip Stoten, ScoopThe EMS industry faces unprecedented challenges as global trade tensions rise and tariff announcements create market uncertainty. In an overview of IPC Europe’s podcast, MADE IN EUROPE, industry experts from GPV and Zollner examine how these developments impact our businesses and customers, and what strategies will prevail in this new landscape.
Nick Koop Launches IPC Flex Design Class
05/06/2025 | Andy Shaughnessy, Design007 MagazineNick Koop is director of flex technology for TTM Technologies, and he’s been a staple of IPC’s flex committees for decades. He’s also a longtime flex design instructor, and he’s about to debut a new IPC class, Flex and Rigid-Flex Design for Manufacturability, which will run May 12–21. In this interview, Nick tells us about this new class and what attendees can expect to learn.
The Government Circuit: Trump’s Trade War Disrupts the Electronics Ecosystem
05/06/2025 | Chris Mitchell -- Column: The Government CircuitThere is certainly no shortage of work to be done in the IPC Government Relations department, as the U.S. waged a tariff campaign on practically every industrial country in the world and several countries embarked on high-tech initiatives with a mix of approaches to the crucial foundations of electronics manufacturing. Indeed, the breadth and speed of U.S. President Donald Trump’s tariff campaign continues to be a serious challenge for our industry.