-
-
News
News Highlights
- Books
Featured Books
- pcb007 Magazine
Latest Issues
Current IssueThe Hole Truth: Via Integrity in an HDI World
From the drilled hole to registration across multiple sequential lamination cycles, to the quality of your copper plating, via reliability in an HDI world is becoming an ever-greater challenge. This month we look at “The Hole Truth,” from creating the “perfect” via to how you can assure via quality and reliability, the first time, every time.
In Pursuit of Perfection: Defect Reduction
For bare PCB board fabrication, defect reduction is a critical aspect of a company's bottom line profitability. In this issue, we examine how imaging, etching, and plating processes can provide information and insight into reducing defects and increasing yields.
Voices of the Industry
We take the pulse of the PCB industry by sharing insights from leading fabricators and suppliers in this month's issue. We've gathered their thoughts on the new U.S. administration, spending, the war in Ukraine, and their most pressing needs. It’s an eye-opening and enlightening look behind the curtain.
- Articles
- Columns
- Links
- Media kit
||| MENU - pcb007 Magazine
The Sum of All Parts: The Fabricator-Assembler Connection
June 20, 2016 | Sam Sangani, PNC Inc.Estimated reading time: 3 minutes
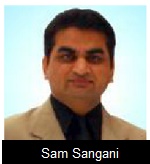
After discussing the relationship between PCB fabricators and those who design the boards (see my previous column ), it is imperative to do the same for the relationship between assemblers and fabricators. This brings about a whole new set of potential complications.
For example, a board manufacturer may not fully understand the scope of panel size limitations for the SMT line in question or if rails are needed on individual pieces/panels so that the pick & place machine has sufficient room to place the components that are close to the board’s edge. You may also have a situation where a component overhangs off the edge of a board. To be sure in can be placed, if in panel form, then the panel array will need additional space between boards so there is no interference of the part to the next board in the array.
Logistical Challenges
The supply of parts is a very crucial element of this relationship. Most assembly houses do not stock an inventory of components for the simple fact that it does not make business sense; every customer will require different parts from job to job and revision to revision. For the assembler to purchase and sit on various parts they think their customers might need is essentially just an increase in toxic, unusable assets that hurt the bottom line. You might have capacitors, resistors etc., with the exact value your customers need, but if it is not made by the manufacturer they desire or supplied by their preferred vendor, the assembler is left with an unusable part.
However, if a board house also has the ability to assemble, it lends to a number of advantages. First and foremost, the customer is able to rely on an accurate and unchanging quote from their manufacturer/assembler. Furthermore, when the customer is given a date on which their job will be completed, their job is actually completed on that date. They are not waiting to receive the bare board from one place and then send it out to another place to be populated—at which time the wait begins all over again. The speed of this process—end to end—is also accelerated significantly.
Packaging and Cleanliness
This in crucial in today’s market when customers expect their boards to be pristine and understandably so. The packaging and shipping processes can cause unnecessary cosmetic and damage to the board. The boards should be vacuum sealed with desiccant. Desiccant is vital to eliminate any moisture that can potentially absorb into the board in transit as well as sitting on the assembler’s shelf until they are assembled. In the case of immersion silver final finish, silver saver paper needs to be inserted between each board to keep the silver from oxidizing. ESD handling can also be a potential issue. When the board is manufactured and populated at the same location, however, you minimize the possibility of these and related errors occurring.
Uniformity of Process
Quality control can be greatly affected when separate entities are handling the manufacturing and assembly processes. Also, there is a great disconnect in the communication between the manufacturer and assembler. Some customers choose to be the ones to relay information between the two parties whereas others may simply choose to hand the ball off to the people working for them. The ideal scenario in this situation is a balance between those two scenarios where the input of the customer, manufacturer and assembler is taken into account and valued equally.
Similar to the designer-manufacturer relationship, the most comprehensive solution to this problem is the Total Concept. If manufacturing and assembling are done under the same roof, the space in which errors can occur is marginalized exponentially.
Although it seems like conventional wisdom, it is not always so. Simply put, the less distance there is between two processes, the less room for error.
Sam Sangani is president and CEO of PNC Inc.
Suggested Items
TT Electronics Achieves ISO 13485 Medical Certification at Mexicali EMS Facility
06/27/2025 | TT ElectronicsThis milestone underscores TT Electronics’ commitment to delivering high-quality, compliant, and reliable manufacturing solutions to its global customers in healthcare and life sciences.
CEE PCB Appoints KT Technical Solutions as North American Sales Representative
06/23/2025 | CEE PCBStrategic Partnership Expands CEE PCB’s Reach into the North American Market with a Focus on Customer-Centric Service and High-Quality Manufacturing
Benchmark Strengthens Presence in Jalisco with Grand Opening of Advanced Manufacturing Facility in Guadalajara
06/21/2025 | BUSINESS WIREBenchmark Electronics, Inc., a global provider of engineering, design, and manufacturing services, celebrated the grand opening of its brand-new manufacturing facility in Guadalajara, Mexico.
PMGC Holdings Signs Letter of Intent to Acquire Profitable U.S.-Based Electronics Manufacturing Company
06/10/2025 | Globe NewswirePMGC Holdings Inc., a diversified public holding company, is pleased to announce the signing of a non-binding Letter of Intent (LOI) to acquire a U.S.-based, cash-flow positive electronics contract manufacturing company with over 40 years of operational history.
VeriSilicon’s AI-ISP Custom Chip Solution Enables Mass Production of Customer’s Smartphones
06/09/2025 | BUSINESS WIREVeriSilicon recently announced that its AI-ISP custom chip solution has been successfully adopted in a customer’s mass-produced smartphones, reaffirming the company’s comprehensive one-stop custom silicon service capabilities in AI vision processing.