-
- News
- Books
Featured Books
- smt007 Magazine
Latest Issues
Current IssueWhat's Your Sweet Spot?
Are you in a niche that’s growing or shrinking? Is it time to reassess and refocus? We spotlight companies thriving by redefining or reinforcing their niche. What are their insights?
Moving Forward With Confidence
In this issue, we focus on sales and quoting, workforce training, new IPC leadership in the U.S. and Canada, the effects of tariffs, CFX standards, and much more—all designed to provide perspective as you move through the cloud bank of today's shifting economic market.
Intelligent Test and Inspection
Are you ready to explore the cutting-edge advancements shaping the electronics manufacturing industry? The May 2025 issue of SMT007 Magazine is packed with insights, innovations, and expert perspectives that you won’t want to miss.
- Articles
- Columns
- Links
- Media kit
||| MENU - smt007 Magazine
Bumping of QFNs/LGAs and Other Leadless Devices for More Consistent Rework
August 9, 2016 | Bob Wettermann, BEST Inc.Estimated reading time: 2 minutes
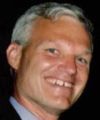
The Challenge
Leadless devices are now the greatest package style by volume (Yole Development Market Survey) being placed by electronics assemblers worldwide. These packages, due to a variety of factors, are challenging to rework. Among the greatest challenges this package presents are the solder voiding primarily on the ground plane, the inability to clean underneath the devices post rework, and the difficulty in getting similar standoff heights on both the IO and center ground. These challenges along with their increasing complexity and ever smaller package sizes challenge even the most skilled rework technicians.
In addition to the above rework challenges, the package style itself remains very difficult to inspect post reflow for a variety of reasons. As there are rarely any visible solder joints due to in most instances a lack of a solderable sidewall on the IO pads of the device, as well as the very low standoff distances between the bottom of the device and the PCB, there is very little visual inspection which can occur. This means that the reliance on a skilled x-ray technician as well as a capable x-ray system is in order.
Types of Rework Methods Available
Of the various methods for reworking leadless devices, the bumping method (Figure 1), when appropriate for the board and part at hand, is the process with the greatest first pass yield, the one with the greatest standoff distance for cleaning flux residue from underneath the device and the one with the greatest assurance of minimizing voiding.
Figure 1: Bumped leadless device prior to placement.
"Bumped" 2 x 2mm QFN Package, 0.5mm pitch, 0.2mm Wide Pads
There are numerous methods being used to rework leadless devices; either guided by the older IPC 7711 5.4.1 process guidelines or by the newest stenciling techniques. The older of these methods includes solder paste printing on the site location of the PCB followed by the placement and reflow of the device. The newer methods including IPC 7711 procedures 5.8.1.1 and 5.8.1.2 includes the device pads being “bumped” followed by their placement. The device, post “bumping”, can be placed using a rework system using paste flux or with a properly-designed “capture” stencil which has apertures that can locate and capture the “bumps” on the PCB.
Both of these latter methods for reworking leadless devices were popularized using polyimide stencils. In these methods, a polyimide stencil is placed over the land patterns on the bottom of the device. Solder paste is then squeegeed in to the apertures. The device is then reflowed. Post reflow, the stencil is peeled off leaving “bumps” on the bottom of the device (mini metal stencils can also be used when appropriate). Because the reflow is done in air, the flux volatiles can escape, thereby having the “bumped” part nearly free of voids. In addition, these stencils are thicker than the initial manufacturing stencils meaning that the final standoff height is greater when compared to traditional printing and placement. This bumping technique also greatly simplifies placement of the leadless device as a lower-skilled technician or even first-timer, when following the instructions properly, can produce the “bumps” for placement.
To read this entire article, which appeared in the August 2016 issue of SMT Magazine, click here.
Suggested Items
SHENMAO Strengthens Semiconductor Capabilities with Acquisition of PMTC
07/10/2025 | SHENMAOSHENMAO America, Inc. has announced the acquisition of Profound Material Technology Co., Ltd. (PMTC), a premier Taiwan-based manufacturer of high-performance solder balls for semiconductor packaging.
KYZEN to Highlight Understencil and PCB Cleaners at SMTA Querétaro Expo and Tech Forum
07/09/2025 | KYZEN'KYZEN, the global leader in innovative environmentally responsible cleaning chemistries, will exhibit at the SMTA Querétaro Expo & Tech Forum, scheduled to take place Thursday, July 24, at Centro de Congresos y Teatro Metropolitano de Querétaro.
Driving Innovation: Direct Imaging vs. Conventional Exposure
07/01/2025 | Simon Khesin -- Column: Driving InnovationMy first camera used Kodak film. I even experimented with developing photos in the bathroom, though I usually dropped the film off at a Kodak center and received the prints two weeks later, only to discover that some images were out of focus or poorly framed. Today, every smartphone contains a high-quality camera capable of producing stunning images instantly.
Hands-On Demos Now Available for Apollo Seiko’s EF and AF Selective Soldering Lines
06/30/2025 | Apollo SeikoApollo Seiko, a leading innovator in soldering technology, is excited to spotlight its expanded lineup of EF and AF Series Selective Soldering Systems, now available for live demonstrations in its newly dedicated demo room.
Indium Corporation Expert to Present on Automotive and Industrial Solder Bonding Solutions at Global Electronics Association Workshop
06/26/2025 | IndiumIndium Corporation Principal Engineer, Advanced Materials, Andy Mackie, Ph.D., MSc, will deliver a technical presentation on innovative solder bonding solutions for automotive and industrial applications at the Global Electronics A