-
- News
- Books
Featured Books
- pcb007 Magazine
Latest Issues
Current IssueSales: From Pitch to PO
From the first cold call to finally receiving that first purchase order, the July PCB007 Magazine breaks down some critical parts of the sales stack. To up your sales game, read on!
The Hole Truth: Via Integrity in an HDI World
From the drilled hole to registration across multiple sequential lamination cycles, to the quality of your copper plating, via reliability in an HDI world is becoming an ever-greater challenge. This month we look at “The Hole Truth,” from creating the “perfect” via to how you can assure via quality and reliability, the first time, every time.
In Pursuit of Perfection: Defect Reduction
For bare PCB board fabrication, defect reduction is a critical aspect of a company's bottom line profitability. In this issue, we examine how imaging, etching, and plating processes can provide information and insight into reducing defects and increasing yields.
- Articles
- Columns
- Links
- Media kit
||| MENU - pcb007 Magazine
Laser Pointers: Laser Processing and Telecentricity
September 8, 2016 | Mike Jennings and Patrick Riechel, ESIEstimated reading time: 5 minutes
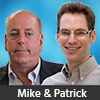
Since Mike and I often receive questions on topics that are relevant to a broader audience, we’ve decided to start using this column to share those questions and answers with our readers. We’ll periodically devote the space in this column to address questions that we receive that are especially timely or topical, or address a topic that affects a wider range of readers.
This month’s question:
“How does your laser drilling tool ensure that the hole in the panel is perpendicular to the work surface when the galvanometer is moving the beam at an angle to the work surface?”
The short answer:
For applications such as via drilling, where vertical laser incidence angle is especially important (who wants to try to plate a panel with blind vias drilled at varying angles?) and where laser scanning technologies such as galvanometers are used, the incorporation of telecentric lenses is the most effective way to ensure beam perpendicularity.
The Basics
First let’s dive into the basics and explain galvanometer scanning and its role in laser via processing, along with a brief overview of the technology that drives scan lens accuracy. For a more detailed overview of the considerations that go into designing the laser and optics subsystems of a laser processing system, watch the ESI “Chalk Talk” titled Optimize Production with Optical Design Considerations, presented by ESI’s Laser and Optics Engineering Manager Helen Li. It can be found in the Resources section of esi.com.
What is scanning with galvanometers and when are they used?
In laser processing systems, mirror galvanometers—commonly known as “galvos”—are mechanisms consisting of mirrors attached to rotary motors to allow for a rapid laser scanning motion. They are one of several options for moving the laser with respect to the work piece (beam positioning), along with linear and rotational stages, fast steering piezo-electric mirrors, electro-optic deflectors, MEMS mirrors, and even solid-state technology such as that used in ESI’s patented Third Dynamics™ beam positioning system. Laser systems designers consider tradeoffs in speed, acceleration, accuracy and range of motion when choosing beam positioning components. Galvos excel in delivering greater levels of accuracy whenever high-velocity feature processing is desired, especially when it involves the processing of curved features, such as those in via drilling and small circuit routing applications.
Effective Use of Scan Lenses
Scan lenses are optical assemblies used to focus a collimated laser beam on a small, tightly-focused spot on the work surface when using scanning components like galvos. Unlike simpler objective lenses, which require that the laser beam stays stationary in the central lens axis in order to focus the beam, scan lenses are designed to accommodate for beam motion across the entire scan lens surface (See Figure 1).
Two types of scan lenses are most commonly used in laser processing: non-telecentric f-theta lenses and telecentric f-theta lenses (see Figure 2). The “f-theta” here refers to the method used to calculate where the beam will strike the work surface when the input beam deflected at angle “theta” strikes the scan lens with focal length property “f”.
The use of telecentric f-theta lenses is the secret to creating holes perpendicular to the work surface when the galvanometer is moving the beam at an angle to the panel surface. Telecentric scan lenses use a complex set of optical components to ensure that, regardless of the angle at which the galvo beam enters the scan lens, the output beam will exit the scan lens parallel to the central lens axis and, therefore perpendicular to the panel surface.
As with many things, there is a set of tradeoffs associated with the choice to employ either telecentric or non-telecentric scan lenses. Telecentric scan lenses are more complex and can be costlier. Also, telecentric scan lenses are typically larger than non-telecentric lenses. However, when beam perpendicularity is important to the specific application, such as via drilling, the quality and yield benefits far outweigh the added cost.
The use of high-quality scan lenses is instrumental in ensuring high quality beam delivery at the panel surface. Some scan lenses are designed with large scan areas, but are manufactured with more narrow areas in which high optical quality and minimal spot distortion are guaranteed. Other scan lenses are guaranteed to deliver high beam quality across the entire scan area.
Price-Performance Tradeoffs
Regardless of the scan lens choice your laser system supplier has made, you, as the system user are still responsible for delivering high process quality and maximized yield at a low cost-of-ownership. The scan lens will typically be the most expensive optical component in your laser system and needs your attention, especially since it is relatively close to the dirty, debris-generating work of removing material. It’s the first place you should check and clean, especially if you find that you have missing or incompletely drilled vias. Since many laser systems include debris removal and optics purging systems that rely on factory vacuum and compressed air supply to operate, it is critical to ensure that the supplied vacuum and compressed air meet manufacturer pressure and flow requirements and that the compressed air is clean. If you have harmful particles in your compressed air, those same particles can settle on your scan lens via the debris assist air feed, resulting in yield loss and possibly a costly scan lens replacement.
Key Takeaways
In most laser micromachining applications, especially via drilling, beam perpendicularity is critically important. If the beam is not perpendicular to the work surface, the laser spot will strike the material with an elliptical—not circular—shape, resulting in inconsistent material removal and non-vertical holes. If this factors into your process yield, do your research and choose a supplier that incorporates high-quality telecentric lenses to ensure that your yield costs stay low. Similarly, place a high priority on the ongoing maintenance of your optics by strictly adhering to the laser system manufacturer’s recommended preventive maintenance schedule, paying attention to the vacuum and compressed air availability at your site. By following these simple guidelines, you can ensure that you keep your costs low and your process yields high. Happy processing!
Patrick Riechel is product manager for ESI’s flexible circuit micromachining tools. To read past columns or to contact him, click here.
Testimonial
"The I-Connect007 team is outstanding—kind, responsive, and a true marketing partner. Their design team created fresh, eye-catching ads, and their editorial support polished our content to let our brand shine. Thank you all! "
Sweeney Ng - CEE PCBSuggested Items
ASC Sunstone Circuits Appoints Ron Morelli as Senior Production Manager
07/21/2025 | ASC SunstoneASC Sunstone Circuits is proud to announce the appointment of Ron Morelli as Production Manager. With over 30 years of experience in production management and planning, Ron brings a wealth of operational expertise and team leadership to ASC Sunstone’s manufacturing operations.
NEOTech’s Agave 1 Facility Earns AS9100 Certification for Commercial Aerospace Manufacturing Excellence
07/17/2025 | NEOTechNEOTech, a premier provider of electronic manufacturing services (EMS), integrated design engineering, and advanced supply chain solutions for the aerospace and defense, medical device, and high-tech industrial markets, proudly announces that its Agave 1 manufacturing facility in Juarez, Mexico has officially received AS9100 certification.
Inside Aimtron’s Cross-border EMS Strategy
07/08/2025 | Nolan Johnson, SMT007 MagazineMukesh Vasani immigrated from a very small farming village in India to the U.S. in 1995 as a civil engineer. After shifting into electronics, Mukesh built his Chicago-based company, Aimtron, into a successful enterprise by combining quality with competitive pricing. He leveraged his roots in India to expand manufacturing without compromising on quality.
Trouble in Your Tank: Can You Drill the Perfect Hole?
07/07/2025 | Michael Carano -- Column: Trouble in Your TankIn the movie “Friday Night Lights,” the head football coach (played by Billy Bob Thornton) addresses his high school football team on a hot day in August in West Texas. He asks his players one question: “Can you be perfect?” That is an interesting question, in football and the printed circuit board fabrication world, where being perfect is somewhat elusive. When it comes to mechanical drilling and via formation, can you drill the perfect hole time after time?
Driving Innovation: Direct Imaging vs. Conventional Exposure
07/01/2025 | Simon Khesin -- Column: Driving InnovationMy first camera used Kodak film. I even experimented with developing photos in the bathroom, though I usually dropped the film off at a Kodak center and received the prints two weeks later, only to discover that some images were out of focus or poorly framed. Today, every smartphone contains a high-quality camera capable of producing stunning images instantly.