-
- News
- Books
Featured Books
- pcb007 Magazine
Latest Issues
Current IssueThe Hole Truth: Via Integrity in an HDI World
From the drilled hole to registration across multiple sequential lamination cycles, to the quality of your copper plating, via reliability in an HDI world is becoming an ever-greater challenge. This month we look at “The Hole Truth,” from creating the “perfect” via to how you can assure via quality and reliability, the first time, every time.
In Pursuit of Perfection: Defect Reduction
For bare PCB board fabrication, defect reduction is a critical aspect of a company's bottom line profitability. In this issue, we examine how imaging, etching, and plating processes can provide information and insight into reducing defects and increasing yields.
Voices of the Industry
We take the pulse of the PCB industry by sharing insights from leading fabricators and suppliers in this month's issue. We've gathered their thoughts on the new U.S. administration, spending, the war in Ukraine, and their most pressing needs. It’s an eye-opening and enlightening look behind the curtain.
- Articles
- Columns
- Links
- Media kit
||| MENU - pcb007 Magazine
Ventec Europe Celebrates 10 Years as 'Not Just Another Laminate Merchant'
October 26, 2016 | Pete Starkey, I-Connect007Estimated reading time: 4 minutes
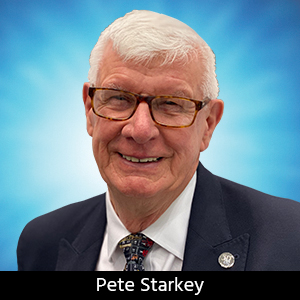
Incorporated in November 2006 as a joint venture known as Global Ventec Laminates, Ventec Europe imported its first container-full of material in May 2007. Later that year, Ventec began cutting, packaging and shipping material from its original location in Leamington Spa, in the midlands of England.
Having known and worked with Managing Director Mark Goodwin in a previous generation of the PCB laminate trade, I was keen to understand his logic and motivation in setting up a laminate distribution business in the UK, which had seen a dramatic decline in its PCB industry.
“Is there a market left to service?” I asked.
He answered, “There most certainly is! There's no argument that the high-volume commercial stuff is long-gone from the UK and Europe, and domestic laminate manufacture has largely gone with it. But there's still a remarkably solid PCB manufacturing industry, albeit very demanding in terms of service, technology and product quality.”
My next question was, “Don't the European and American laminators recognize the potential of this marketplace? And can they not rely upon the loyalty of their traditional customers?”
Goodwin answered, “Mergers and acquisitions among Western World laminators have left the industry with fewer choices, and those laminators have tended to focus their energies developing their Far Eastern markets, leaving themselves short of resources to service their traditional home market. If anything, we're coming in the opposite direction- they've opened the door for an entrepreneurial Taiwanese laminator to develop a world presence.”
Now, here we are 10 years on, a bit older and not a lot wiser, reflecting upon those words as we stand in Ventec Europe’s immaculate headquarters facility, still in Leamington Spa, but in smart new premises.
Starkey: Mark, do you remember that “Not just another laminate merchant” article I wrote after my first visit? You weren’t far out in your vision of the future!
Goodwin: I certainly do, and I think your report was a fair assessment of where we were at that time and what our aims were for the future. As we approach our tenth anniversary, let’s do a few “then and now” comparisons.
We started with a 1985-vintage Schmid saw with an improvised extraction system. We are now operating in the UK with two state-of-the-art Yow Shi diamond-blade saws with full extraction, and we have a large-format Holzma panel saw in Germany for volume production.
Back then we started with a well-used Rosenthal slitter that Jack Pattie had acquired in the Chicago area. A local company refurbished it for us, and we began cutting prepreg on it, initially with no extraction. Now we have three state-of-the-art Pasquato slitters in the UK, one dedicated to polyimide, and a similar Pasquato machine in our German facility. In the UK, all the machines are equipped with certified Class 1000 laminar flow canopies, and we maintain a strict clean-room cutting environment.
Our strength has always been that we have had good people right from the start and, even though some of our original equipment might have been a bit dated, our people were capable of using it to do a first-class job. The inverse is not true—even with the best of equipment! Within our team we have a great depth of industry experience and understanding, and we maintain high standards of training. We do a good job. Not to say things can’t be improved; we’re improving all the time. Look what we’ve achieved over the last 10 years: Who would have foreseen the lab capability we’ve got in Europe. Who would have foreseen the efficiency of fabrication and distribution and the standards of cleanliness that we have established in our warehouses in Leamington Spa and Kirchheimbolanden near Frankfurt? Who would have thought we would have had a global OEM team driven off the back of our overseas business units?
We started in the UK, rolled out to Germany, incorporated the East and West Coast and Midwest in America, and we now have an overseas business approaching $50 million. So I think the scepticism with which some of our competitors viewed our venture into Europe was a little misplaced! Our European base has been a springboard to get ourselves well-established in other high-reliability markets like Israel, and into the OEM market with our IMS business.
And we’ve got a lot of new things coming: You’ve seen our development in IMS, you’ve seen our development in polyimide, and you’ve seen our branding and development in the high-speed low-loss. And then of course at DesignCon in Santa Clara in 2017 we’re going to launch the next big step in our high-speed low-loss portfolio of products, which should hopefully be a springboard for the next 10 years of our development in the overseas business.
Starkey: Thanks, Mark. You’ve certainly got a 10-year success story you can be proud of. And I am sure that Ventec Europe will continue to go from strength to strength over the next decade. Happy anniversary!
Footnote from Starkey: From my perspective, one thing that definitely hasn’t changed over the last 10 years is the commitment of the Ventec team, reinforcing Mark Goodwin’s plain-talking, hard-nosed determination to see Ventec recognised as the world leader in quality-assured high-reliability laminates: manufacture, supply-chain management and customer support.
Suggested Items
Insulectro & Dupont Host Technology Symposium at Silicon Valley Technology Center June 25
06/22/2025 | InsulectroInsulectro, the largest distributor of materials for use in the manufacture of PCBs and printed electronics, and DuPont, a major manufacturer of flex laminates and chemistry, invite fabricators, OEMS, designers, and engineers to attend an Innovation Symposium – Unlock the Power - this Wednesday, June 25, at DuPont’s Silicon Valley Technology Center in Sunnyvale, CA.
Ventec Strengthens Commitment to Halogen-Free PCB Manufacturing in Europe
06/11/2025 | Ventec International GroupVentec International Group, the PCB materials innovator, manufacturer, supplier and one-stop shop for copper clad laminates, prepregs, as well as process consumables and PCB manufacturing equipment has established volume inventory of halogen-free FR4.1 and FR15.1 PCB materials at its European hub in Germany.
Ventec International Group Enters into a Fulfillment and Supply Agreement with Matrix and Launches Ventec Americas
06/09/2025 | Ventec International GroupVentec is excited to announce a new partnership with Matrix aimed at enhancing the fulfillment, value-added conversion, and distribution of PCB base materials across the North American market. This collaboration is set to significantly improve supply chain efficiency, and delivery performance for the company's North American customers.
Panasonic Appoints Matrix as its Authorized Distributor in Europe
06/03/2025 | Matrix ElectronicsEffective July 1st, 2025, Panasonic Industry Co., Ltd. has appointed Matrix Electronics Limited as its Authorized Distributor in the European region.
From DuPont to Qnity: A Bold Move in Electronics Materials
05/14/2025 | Marcy LaRont, I-Connect007DuPont has announced the intended spinoff of a public independent electronics company, Qnity, which will serve as a solutions provider to the semiconductor and electronics industries to enhance competitiveness and innovation in advanced computing, smart technologies, and connectivity. In this interview, Jon Kemp, Qnity CEO-elect and current president of DuPont’s Electronics business, shares his insights on the strategic separation from DuPont.