-
- News
- Books
Featured Books
- smt007 Magazine
Latest Issues
Current IssueWhat's Your Sweet Spot?
Are you in a niche that’s growing or shrinking? Is it time to reassess and refocus? We spotlight companies thriving by redefining or reinforcing their niche. What are their insights?
Moving Forward With Confidence
In this issue, we focus on sales and quoting, workforce training, new IPC leadership in the U.S. and Canada, the effects of tariffs, CFX standards, and much more—all designed to provide perspective as you move through the cloud bank of today's shifting economic market.
Intelligent Test and Inspection
Are you ready to explore the cutting-edge advancements shaping the electronics manufacturing industry? The May 2025 issue of SMT007 Magazine is packed with insights, innovations, and expert perspectives that you won’t want to miss.
- Articles
- Columns
- Links
- Media kit
||| MENU - smt007 Magazine
Rework and Repair Standard Getting Updated
December 13, 2016 | Bob Wettermann, BEST Inc.Estimated reading time: 2 minutes
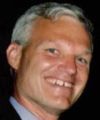
The IPC-7711/21 Rework of Electronic Assemblies/Repair and Modification of Printed Boards and Electronic Assemblies is being “upreved” from version “B” to version “C” and will soon be released to the industry. There are a couple of notable changes that strengthened, modernized and brought together changes from the previous “B” version, which was approved in 2007.
Several of the changes from the previous version deal with the manner in which leadless devices are being reworked. Leadless devices have become the most widely placed in terms of units worldwide. In addition to the methods previously described when the initial version of the IPC7711/21 “B” came out, the new “C” version includes three new methods, summarized below:
- Method 5.8.1.1: Prebumping the leadless device using a polyimide stencil
- Method 5.8.1.2: Prebumping the device using polyimide stencils with the “bumped” component then fitting in to stay-in-place capturing stencil on the rework location on the PCB
- Method 5.8.1.3: Hand bumping center ground and hand soldering the IO connection method
Another area in which some newer rework techniques are memorialized in the new “C” version are the various pad repair techniques including:
- Method 4.7.4: Land repair land with integral via repair film method which leans on the previous repair film method for pad repair
- Method 4.7.5: SMT/BGA land repair with integral via repair circuit extension film adhesive method
Other areas of change for this “C” version include:
Method 3.9.1.2 focused IR for BGA rework and Method 5.7.12 focused IR placement of BGAs. These changes mirror the inroads that IR rework have made since the B standard as the focused heating is important for ever higher board part densities and the continuing proliferation of underfilled devices, very small devices and highly temperature sensitive devices finding their way onto PCBs.
In addition to the above procedure upgrades there are a variety of other changes due to operations running in a mixed alloy environment of both lead-free and tin-lead solders. One of the changes with the IPC 7711/21 has to do with the segregation of the hand soldering equipment limiting cross-contamination. These changes are due to there being significant rework differences between the processing of these two alloy types. The major differences in processing these alloys which impact rework operations are the fluxes being used, the cleaning materials being used and the longer soldering dwell times which may or may not require the addition of the nitrogen in to the rework/repair operations. The higher reflow temperatures of the lead-free solders requires that the device in proximity to the rework location needs to be protected from thermal damage.
There are also a couple of newer proposed methods up for consideration which did not make this version of the standard and will have to wait for Version “D” or beyond. These include:
- Flex circuit repair
- New micro blasting method for coating removal
- New method for solder mask replacement
Keep a watch out on the IPC website as this revised standard makes its way to being available or speak with your training services provider.
To read this entire article, which appeared in the December 2016 issue of SMT Magazine, click here.
Suggested Items
Driving Innovation: Direct Imaging vs. Conventional Exposure
07/01/2025 | Simon Khesin -- Column: Driving InnovationMy first camera used Kodak film. I even experimented with developing photos in the bathroom, though I usually dropped the film off at a Kodak center and received the prints two weeks later, only to discover that some images were out of focus or poorly framed. Today, every smartphone contains a high-quality camera capable of producing stunning images instantly.
Hands-On Demos Now Available for Apollo Seiko’s EF and AF Selective Soldering Lines
06/30/2025 | Apollo SeikoApollo Seiko, a leading innovator in soldering technology, is excited to spotlight its expanded lineup of EF and AF Series Selective Soldering Systems, now available for live demonstrations in its newly dedicated demo room.
Indium Corporation Expert to Present on Automotive and Industrial Solder Bonding Solutions at Global Electronics Association Workshop
06/26/2025 | IndiumIndium Corporation Principal Engineer, Advanced Materials, Andy Mackie, Ph.D., MSc, will deliver a technical presentation on innovative solder bonding solutions for automotive and industrial applications at the Global Electronics A
Fresh PCB Concepts: Assembly Challenges with Micro Components and Standard Solder Mask Practices
06/26/2025 | Team NCAB -- Column: Fresh PCB ConceptsMicro components have redefined what is possible in PCB design. With package sizes like 01005 and 0201 becoming more common in high-density layouts, designers are now expected to pack more performance into smaller spaces than ever before. While these advancements support miniaturization and functionality, they introduce new assembly challenges, particularly with traditional solder mask and legend application processes.
Knocking Down the Bone Pile: Tin Whisker Mitigation in Aerospace Applications, Part 3
06/25/2025 | Nash Bell -- Column: Knocking Down the Bone PileTin whiskers are slender, hair-like metallic growths that can develop on the surface of tin-plated electronic components. Typically measuring a few micrometers in diameter and growing several millimeters in length, they form through an electrochemical process influenced by environmental factors such as temperature variations, mechanical or compressive stress, and the aging of solder alloys.