-
- News
- Books
Featured Books
- pcb007 Magazine
Latest Issues
Current IssueThe Hole Truth: Via Integrity in an HDI World
From the drilled hole to registration across multiple sequential lamination cycles, to the quality of your copper plating, via reliability in an HDI world is becoming an ever-greater challenge. This month we look at “The Hole Truth,” from creating the “perfect” via to how you can assure via quality and reliability, the first time, every time.
In Pursuit of Perfection: Defect Reduction
For bare PCB board fabrication, defect reduction is a critical aspect of a company's bottom line profitability. In this issue, we examine how imaging, etching, and plating processes can provide information and insight into reducing defects and increasing yields.
Voices of the Industry
We take the pulse of the PCB industry by sharing insights from leading fabricators and suppliers in this month's issue. We've gathered their thoughts on the new U.S. administration, spending, the war in Ukraine, and their most pressing needs. It’s an eye-opening and enlightening look behind the curtain.
- Articles
- Columns
- Links
- Media kit
||| MENU - pcb007 Magazine
Panasonic Commercializes Low Transmission Loss Flexible Multi-layer Circuit Board Materials
January 17, 2017 | Panasonic CorporationEstimated reading time: 4 minutes
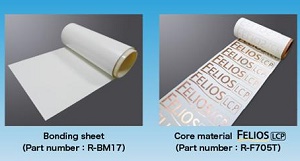
Panasonic Corporation announced today that it has commercialized its Low Transmission Loss[1] Flexible Multi-layer Circuit Board Materials, suitable for high-speed large-volume data transmission and thinner designs of mobile devices, including smartphones and tablet computers. The company will launch its mass production in January 2017. The combination of a liquid-crystal polymer (LCP) core material[2] and a bonding sheet material that can be laminated at a low temperature and stored at room temperature will considerably ease the manufacture of high-frequency flexible multi-layer circuit boards.
Existing coaxial cables used for large-volume transmission are thick, so they present an obstacle to making mobile devices thinner. Low transmission loss flexible multi-layer circuit boards are of increasing potential as a solution that achieves both large-volume data transmission and a thin design, but they face many restrictions in how they should be handled, due to the characteristics of the materials they incorporate, so they require special facilities for manufacturing. Using its unique resin design technologies, Panasonic has developed a bonding sheet that can be laminated at a low temperature of less than 200 °C and stored at room temperature. This eliminates the need for special facilities for high-temperature lamination and refrigerated storage for bonding sheets. The company has also achieved high adhesiveness of LCP and low profile copper foil for the LCP core material by using its unique laminating techniques. Although existing flexible core materials using polyimide and so on are usable for only low-speed transmission, the new material, due to its low transmission loss property can also be used for high-speed transmission of large-volume data.
Panasonic's new flexible multi-layer circuit board materials have the following features:
- Low transmission loss and compatibility with USB 3.1 Gen 2 (10 Gbps) enable the transmission of large-volume data at higher speeds
- Transmission loss: -2 dB/100 mm @ 6 GHz*1.
- Core material: Dielectric constant: 2.9 @ 10 GHz, dissipation factor: 0.002 @ 10 GHz
- Bonding sheet: Dielectric constant: 2.2 @ 10 GHz, dissipation factor: 0.001 @ 10 GHz
- Flexible multi-layer circuit board adopts a 3-layer structure with multiple of signal lines at a thickness of 0.2 mm, allowing further thinning of mobile devices.
- Total board thickness: 0.2 mm or less(1)
- Circuit board material that can be laminated at a low temperature and stored at room temperature makes manufacturing of flexible multi-layer circuit boards easier.
- Lamination temperature: 180 - 200°C, existing bonding sheet(2): 300°C
- Room-temperature storage: 23 (±5) °C, existing bonding sheet(3): refrigerated storage: 5°C or below
(2) Panasonic's conventional LCP bonding sheet
(3) Ordinary low-dielectric constant bonding sheet
Suitable applications:
Circuit boards for high-frequency antenna modules, high-speed cables, etc.
Panasonic Technology
1. Low transmission loss and compatibility with USB 3.1 Gen 2 (10 Gbps) contribute to transmission of large-volume data at higher speeds
There is a growing need for faster transmission of signals due to the increasing volume of data demanded by the ever-higher resolutions of mobile device cameras and display screens. As a result, low transmission loss flexible multi-layer circuit boards that enable large-volume, high-speed transmission are of increasing interest as a replacement for currently-used coaxial cables; and low transmission loss, meaning that only a small amount of the signal is lost during transmission, is desired for the circuit board material. Panasonic has commercialized a low transmission loss core material and bonding sheet by applying its unique resin design technologies. It supports standards including USB 3.1 Gen 2 (10 Gbps) and will enable increased speed of large-volume data transmission in mobile devices.
2. Flexible multi-layer circuit board comprising a 3-layer, 0.2 mm-thick structure with multiple signal lines contributes to thinner mobile device designs
A coaxial cable is composed of one signal line in a cable and is capable of large-volume data transmission, but its downside is its thickness. A low transmission loss flexible multi-layer circuit board has several signal lines within it, so large-volume data transmission and a thinner design can be achieved simultaneously. Adopting this material allows flexible multi-layer circuit boards, in a 0.2 mm-thick, 3-layer structure that can carry several signal lines, to replace coaxial cables.
3. Circuit board material that can be laminated at a low temperature and stored at room temperature facilitates the manufacture of flexible multi-layer circuit boards
Previous bonding sheet, which forms the low transmission loss flexible multi-layer circuit boards with core material, had to be laminated at a high temperature or stored refrigerated. It was also difficult to handle, due to its material characteristics, and required special facilities that placed a burden on manufacturers. Using its unique resin design technologies, Panasonic has developed a bonding sheet that can be laminated at a low temperature of 200 °C or less, and stored at room temperature, making it far easier to handle the material during production. By providing this sheet and the low-transmission loss core material, the company will considerably facilitate the production of flexible multi-layer circuit boards.
Basic specifications
About Panasonic
Panasonic Corporation is a worldwide leader in the development of diverse electronics technologies and solutions for customers in the consumer electronics, housing, automotive, enterprise solutions and device industries. Since its founding in 1918, the company has expanded globally and now operates 474 subsidiaries and 94 associated companies worldwide, recording consolidated net sales of 7.553 trillion yen for the year ended March 31, 2016. Committed to pursuing new value through innovation across divisional lines, the company uses its technologies to create a better life and a better world for its customers. To learn more about Panasonic, click here.
Suggested Items
The Evolution of Picosecond Laser Drilling
06/19/2025 | Marcy LaRont, PCB007 MagazineIs it hard to imagine a single laser pulse reduced not only from nanoseconds to picoseconds in its pulse duration, but even to femtoseconds? Well, buckle up because it seems we are there. In this interview, Dr. Stefan Rung, technical director of laser machines at Schmoll Maschinen GmbH, traces the technology trajectory of the laser drill from the CO2 laser to cutting-edge picosecond and hybrid laser drilling systems, highlighting the benefits and limitations of each method, and demonstrating how laser innovations are shaping the future of PCB fabrication.
Day 2: More Cutting-edge Insights at the EIPC Summer Conference
06/18/2025 | Pete Starkey, I-Connect007The European Institute for the PCB Community (EIPC) summer conference took place this year in Edinburgh, Scotland, June 3-4. This is the third of three articles on the conference. The other two cover Day 1’s sessions and the opening keynote speech. Below is a recap of the second day’s sessions.
Day 1: Cutting Edge Insights at the EIPC Summer Conference
06/17/2025 | Pete Starkey, I-Connect007The European Institute for the PCB Community (EIPC) Summer Conference took place this year in Edinburgh, Scotland, June 3-4. This is the second of three articles on the conference. The other two cover the keynote speeches and Day 2 of the technical conference. Below is a recap of the first day’s sessions.
Preventing Surface Prep Defects and Ensuring Reliability
06/10/2025 | Marcy LaRont, PCB007 MagazineIn printed circuit board (PCB) fabrication, surface preparation is a critical process that ensures strong adhesion, reliable plating, and long-term product performance. Without proper surface treatment, manufacturers may encounter defects such as delamination, poor solder mask adhesion, and plating failures. This article examines key surface preparation techniques, common defects resulting from improper processes, and real-world case studies that illustrate best practices.
RF PCB Design Tips and Tricks
05/08/2025 | Cherie Litson, EPTAC MIT CID/CID+There are many great books, videos, and information online about designing PCBs for RF circuits. A few of my favorite RF sources are Hans Rosenberg, Stephen Chavez, and Rick Hartley, but there are many more. These PCB design engineers have a very good perspective on what it takes to take an RF design from schematic concept to PCB layout.