-
- News
- Books
Featured Books
- smt007 Magazine
Latest Issues
Current IssueMoving Forward With Confidence
In this issue, we focus on sales and quoting, workforce training, new IPC leadership in the U.S. and Canada, the effects of tariffs, CFX standards, and much more—all designed to provide perspective as you move through the cloud bank of today's shifting economic market.
Intelligent Test and Inspection
Are you ready to explore the cutting-edge advancements shaping the electronics manufacturing industry? The May 2025 issue of SMT007 Magazine is packed with insights, innovations, and expert perspectives that you won’t want to miss.
Do You Have X-ray Vision?
Has X-ray’s time finally come in electronics manufacturing? Join us in this issue of SMT007 Magazine, where we answer this question and others to bring more efficiency to your bottom line.
- Articles
- Columns
- Links
- Media kit
||| MENU - smt007 Magazine
Estimated reading time: 4 minutes
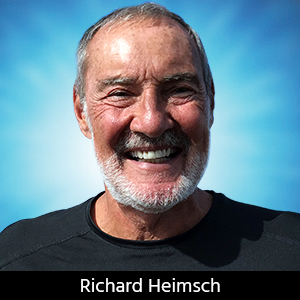
More Than Just Dry Air: Prodrive Technologies - 4.0 in Action
Headquartered in Eindhoven, Netherlands, Prodrive Technologies is a global provider of world-class technical products, systems, and automation solutions. From servo drives to automated guided vehicles (AGVs), Prodrive builds it, and creating their own factory of the future has been a significant part of their success.
At a time when numerous companies around them chose to move their manufacturing to lower cost geographies, Prodrive decided instead to develop and integrate automation solutions for the production of their high mix, low to high volume products. With a strong focus on quality, flexibility, and productivity, they have proven to possess a globally competitive production environment—located in Western Europe. From the moment Prodrive Technologies started with in-house production, they viewed automation in an unconventional way. Working in a dynamic industry and producing over a thousand different products every year demands flexible automation. They believe that critical focus for successful automation must be trained upon the processes and not the products. With this philosophy, over a thousand different products are being handled by the same automated processes.
Creating their own systems that support or improve the production processes is one of Prodrive Technologies’ core competences. The Prodrive Technologies AGVs are a good example of an in-house development, taking care of the intelligent transport of components and products. The AGVs are not only used to optimize their internal processes, but are now also available for outside sale. Prodrive Technologies is a fast-growing company with a high diversity in products, which makes flexibility in transport essential. After an extensive market research, Prodrive Technologies decided to develop their own AGVs that actually provide the flexible and intelligent transport needed. Taking care of the transport, the AGVs increase Prodrive Technologies’ productivity and enable 24/7 production without human interference. They navigate without supporting infrastructure through the factory, finding their way from pick-up locations to drop-off locations.
In this age, smart minded companies continuously search for flexible automation and digitalization of their processes. Track and trace become essential parts of every automation process. Industry 4.0 is a good example of an initiative that helps companies getting ready for the next industrial revolution, focusing on flexible automation, digitalization, and track and tracing throughout the whole supply chain. Embracing these ideas in such a way has enabled manufacturing in Europe be globally competitive and significant amounts of manual labor redeployed. Prodrive developed a components logistic process for printed circuit board assembly that is completely automated and digitized and had increased their productivity enormously.
Figure 1: Prodrive Technologies' AGVs navigate without supporting infrastructure through the factory, finding their way from pick-up locations to drop-off locations.
The Component Tape Flow
Every electronics manufacturer deals with large numbers of components used in the production process. These components are placed on component tapes that can be used by the pick and place machines for PCB assembly. Current technology has advanced such that this flow of component tapes is fully automated, from inbound to the moment they are ready to be loaded onto the pick and place machines. Even more important, processes are set up in a way that provides complete tracking and tracing of the components at all times, eliminating manual handling and reducing errors.
This automated process is set-up as follows. All incoming reels are handed to a robot that is able to automatically recognize tapes using vision technology. With 3D vision, it recognizes specific characteristics of the reels and scans the unique barcode. The reel gets a unique serial number and the component information is automatically logged into the ERP system. Placed in a standardized carrier, they are ready to be transported to storage locations. For the most efficient process, multiple trays are stacked by a robot cells. Automated guided vehicles (AGV) were chosen for transportation because they are systems that take care of transportation in both an automated and autonomous way.
AGVs deliver reels or trays to the central, robotically manned “warehouse.” This warehouse is environmentally controlled for both humidity and temperature, enabling the intricate management of all moisture sensitive components. The component tapes are being delivered by the AGVs to selected entry points. Reels are identified and the type and floor life (both exposed and remaining) are immediately known. Five-axis robots then place each reel into a best fit location. Best fit not only physically, but with respect to the components’ MSL and floor life exposure, which may mean
When a reel is needed for production, it will be automatically located, selected and handed out to the operator, who puts it into a feeder that is used to place the tapes in the aforementioned AGVs. Feeder carriers are specially designed to increase the tracking and tracing of components throughout the logistic process. Every slot of the feeder carrier has an own identity and is connected with the manufacturing execution system (MES). Using the location information in an intelligent way for smart scheduling and assignment of the slots, the operator handling time and the margin of error with tapes and feeders is reduced substantially. Having supporting systems like the feeder carrier also prevents loss of tapes which causes searching time and mistakes like placing the wrong tape on the machines.
The final step before PCB assembly is placing the feeders with the tapes into the pick and place machines. The process has reduced manual handling to only two steps, the remainder is completely automatic.
The Benefits
During the whole process, there is real-time insight of component locations and production process status. Using real-time information to prepare future production batches not only gives a huge productivity increase, it also helps reducing product lead times and increases flexibility. The margin of error is being eliminated by a real-time control of the MES and ERP. By continuously investing in intelligent automation and productivity, the setup of this process is a real-world example of how to build the factory of the future.
More Columns from More Than Just Dry Air
Controlling Oxidation and Intermetallics in Moisture-sensitive DevicesPCBs are MSDs
Long-Term Storage of Electronic Components and Compositions
More Than Just Dry Air: Solutions for Long-term Storage of Electronic Components and Compositions
More Than Just Dry Air: In Pursuit of 4.0
More Than Just Dry Air: Controlling Oxidation and Intermetallics in Moisture-Sensitive Devices