-
- News
- Books
Featured Books
- pcb007 Magazine
Latest Issues
Current IssueThe Hole Truth: Via Integrity in an HDI World
From the drilled hole to registration across multiple sequential lamination cycles, to the quality of your copper plating, via reliability in an HDI world is becoming an ever-greater challenge. This month we look at “The Hole Truth,” from creating the “perfect” via to how you can assure via quality and reliability, the first time, every time.
In Pursuit of Perfection: Defect Reduction
For bare PCB board fabrication, defect reduction is a critical aspect of a company's bottom line profitability. In this issue, we examine how imaging, etching, and plating processes can provide information and insight into reducing defects and increasing yields.
Voices of the Industry
We take the pulse of the PCB industry by sharing insights from leading fabricators and suppliers in this month's issue. We've gathered their thoughts on the new U.S. administration, spending, the war in Ukraine, and their most pressing needs. It’s an eye-opening and enlightening look behind the curtain.
- Articles
- Columns
- Links
- Media kit
||| MENU - pcb007 Magazine
Estimated reading time: 5 minutes
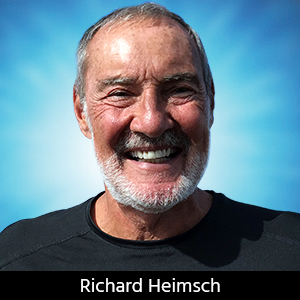
Controlling Oxidation and Intermetallics in Moisture-sensitive Devices
To avoid the damage of microcracks and delamination during the processing of electronic components, appropriate environmental storage is essential. The introduction of lead-free soldering and the associated higher processing temperatures involved makes moisture management even more important. Lead-free reflow increases the consequent saturated vapor pressure within components considerably (up to 30 bars). The same component that could be safely processed before lead-free becomes a moisture sensitive device with limited floor life. The difference is often two moisture sensitivity levels (MSLs) higher in classification, and shorter allowable exposure time (floor life).
Component suppliers should deliver these moisture sensitive components in effective protective packaging to avoid absorption of humidity during transport and storage. These moisture barrier bags (MBBs) are made from multiple layers of plastic and aluminum. Properly prepared and sealed, they are also a protective packaging that can prevent oxidation. ESD bags or zippered plastic bags do not protect against moisture. After opening the package, the time begins during which the components absorb humidity. Depending on ambient humidity and temperature, the components can be safely used only within a limited time period. This time period is classified by the IPC/JEDEC J-STD-033D.
When a component has exceeded the allowed exposure time, the component can be dried and made safe again through a baking process, traditionally done at 125°C. The component should be processed especially carefully after that. Repeated absorption of humidity must be avoided because the baking process should not be repeated. Even one exposure to baking at these temperatures induces oxidation and intermetallic growth, which reduces the wetting ability of the connection surfaces. Intermetallic thickness has been shown to increase by approximately 50% when baking at 125°C for four days. Thicker intermetallic layers can lead to a reduction in solder joint integrity, and in extreme cases, reduce solderability.
Figure 1: Copper sample.
To fight this well-known effect, many suppliers of baking ovens provide an additional reduction of oxygen by means of a nitrogen atmosphere or vacuum during the drying process. Setting the clock back to zero for the component can take in excess of 72 hours, inevitably bringing along considerable costs for nitrogen. Only a low-rest oxygen content of less than 13 ppm stops the oxidation.
Long-term Storage of Obsolete Components
Product lifecycles are very short with new models being released sooner than ever before. Many manufacturers in industries including automotive, aviation, military, and avionics must guarantee the availability of replacement parts (including PCBs) for 10 or even 20 years. This demands the advance purchase and extended storage of components and materials. Further complicating the problem is that most components cannot be stored for more than a few years without very special handling procedures. Oxidation, intermetallics, and embrittlement are just a few of the conditions that must be addressed.
Figure 2: AgCu50 solder material.
IPC/JEDEC J-STD-033D addresses a broad range of fundamentals regarding moisture sensitive devices and their proper handling, but very long-term storage is not addressed.
Also, the obsolescence of components and ever-shortened product life cycles forces manufacturers to build up an appropriate stock for further production and spare parts supply. Various ageing processes on electronic components show that storage in dry packs (also under nitrogen atmosphere) cannot guarantee reliability in the future.
Besides temperature, humidity is the strongest negative influence on the surface oxidation of metals. Due to oxidation, the components are more difficult to wet and cause more soldering defects, which can lead to failure of the entire assembly.
Corrosion Protection Ensures Quality in the Long Term
Two conditions must always be met for metal corrosion to occur. An oxidizing agent must be present, which is provided by the 21% oxygen content of the air. The second prerequisite is an aqueous solution that acts as an electrolyte. The electrolyte forms above a humidity of 10% relative humidity in the form of a thin, invisible water film on the metal surface [1].
Figure 3: AgCu28 solder material.
As soon as one of these components of the oxidation reaction is missing, the corrosion stops. Three processes are common for this. Storage in a dry pack and/or under nitrogen removes both the oxidant and electrolyte from the storage atmosphere. Storage in a dry atmosphere only removes the electrolyte. But what is the more effective protection against oxidation?
The dry pack is only suitable for short- to medium-term storage because there is a risk that outgassing will lead to corrosion effects on the contact surfaces. These are usually plasticizers and flame retardants, which can reach high concentrations within the bags. This effect does not occur with nitrogen and dry storage because the storage atmosphere is permanently filtered or replaced.
Direct Comparison of Nitrogen and Dry Storage
To determine the oxidation rate under the two storage conditions, a long-term test (over nine months) was carried out. At regular intervals (every four weeks) the samples were examined for oxidation by EDX analysis. In parallel, the same materials were stored as a reference under ambient air.
Figure 4: Ag sample.
For each material, there is a diagram showing the development of the percentage oxygen peak height compared to the respective main peak as a function of the storage time. This comparison is permissible insofar as all EDX spectra were recorded under the same measuring conditions (high voltage, the running time of the analysis, the aperture setting, and the sample distance to the detector) [2–6].
Test Evaluation Storage Atmosphere
As expected, the highest O2 peaks, and thus the highest surface oxidation, could be measured on the samples stored under air. When comparing the samples stored in N2 and dry air, it is noticeable that the lowest O2 peaks and surface oxidation occur during dry storage. The results of this long-term test prove that dry storage can be classified as very suitable for long-term storage due to its optimal oxidation protection [2–6]. Dry storage is preferable to nitrogen storage not only in terms of quality but also in terms of energy consumption [7].
Influence of Temperature on Ageing Rate
In addition to corrosion, the components age through diffusion processes at metallic boundary layers. Each temperature increase leads to an increase in the ageing rate due to an increase in the reaction rate. A rule of thumb predicts a doubling to quadrupling of the ageing rate with a temperature increase of 10K. The physical and chemical processes are described in more detail with the Arrhenius equation. For this reason, it is recommended to reduce the storage temperature as much as possible during long-term storage. However, there are also negative effects such as whisker formation and tin pest that increase with decreasing temperature. To avoid this, store components at 14°C above the critical temperature of 13.2°C. The temperature of the components is then reduced to a minimum.
References
1. Jacobus Henricus van’t Hoff. Études de dynamique chimique. Frederik Muller & Co., 1884, pp. 114–118.
2. Svante Arrhenius. Zeitschrift für Physikalische Chemie. 1889, pp. 226–248.
3. International Union of Pure and Applied Chemistry (IUPAC). Compendium of Chemical Terminology: Gold Book. 2014.
4. Karl Müller & Karl-Helmut Tostmann. Lehrbuch der Metallkorrosion. Lehrbuchreihe Galvanotechnik, 2017, pp. 32–33.
5. M. Roggenbuck & M. Haubner. “Qualification Drying Storage Cabinets.” Thales Electron Devices GmBH, 2018.
6. ZVEI Die Elektroindustrie. “Guideline for the Long- Term Storage of Components, Subassemblies and Devices.” 2014, p. 10.
7. Super Dry Totech GmbH. “Cost Comparison.” 2013.
More Columns from More Than Just Dry Air
PCBs are MSDsLong-Term Storage of Electronic Components and Compositions
More Than Just Dry Air: Solutions for Long-term Storage of Electronic Components and Compositions
More Than Just Dry Air: Prodrive Technologies - 4.0 in Action
More Than Just Dry Air: In Pursuit of 4.0
More Than Just Dry Air: Controlling Oxidation and Intermetallics in Moisture-Sensitive Devices