-
- News
- Books
Featured Books
- pcb007 Magazine
Latest Issues
Current IssueThe Hole Truth: Via Integrity in an HDI World
From the drilled hole to registration across multiple sequential lamination cycles, to the quality of your copper plating, via reliability in an HDI world is becoming an ever-greater challenge. This month we look at “The Hole Truth,” from creating the “perfect” via to how you can assure via quality and reliability, the first time, every time.
In Pursuit of Perfection: Defect Reduction
For bare PCB board fabrication, defect reduction is a critical aspect of a company's bottom line profitability. In this issue, we examine how imaging, etching, and plating processes can provide information and insight into reducing defects and increasing yields.
Voices of the Industry
We take the pulse of the PCB industry by sharing insights from leading fabricators and suppliers in this month's issue. We've gathered their thoughts on the new U.S. administration, spending, the war in Ukraine, and their most pressing needs. It’s an eye-opening and enlightening look behind the curtain.
- Articles
- Columns
- Links
- Media kit
||| MENU - pcb007 Magazine
Estimated reading time: 4 minutes
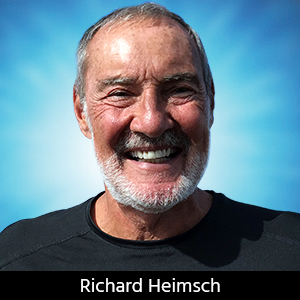
Long-Term Storage of Electronic Components and Compositions
In part one of this series, we reviewed some of the reasons why long term storage of electronic components is both a problematic, as well as an increasing requirement for many electronic assemblers.
Rapid changes in packaging design and material force companies to purchase forward quantities to guard against the impact of component obsolescence on their final product.
Product lifecycles have become very short with new models being released sooner than ever before. Many manufacturers in industries including automobiles, aviation and avionics, military and railway must guarantee the availability of replacement parts (including PCBs) for 10 or even 20 years. This demands the advance purchase and extended storage of components and materials. Further complicating the problem is that most components cannot be stored for more than a few years without very special handling procedures.
IPC JEDEC Standards
Though the original document was released almost two decades ago, and new technologies have been introduced since, IPC/JEDEC J-STD-033 addresses a broad range of fundamentals regarding moisture-sensitive devices and their proper handling. Updated several times since its initial publication, the 2012 Rev C clarified some storage time definitions, but very long term storage of the extent faced by manufacturers mentioned above is not completely addressed.
5.3 Safe Storage: Safe storage means dry SMD packages held in a controlled humidity condition such that the floor-life clock remains at zero. Acceptable safe storage conditions for SMD packages classified as Level 2 through 5a are listed below.
5.3.1 Dry Pack: Dry-packed SMD packages in intact MBBs, stored per Clause 3.3, shall have a calculated shelf life of at least 12 months from the bag seal date shown on the caution or bar code label.
5.3.2 Shelf Life: The minimum calculated shelf life is 12 months from bag seal date. If the actual shelf life has exceeded 12 months, but less than two years, from the bag seal date and the humidity indicator card (HIC) (Clause 5.5.1) indicates that baking is not required, then it is safe to reflow the components per the original MSL rating. Although unanticipated, factors other than moisture sensitivity could affect the total shelf life of components.
Note: An HIC that has been continuously sealed in the MBB is typically accurate for at least two years.
5.3.3 Dry Atmosphere Cabinet: A storage cabinet which maintains low humidity by purging with dry air or nitrogen at 25 ± 5°C. The cabinet must be capable of recovering to its stated humidity rating within one hour from routine excursions such as door opening/closing.
- 5.3.3.1 Dry cabinet at 10% RH SMD packages not sealed in a MBB may be placed in a dry atmosphere cabinet, maintained at not greater than 10% RH. A dry cabinet should not be considered a MBB. Storage of SMD packages in a dry cabinet should be limited to a maximum time per Table 7-1. If the time limit is exceeded the packages should be baked according to Table 4-2 to restore the floor life.
- 5.3.3.2 Dry cabinet at 5% RH SMD packages not sealed in a MBB may be placed in a dry atmosphere cabinet, maintained at not greater than 5% RH. Storage in a dry cabinet may be considered equivalent to storage in a dry pack with unlimited shelf life.
These guidelines address moisture within the component and mitigation of risks during reflow, but the solderabilty of components is also a significant consideration.
Because of surface oxidation, components and PCBs can suffer from reduced solderablity, which often results in complete failure. Diffusion of vapor and noxious substances in the inner structure of the components or PCBs can result in long-term disintegration of conductor paths and insulation layers. Both risks can be avoided by correct handling and dry storage.
The Oxidation Process—Contact Corrosion
In an ultra-dry atmosphere there is no corrosion. For corrosion to occur, two demands must be met: there must be a means of oxidation, and there must be a watery solution, which works as an electrolyte. The oxygen in the air forms the means of oxidation, the vapor (humidity) the electrolyte. The critical limit at which oxidation with oxygen takes place, depending upon the metal or alloy, at between 40 and 70% RH. This means that more than eight grams of vapor per m3 must be present. As a side note, 0.5% RH, used commonly today, reduces water content to 0.05 grams per m3.
The effects of long-term storage on the solderabilty of components was studied in some detail by DFR Solutions, including in one titled "Solderability After Long Term Storage." In this case study, the solderability was assessed for components from three different reels stored for up to five years to determine how much additional storage life was available. The components were either an ASIC in a SOIC package or a MOSFET in a TO-252 package. In both situations, the lead frame plating was tin-based1.
Both oxidation and intermetallic formation occurred, as would be expected for the reasons described previously. Oxidation can be prevented with the use of low humidity storage, or potentially mitigated with the implementation of more aggressive fluxes.
Intermetallics, however, cannot be addressed in either of the same ways. Temperature therefore is an extremely critical parameter to control during long-term storage. Intermetallic growth rate is strongly temperature-dependent and doubles for each 10°C temperature increase. This aging process can be slowed by appropriate cooling. However, the risk of whisker formation of tin alloys increases with decreasing temperature. Studies and practice have shown that a storage temperature of 12°C is optimal to best mitigate both risks, while maintaining a storage humidity of <5% to arrest oxidation and preserve solderability.
References
1. Joelle Arnold, Cheryl Tulkoff, Greg Caswell, DFR Solutions, “Solderability after Long-Term Storage.”
More Columns from More Than Just Dry Air
Controlling Oxidation and Intermetallics in Moisture-sensitive DevicesPCBs are MSDs
More Than Just Dry Air: Solutions for Long-term Storage of Electronic Components and Compositions
More Than Just Dry Air: Prodrive Technologies - 4.0 in Action
More Than Just Dry Air: In Pursuit of 4.0
More Than Just Dry Air: Controlling Oxidation and Intermetallics in Moisture-Sensitive Devices