-
- News
- Books
Featured Books
- smt007 Magazine
Latest Issues
Current IssueSupply Chain Strategies
A successful brand is built on strong customer relationships—anchored by a well-orchestrated supply chain at its core. This month, we look at how managing your supply chain directly influences customer perception.
What's Your Sweet Spot?
Are you in a niche that’s growing or shrinking? Is it time to reassess and refocus? We spotlight companies thriving by redefining or reinforcing their niche. What are their insights?
Moving Forward With Confidence
In this issue, we focus on sales and quoting, workforce training, new IPC leadership in the U.S. and Canada, the effects of tariffs, CFX standards, and much more—all designed to provide perspective as you move through the cloud bank of today's shifting economic market.
- Articles
- Columns
- Links
- Media kit
||| MENU - smt007 Magazine
Assembly of Flexible Circuits
April 6, 2017 | John Talbot, Tramonto CircuitsEstimated reading time: 7 minutes
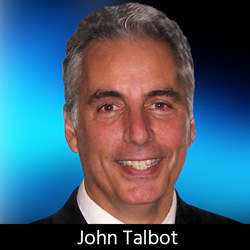
A flexible circuit assembly consists of a bare circuit with conductive patterns etched onto it that allow the attachment of components that, when completed, results in a working electronic product. Components are available in different shapes, sizes and methods of attachment. There are through-hole components that have wire leads that, as the description states, go through-holes in the circuit and are soldered. Surface mount components, intuitively, are placed on surface pads and soldered to the circuit. The number of different configurations of through-hole and surface mount components are vast. The typical method of attachment is by soldering the component to a conductive pattern. Some components are soldered one lead at a time by hand. Others are placed automatically by machine and run through an oven to solder the entire board at the same time. No matter the method, the assembly of electronic flexible circuits is tedious because of its inherent flexible nature. Therefore, we must give extra attention to the assembly process.
Flexible Circuits
Flexible circuits are made from a thin plastic substrate of polyimide or polyester. The most widely used material for flexible assemblies is polyimide (poly im id) because it can withstand the high temperatures required to solder components without negative effects. Polyester circuits shrivel up when exposed to those temperatures and make them less appropriate for flexible assemblies. The polyimide material is laminated to conductive layers and insulating layers with epoxy or acrylic based adhesives. The final product is a very thin, typically .010”, overall thickness. This is the characteristic that makes assembly on flexible circuits more difficult than traditional printed circuit boards which are 1/16” thick and sturdy. The inherent nature of a flexible circuit demands high attention to handling during the assembly process. Whether hand soldering or automated soldering, the circuits must be supported for consistent results. The discussion below will focus on the processes that will make any flexible circuit assembly successful.
Figure 1: Flexible circuit.
Moisture and Flexible Circuits
Before we can start any assembly on a flexible circuit, we must first bake out the moisture. This is done in a dry oven at low temperature for several hours. The intent is to evaporate all moisture that has been absorbed by the plastic and adhesive layers during storage. This is a bigger problem during the summer months when atmospheric humidity is high. Less of an issue during the dryer winter months. However, no matter the season, if the moisture is not baked out, negative results are possible.
When introduced to the high temperatures required to melt solder, 680°F to 750°F, the moisture trapped between the layers can boil quickly and cause the laminated layers to separate. Once the layers are separated the flexible circuit cannot be used reliably as it allows air into the circuit which contains water, that will eventually corrode and render the circuit useless. It is a prudent first step in any circuit assembly process to bake out the moisture.
Solder Choices for Assembly of Flexible Circuits
Before the year 2000, most circuit assemblies used solder that consisted of tin and lead. A popular ratio of the alloy was 63%tin and 37%lead. However, the European Union passed a directive named Restriction of Hazardous Substances, commonly known as RoHS, or Directive2002/95/EC. It restricted the use of lead, mercury, cadmium and other substances in products sold there. Electronic industries worldwide were affected and had to come up with a substitute for the tin/lead alloys that had been used for decades.
Today, both RoHS and non-RoHS solders exist and are used. A typical RoHS compliant solder will contain no lead and be made instead of tin, silver and copper. This new solder requires higher temperatures to melt than the tin/lead versions and looks differently as well.
Both RoHS and non-RoHS solders come mixed with flux that must be cleaned or flux that does not require to be cleaned. The flux in the version that requires cleaning is very corrosive and can be conductive if left on the circuit, but is easily cleaned with water. The flux in no-clean solder leaves an inert clear residue that may remain on the circuit forever without adverse effects. The use of these solder options on flexible circuits is common and generally requires no special considerations, aside from the melting temperature.
Hand or Manual Soldering Process
The hand or manual soldering process requires a skillful assembler to attach components to a flexible circuit one solder joint at a time. A compliant solder joint, defined by the governing body, IPC, makes no distinction for flexible circuits. The complications added to the solder process come from the thin flexible nature of the circuit. For instance, if a component is inserted or placed with too much pressure, the material can wrinkle and may create a void under the component that could allow foreign material to gather.
Figure 2: Hand solder.
Another concern during hand assembly is how to keep the circuit in a static condition so that it doesn’t move when the solder or iron is placed on the component. It’s difficult enough to solder components manually, but that difficulty is magnified when the circuit is not static. Trying to create a compliant solder joint on a moving target is the highest level of frustration.
Therefore, it is common to create fixtures to assist in the hand assembly of flexible circuits. The fixture is used to keep the circuit flat and still during the process. The fixture is an invaluable aid to the assembler.
Automated Soldering Process
The automated soldering process is typically done on multiple circuits designed in a matrix to form a panel. This panel can then have solder applied, go into a machine that will load all the components to their proper locations/orientations and finally run through an oven to solder the entire panel. This is much easier to describe than to put into practice.
Figure 3: Carrier panel.
The complications are many when flexible circuits are the point of discussion. The screening process and component placement puts a great deal of pressure on the circuit that requires tooling to be designed specifically for each circuit. A typical way to fixture a flexible panel is to create a “carrier” that is used to carry the circuit through the entire process. It provides a stable surface that assists in consistent assembly and eliminates much of the laborious tedium associated with the assembly of flexible circuits. With the use of carriers, the flexible circuit panel can run through the entire process with little or no issues.
Page 1 of 2
Testimonial
"We’re proud to call I-Connect007 a trusted partner. Their innovative approach and industry insight made our podcast collaboration a success by connecting us with the right audience and delivering real results."
Julia McCaffrey - NCAB GroupSuggested Items
Indium Corporation Promotes Two Leaders in EMEA (Europe, Middle East, and Africa) Markets
08/05/2025 | Indium CorporationWith its commitment to innovation and growth through employee development, Indium Corporation today announced the promotions of Andy Seager to Associate Director, Continental Sales (EMEA), and Karthik Vijay to Senior Technical Manager (EMEA). These advancements reflect their contributions to the company’s continued innovative efforts with customers across Europe, the Middle East, and Africa (EMEA).
MacDermid Alpha Electronics Solutions Unveils Unified Global Website to Deepen Customer, Talent, and Stakeholder Engagement
07/31/2025 | MacDermid Alpha Electronics SolutionsMacDermid Alpha Electronics Solutions, the electronics business of Elements Solutions Inc, today launched macdermidalpha.com - a unified global website built to deepen digital engagement. The launch marks a significant milestone in the business’ ongoing commitment to delivering more meaningful, interactive, and impactful experiences for its customers, talent, and stakeholders worldwide.
KOKI to Showcase Analytical Services and New HF1200 Solder Paste at SMTA Guadalajara 2025
07/31/2025 | KOKIKOKI, a global leader in advanced soldering materials and process optimization services, will exhibit at the SMTA Guadalajara Expo & Tech Forum, taking place September 17 & 18, 2025 at Expo Guadalajara, Salón Jalisco Halls D & E in Guadalajara, Mexico.
Weller Tools Supports Future Talent with Exclusive Donation to SMTA Michigan Student Soldering Competition
07/23/2025 | Weller ToolsWeller Tools, the industry leader in hand soldering solutions, is proud to announce its support of the upcoming SMTA Michigan Expo & Tech Forum by donating a limited-edition 80th Anniversary Black Soldering Set to the event’s student soldering competition.
Koh Young Appoints Tom Hattori as President of Koh Young Japan
07/21/2025 | Koh YoungKoh Young Technology, the global leader in True 3D measurement-based inspection solutions, announced the appointment of Tom Hattori as President of Koh Young Japan (JKY).