-
- News
- Books
Featured Books
- smt007 Magazine
Latest Issues
Current IssueIntelligent Test and Inspection
Are you ready to explore the cutting-edge advancements shaping the electronics manufacturing industry? The May 2025 issue of SMT007 Magazine is packed with insights, innovations, and expert perspectives that you won’t want to miss.
Do You Have X-ray Vision?
Has X-ray’s time finally come in electronics manufacturing? Join us in this issue of SMT007 Magazine, where we answer this question and others to bring more efficiency to your bottom line.
IPC APEX EXPO 2025: A Preview
It’s that time again. If you’re going to Anaheim for IPC APEX EXPO 2025, we’ll see you there. In the meantime, consider this issue of SMT007 Magazine to be your golden ticket to planning the show.
- Articles
- Columns
Search Console
- Links
- Media kit
||| MENU - smt007 Magazine
Fixturing: Key to Accurate Flex Circuit Assembly
April 17, 2017 | Stephen Las Marias, I-Connect007Estimated reading time: 3 minutes
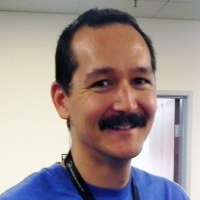
Adrian Nishimoto, operation manager at Spectrum Assembly Inc. (SAI), talks about the critical factors to consider during flex circuit assembly, such as fixturing and accurate thermal profiling. He also mentions why jet printers are suitable for use in assembling flex circuits.
Stephen Las Marias: What do you think are the major challenges in flex circuit assembly?
Adrian Nishimoto: Making our customers realize that fixturing is an integral part of successfully building flex circuits. We need good 3D Solidworks files, CAD or Gerber data to design carriers able to provide a rigid surface as the flex circuits go through stencil printing, pick-and-place and reflow. In some cases, we also use specialized carriers for aqueous wash system.
Las Marias: Please talk about specific steps in the flexible circuit assembly process that have the biggest effect on yields.
Nishimoto: Having tooling holes that keep the flex substrate rigid in a fixture during stencil printing and pick-and-place ensures better solder paste accuracy and component placement accuracy. The goal is to keep it flat and keep it from moving during these processes. The carrier is also critical if you have any type of conveyor system handling PCBAs in production.
Las Marias: How do you address these challenges? Does the process require different parameters?
Nishimoto: In addition to the fixturing considerations we’ve mentioned, accurate thermal profiling is also necessary. The carrier’s thermal mass impact—the ability to absorb and store heat—needs to be taken into consideration. We do have our suppliers drill material out of the carrier to make them more web-like and less of a heatsink. That said, there isn’t a one-size-fits-all solution to profiling because flex circuits come in all size ranges and that changes the optimum profile.
Las Marias: How does flex circuit assembly differ from standard PCB assembly?
Nishimoto: Because the material is flexible, all secondary operations need to use extra care in processing. If there are ceramic capacitors or other large ICs, it becomes important to make sure that the substrate is not flexed in handling because that will damage the solder joint.
Las Marias: What about the challenges with respect to flexible circuit materials?
Nishimoto: We don’t see any challenges as long as we can create a fixture to keep it rigid.
Las Marias: Do customers call out a specific brand name of material to use when dealing with flexible printed circuits?
Nishimoto: There is no specific brand name of material called out. In some cases, the substrate is exotic, but most are polyimide materials. Some customers specify the supplier on the approved vendor list, but in many cases, they depend on us to identify suppliers and give them choices to qualify that meet their requirements in terms of material performance and lead-time.
Las Marias: Which practice has the greatest impact on the quality of flexible circuit assemblies?
Nishimoto: Following industry-standard best practices in initial design and layout. Since flex circuits are folded up and put in tight enclosures, it is important to reduce points of failure, such as the location of points of interconnect. For example, a really long connector may require a rigid flex design, which uses stiffener rather than a 100% flex design.
Las Marias: In which end markets are you seeing increasing use of flexible circuits?
Nishimoto: Primarily, we are seeing them in medical and consumer applications.
Las Marias: What are the key things for OEMs to consider when choosing an assembly partner for flexible circuit assemblies/projects?
Nishimoto: First is prior experience with flex circuit assembly. Then, they should have a good relationship with one or more board carrier fabricators. Lastly, they should have an expertise in thermal profiling in reflow and strong discipline in work-in-process handling practices.
Las Marias: Are there new technologies out there that will significantly impact or benefit the flexible circuit assembly process?
Nishimoto: When you have rigid-flex combinations or stiffeners in use, you have two different heights—which makes it impossible to screen print without specialized fixturing. Paste jet printers like the MY500 we use are more adjustable and do not have that constraint because it allows us to tailor the amount of solder on individual components without the use of a stencil.
Las Marias: Thank you, Adrian.
Nishimoto: Thank you.
This article was originally published in the March 2017 issue of SMT Magazine.
Suggested Items
Indium’s Karthik Vijay to Present on Dual Alloy Solder Paste Systems at SMTA’s Electronics in Harsh Environments Conference
05/06/2025 | Indium CorporationIndium Corporation Technical Manager, Europe, Africa, and the Middle East Karthik Vijay will deliver a technical presentation on dual alloy solder paste systems at SMTA’s Electronics in Harsh Environments Conference, May 20-22 in Amsterdam, Netherlands.
SolderKing Achieves the Prestigious King’s Award for Enterprise in International Trade
05/06/2025 | SolderKingSolderKing Assembly Materials Ltd, a leading British manufacturer of high-performance soldering materials and consumables, has been honoured with a King’s Award for Enterprise, one of the UK’s most respected business honours.
Knocking Down the Bone Pile: Gold Mitigation for Class 2 Electronics
05/07/2025 | Nash Bell -- Column: Knocking Down the Bone PileIn electronic assemblies, the integrity of connections between components is paramount for ensuring reliability and performance. Gold embrittlement and dissolution are two critical phenomena that can compromise this integrity. Gold embrittlement occurs when gold diffuses into solder joints or alloys, resulting in mechanical brittleness and an increased susceptibility to cracking. Conversely, gold dissolution involves the melting away of gold into solder or metal matrices, potentially altering the electrical and mechanical properties of the joint.
'Chill Out' with TopLine’s President Martin Hart to Discuss Cold Electronics at SPWG 2025
05/02/2025 | TopLineBraided Solder Columns can withstand the rigors of deep space cold and cryogenic environments, and represent a robust new solution to challenges facing next generation large packages in electronics assembly.
BEST Inc. Reports Record Demand for EZReball BGA Reballing Process
05/01/2025 | BEST Inc.BEST Inc., a leader in electronic component services, is pleased to announce they are experiencing record demand for their EZReball™ BGA reballing process which greatly simplifies the reballing of ball grid array (BGA) and chip scale package (CSP) devices.