-
- News
- Books
Featured Books
- smt007 Magazine
Latest Issues
Current IssueIntelligent Test and Inspection
Are you ready to explore the cutting-edge advancements shaping the electronics manufacturing industry? The May 2025 issue of SMT007 Magazine is packed with insights, innovations, and expert perspectives that you won’t want to miss.
Do You Have X-ray Vision?
Has X-ray’s time finally come in electronics manufacturing? Join us in this issue of SMT007 Magazine, where we answer this question and others to bring more efficiency to your bottom line.
IPC APEX EXPO 2025: A Preview
It’s that time again. If you’re going to Anaheim for IPC APEX EXPO 2025, we’ll see you there. In the meantime, consider this issue of SMT007 Magazine to be your golden ticket to planning the show.
- Articles
- Columns
Search Console
- Links
- Media kit
||| MENU - smt007 Magazine
The Complex World of Soldering
May 1, 2017 | Stephen Las Marias, I-Connect007Estimated reading time: 11 minutes
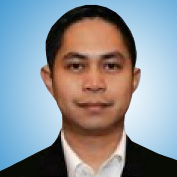
Industry veteran Happy Holden and Saline Lectronics Senior Process Engineer Cathy Cox discuss the various challenges and issues that users face in soldering, including the lack of a "one-size-fits-all" approach in the process, and some key factors that the PCB assembly industry should consider when it comes to different applications and markets.
Stephen Las Marias: What do you think are the greatest challenges when it comes to soldering in PCB assembly?
Cathy Cox: I would have to say our challenges are temperature. Temperature is a big problem with the flex boards. With the circuit board being so thin, actually getting the right temperature to be able to run them through a reflow is definitely a challenge.
Happy Holden: Picking a final finish that’s compatible with the solder that you picked in the flux. There’s no one answer that fits all. So picking that, and then you might say defending it—when people are selling different combinations—is a pretty big challenge, especially when not all the criteria for evaluation and testing is readily available. I've come to learn that the wetting balance really isn’t reliable to use that much anymore.
Our end-use applications are so diverse that when you talk about any particular subject, it’s tough for people to apply. ‘Does this apply to me or is he talking about the other guy over there?’ For instance, flex assembly and soldering is a particular challenge; but when I think of soldering, I think of rigid boards and I think of standard size thinner ones. When you get to really thick—over 2 mm—type boards, getting lead-free solder up to a milling temperature is a real challenge. There, you have to worry about the materials you built the boards for. It’s a huge industry, and how you carve it up is part of the challenge.
My life for years has been in automotive electronics. The company I work for is one of the highest volume assembler of automotive electronics in the Western hemisphere. Soldering is not really a problem except for new devices, QFNs and things like that that are coming on the market. It’s a process that’s running extremely smooth.
Las Marias: Do you think lead-free soldering continues to be an issue when it comes to reliability?
Holden: The industry has already moved to lead-free soldering. That was done a long time ago. It’s only the military and avionics and a few hold outs that haven’t moved to lead free. I talked to people at the APEX show that were in the military, and they realize that their time is running short because they have fewer and fewer people who support them. If you're going to lead free then, unlike tin lead where there wasn’t much variety, now you’ve got a whole proliferation of solders and different compatibility with final finishes, and different suitability for reliability life. That’s one reason why it’s so difficult because depending on what you’re assembling for, the answers maybe different.
Cox: I totally agree with Happy. At Saline Lectronics, the majority of our customers are doing lead free. Lead free is definitely more of a challenge with flex boards just due to the temperature. Getting good solder joints is definitely a challenge, but it’s a challenge that most companies are up for, so it's good. We need new things in our industry.
Las Marias: Do miniaturization, increased board densities, and shrinking component sizes impact the soldering process from your perspective?
Cox: I don't know if they necessarily affect it from what I can see. We deal with a lot of the 0201s. We're pretty excited to get our hands on 01005s and start playing with them and see if our pick-and-place machines can handle them. We'll need more precise placements to be able to make sure you get a good solder joint. It will be a little bit more challenging for an operator to manually inspect a board with solder joints being so small. But we have our high-tech AOI equipment, so that should not be a problem for us.
Patty Goldman: So, you don’t see very many of those types of components?
Cox: We see very small components all the time, but the smaller they get will be a challenge. I don't think it’s a challenge that’s going to stop us from doing anything. It’s just a different way of looking at it; it’s a different way of manufacturing it. You have to have more precise placement, make sure the thickness on your solder paste machines are proper, and I think it’s going to be awesome.
Goldman: What's your biggest bugaboo, then?
Cox: Our biggest with flex boards would actually be our pallets that we use in surface mount to keep our boards flat during the reflow. We can set pallets up for all different types of boards, but getting one to fit completely flat in there every time, and make sure the components are going to sit flat when they go through reflow, is a challenge. Most of the time, it's the bigger components that we see issues with because there’s a bigger area to have a bubble in the flex board.
Las Marias: Is solder jetting catching up with the paste printing process?
Holden: My last six years have been in high-volume production, and solder paste printing and the integral AOI machines are going to be tough to match in terms of jetting. Jetting may be much more applicable to high-mix, low-volume, but for the high-volume automobile market, mobile phones, consumer products, paste printing is pretty well defined and highly robust. Jetting maybe coming along, but it will have a hard time matching the fancy step stencils and some of the other techniques developed in stencil printing. But it may be totally adequate for high mix. I’ve never seen or we’ve never used any jetting equipment except for inkjet printing or solder mask printing in the PCB area. I don’t have a lot of experience with it, but any kind of jetting like that, be it inkjet, solder mask, or solder, really has not met the needs of volume manufactures to be cost effective, not yet. It’s for the prototype or high mix.
Las Marias: Does solder paste selection or qualification still matter today despite the standard solder types used in certain applications?
Holden: Yes, because they’re constantly improving solder paste and things like that. You're kind of always evaluating tweaks and minor improvements to see what it does, especially when one of our focuses in the past has been voiding and the micro-voiding you had with lead free. We haven't rejected products but we'd liked to eliminate it. Those are constantly minor tweaks in the formulation of the solder paste and the refill profile.
Las Marias: I understand solder voiding is still a big issue in the industry. Cathy, how do you tackle voiding?
Cox: We go with Indium solder paste. We have a really good connection with them. They help us through a lot of our issues with incisions, voids, stuff like that. We have been trying a few things here in our shop with changing the amount of paste that we put on a stencil, removing the mask around the pads so that the air can actually escape between the component and the solder pad. We've seen some success with that. The IPC standard keeps getting more and more vague on voiding under QFNs or even in through-hole components. We took it upon ourselves to kind of set our own standards, making sure that we have anything under 25% under a component or within a barrel fill. With our window pane and with reducing the solder mask around the pads, we’ve been successful in minimizing voiding to about 25% with our QFNs, BGAs.
Page 1 of 2
Suggested Items
Living His Dream: IPC EAO Course Leads Thejas K to Role as Quality Engineer
05/30/2025 | Michelle Te, IPC CommunityIt’s not often that a child wants to follow in the footsteps of their parents’ career. But Thejas K, a 22-year-old from Mysuru, India, whose mother Padmavathi was an EMS operator for nearly 20 years, is now an associate engineer in the quality department at Cyient DLM where PCB assemblies are manufactured for aerospace and defense.
Standards: The Roadmap for Your Ideal Data Package
05/29/2025 | Andy Shaughnessy, Design007 MagazineIn this interview, IPC design instructor Kris Moyer explains how standards can help you ensure that your data package has all the information your fabricator and assembler need to build your board the way you designed it, allowing them to use their expertise. As Kris says, even with IPC standards, there’s still an art to conveying the right information in your documentation.
IPC Applauds Leadership of Reps. Moore and Krishnamoorthi on PCB Manufacturing Bill
05/28/2025 | IPCIPC, the global electronics association serving more than 1,400 U.S. companies and over 3,200 worldwide, strongly supports the bipartisan reintroduction on May 28 of the Protecting Circuit Boards and Substrates (PCBS) Act in the 119th Congress.
AT&S Strengthens European Research at IPCEI Day
05/26/2025 | AT&SWith the IPCEI program, the European Union supports companies that make important contributions to the technological development of key industries on the old continent.
LSI ADL Technology Leverages IPC Membership for Growth, Training, and Industry Leadership
05/28/2025 | Michelle Te, IPC CommunityWhether attending the EMS Leadership Summit at IPC APEX EXPO, or subscribing to workforce training, LSI ADL Technology has noted several positive changes directly related to its IPC membership. “Collaboration, brainstorming, and sharing best practices have been the most important aspects of our partnership with IPC,” says Jonathan Verity, assistant general manager at LSI ADL Technology.