-
- News
- Books
Featured Books
- smt007 Magazine
Latest Issues
Current IssueIntelligent Test and Inspection
Are you ready to explore the cutting-edge advancements shaping the electronics manufacturing industry? The May 2025 issue of SMT007 Magazine is packed with insights, innovations, and expert perspectives that you won’t want to miss.
Do You Have X-ray Vision?
Has X-ray’s time finally come in electronics manufacturing? Join us in this issue of SMT007 Magazine, where we answer this question and others to bring more efficiency to your bottom line.
IPC APEX EXPO 2025: A Preview
It’s that time again. If you’re going to Anaheim for IPC APEX EXPO 2025, we’ll see you there. In the meantime, consider this issue of SMT007 Magazine to be your golden ticket to planning the show.
- Articles
- Columns
Search Console
- Links
- Media kit
||| MENU - smt007 Magazine
Use of Lean Manufacturing Principles Enhances Quality and Productivity
August 22, 2018 | Mike Baldwin, Spectrum Assembly Inc.Estimated reading time: 2 minutes
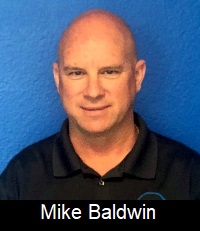
Regional EMS providers typically provide greater flexibility and responsiveness to their box build customers via use of work-cell-based batch assembly processes. Production volumes are fairly low, so the creation of dedicated continuous flow paced assembly lines is rare. However, we often see larger footprints and more complex projects with higher volumes.
Our cable, harness and PCBA manufacturing capabilities attract companies with products requiring complex subassemblies. As a result, it utilizes both work-cell-based and continuous-flow-line assembly in its box build assembly area.
One recent project example illustrates why this flexibility is important. The customer develops sports therapy devices used by trainers and professional sports teams. They had a next-generation product that increased functionality and, as a result, became mechanically much more complex. They needed a contract manufacturer capable of assisting them with development of mechanical manufacturing process instructions in addition to manufacturing the product. SAI helped develop the manufacturing process instructions as part of its new product introduction (NPI) services. The customer’s documentation for wire and cable assemblies, electronic assemblies, mechanical assemblies and cosmetics requirements is transmitted to the Aegis system and used to create visual work instructions that are utilized by the production team.
This project included cables, harnesses, PCBAs, electro-mechanical, fluidic, air and water subassemblies as well as chassis, sheet metal, plastics and hardware components. Routing the tubing in a limited chassis space was a challenge. Our team used the same process templates used in developing efficient wire and harness routing to route the fluidic, air and water lines. Trial builds were performed to ensure correct air pressure and water flow, and once nailed down, a tubing cut list was developed to make sure that all tubing was cut to appropriate lengths for the preferred routing. The customer validated the process. While computer modeling of this type of routing seems efficient, a routing that looks great on the computer screen can turn out to be an inefficient order of operations on the production line based on the obstacles that operators encounter during the assembly process. Having a combination of computer modelling and hands-on trial builds meant nothing was missed and that the order of operations was fully optimized.
Initially, the project was planned as a batch build process in several dedicated work cells, however, the volumes quickly outgrew that model. Our team utilized Lean manufacturing principles to redesign production flow from a cellular manufacturing process to a single conveyorized production line that integrated subassemblies with final assembly. Lean manufacturing principles were a core part of this redesign effort.
In the original process, cables, harnesses, PCBAs and subassemblies were assembled separately and pulled from stock. Final units were assembled sequentially by a pair of production operators.
The redesigned line has seven "feeder" work cells where production operators build electronic subassemblies consisting of multiple PCBAs, an onboard computer and associated harnesses; the fluidics; heating elements, cooling elements and additional subassemblies. In total, there are over 800 line items, seven custom PCBAs and 37 custom cables. At each station, operators add their subassembly to the base unit as it moves down the conveyor line. Programming, serialization, functional test, burn-in and crating are located at the end of the line. As part of this process, a 17-page device history record (DHR) is created and electronically filed for future use.
To read the full version of the article, which appeared in the July 2018 issue of SMT007 Magazine, click here.
Suggested Items
SAIC Awarded New $55 Million Mission Integration Contract From Space Development Agency
05/05/2025 | SAICScience Applications International Corp. has been awarded the Proliferated Warfighter Space Architecture (PWSA) Tranche 3 Program Integration (T3PI) contract from the Space Development Agency (SDA).
Discovery Opens Doors for Cheaper and Quicker Battery Manufacturing
04/23/2025 | PNNLThe discovery centers on sublimation, a commonly known process whereby under the right conditions, a solid turns directly into a vapor. Sublimation is what creates the tail of a comet as it flies by the sun. As the comet’s icy shell heats up, the ice instantly becomes vapor, instead of first melting into liquid water.
NCAB Acquires 100% of B&B Leiterplattenservice GmbH in Germany
04/23/2025 | NCABNCAB has signed an agreement to acquire 100 percent of B&B Leiterplattenservice GmbH (B&B) headquartered in Mittweida, west of Dresden. The company had net sales of around 150 MSEK in 2024 within the PCB trading with an EBITA exceeding SEK 20 million.
Spirit Electronics Expands U.S. Semiconductor Capacity with Acquisition of SMART Microsystems
04/17/2025 | BUSINESS WIREAs part of its strategic commitment to strengthening domestic semiconductor manufacturing, Spirit Electronics has acquired SMART Microsystems, located at Lorain County Community College (LCCC) in Ohio.
Vertex Growth Announces Commitment of €10M Investment in Dolphin Semiconductor to Accelerate Growth Strategy
04/16/2025 | BUSINESS WIREVertex Growth, a Singapore-based growth-stage venture capital fund, today announced a commitment of €10M in Dolphin Semiconductor, a leading provider of semiconductor IP solutions specializing in mixed-signal IP design. This investment will further support and accelerate the execution of Dolphin Semiconductor's growth strategy.