-
- News
- Books
Featured Books
- pcb007 Magazine
Latest Issues
Current IssueThe Hole Truth: Via Integrity in an HDI World
From the drilled hole to registration across multiple sequential lamination cycles, to the quality of your copper plating, via reliability in an HDI world is becoming an ever-greater challenge. This month we look at “The Hole Truth,” from creating the “perfect” via to how you can assure via quality and reliability, the first time, every time.
In Pursuit of Perfection: Defect Reduction
For bare PCB board fabrication, defect reduction is a critical aspect of a company's bottom line profitability. In this issue, we examine how imaging, etching, and plating processes can provide information and insight into reducing defects and increasing yields.
Voices of the Industry
We take the pulse of the PCB industry by sharing insights from leading fabricators and suppliers in this month's issue. We've gathered their thoughts on the new U.S. administration, spending, the war in Ukraine, and their most pressing needs. It’s an eye-opening and enlightening look behind the curtain.
- Articles
- Columns
- Links
- Media kit
||| MENU - pcb007 Magazine
Microvias: Links of Faith are Not Created Equally
July 18, 2019 | Jerry Magera and J.R. Strickland, Motorola Solutions Inc.Estimated reading time: 5 minutes
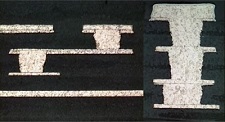
Abstract
Microvias connect adjacent copper layers to complete electrical paths. Copper-filled microvias can be stacked to form connections beyond adjacent copper layers. Staggered microvias stitch adjacent copper layers with paths that meander on the layers between the microvias. Both microvia configurations are formed by essentially the same sequential operations of laser drill, metallization, and patterning, using various chemical, mechanical, and thermal treatments to form each layer, one over the other. Stacked microvias must be filled while staggered microvias do not. Process specifics differ from manufacturer to manufacturer.
Stacked microvias fracture during reflow assembly while staggered microvias do not. Assembly reflow subjects the printed wiring board (PWB) to the greatest temperature excursion. Stacked microvias with a weak interface fracture during assembly reflow and are a hidden reliability threat. This phenomenon was reported in IPC-WP-023 [1] in May of 2018. IPC-TM-650 Method 2.6.27A is a performance-based PWB acceptance test that detects fractured microvias. SEM pictures are presented to initiate discussions in the search for the root cause. Included are cross-section images of completed microvia structures, SEMs after laser drill, and after electroless copper. Not all stacked microvias fail. To learn why, microvia samples were collected from different PWB suppliers. Microvias drilled by UV lasers are compared to microvias drilled by other laser configurations. The images show that microvia structure was influenced by laser type. This article discusses the various laser-drilled microvias and presents SEM photographs to begin the search for the root cause of weak copper interface.
Introduction
The search for root cause in this article focuses on laser drill. Not all stacked microvias fail. To learn why, microvia samples drilled by UV lasers were visually compared to microvias drilled by other laser configurations. Samples were extracted after laser drill and after electroless copper. SEM analysis provided high-resolution views for comparison. The SEM pictures revealed that microvia structure was influenced by laser type.
Figure 1: Cross-section of layer 1 to layer 3 staggered copper filled microvia and layer 1 to layer 4 stacked copper filled microvia. Cross-sections were polished and microetched to reveal copper structure.
Figure 1 shows a two-level staggered microvia and a three-level stacked microvia. Both configurations are used in PWBs; however, when both were used on same PWB, the stacked microvia failed during reflow assembly while the staggered microvia did not. The microvias were formed with a UV-CO2 combo laser UV clean followed by desmear, electroless copper, and electrolytic copper fill.
Figure 2: Cross-section of a three-stack microvia failure.
Both stacked and staggered microvias must survive reflow assembly. A cross-section of a failed three-stack microvia shown in Figure 2 revealed a separation between the target pad and plated copper fill at both layers 2 and 4. The microvias were drilled with a UV laser followed by desmear, electroless copper, a copper strike, then copper fill. The UV laser ablation parameter was set to dig into the copper target pad. The UV-drilled microvia failed during reflow assembly.
Figure 3 is SEM photograph of a UV laser-drilled, copper-filled microvia cross-section before assembly reflow. The copper-fill to target pad interface as shown is a complex structure that meanders into the layer 2 plated copper. Arrow (a) points to a UV laser-formed copper burr at the knee of the copper foil. Arrow (b) points to a thin demarcation that follows the copper fill to copper strike interface. Arrow (d) points to the electroless layer between the copper foil and electroplated copper. Arrows (c) and (e) point to interface features that are darker and coarser than the plated copper. The electroplated copper strike to electroless copper to target pad interfaces were obscured by the features created by the UV laser ablation.
Figure 3: UV-only laser-drilled copper-filled microvia: (a) UV-laser-induced burr formed on copper foil; (b) Demarcation between copper fill and copper strike; (c) Feature with different texture compared to the plated copper; (d) Electroless copper layer between copper foil and electroplated copper; (e) Feature with texture different compared to the plated copper.
UV laser-drilled stacked microvias failed reflow assembly more frequently compared to microvias drilled by other laser types. The difference was related to the UV laser created features present between the copper fill and target pad as shown in Figure 3. The features, only observed in UV laser-drilled microvias formed as copper melted and recast in the presence of air, coincide with the weak points that fracture when thermally stressed during reflow assembly. The rest of this article presents SEM photographs of microvias after laser drill and after electroless copper to show the condition of the copper surface of the target pad produced by the commonly practiced laser processes.
Results and Discussion
The PWB manufacturing base uses different laser types, plating chemistries, and laminate materials in the manufacture of PWBs with microvias. A reliable stacked microvia depends on the condition of the target pad after the laser process. Laser drilling is the accepted method of forming microvias. UV Nd:YAG and CO2 lasers were developed to drill microvias and are commercially available in four different configurations to the PWB industry.
1. UV Nd:YAG Laser
The UV laser can micro-machine a variety of materials, including copper and glass-reinforced dielectric laminate to produce unique features. The ability to ablate copper can potentially damage copper surfaces, such as the target pad of a microvia. SEM photographs of target pads touched by the UV beam show evidence of melted copper and copper particles that were explosively ejected from the melted copper surface. Copper flow patterns were visible on the target pad along with porosity and inclusions that were characteristic of the sputtering and recasting of molten copper. Molten copper flow patterns were visible over the surface of the target pad and the rim of the outer layer copper foil surrounding the microvia opening—basically any copper surface the UV beam contacted. Constructions require surface copper thickness thinner than target copper thickness to prevent the UV beam from piercing the target pad copper. In most constructions, UV copper ablation requires entry copper to be less than 0.5-oz. copper weight.
To read the full article, which appeared in the July 2019 issue of PCB007 Magazine, click here.
Suggested Items
I-Connect007 Editor’s Choice: Five Must-Reads for the Week
07/11/2025 | Andy Shaughnessy, Design007 MagazineThis week, we have quite a variety of news items and articles for you. News continues to stream out of Washington, D.C., with tariffs rearing their controversial head again. Because these tariffs are targeted at overseas copper manufacturers, this news has a direct effect on our industry.I-Connect007 Editor’s Choice: Five Must-Reads for the Week
Digital Twin Concept in Copper Electroplating Process Performance
07/11/2025 | Aga Franczak, Robrecht Belis, Elsyca N.V.PCB manufacturing involves transforming a design into a physical board while meeting specific requirements. Understanding these design specifications is crucial, as they directly impact the PCB's fabrication process, performance, and yield rate. One key design specification is copper thieving—the addition of “dummy” pads across the surface that are plated along with the features designed on the outer layers. The purpose of the process is to provide a uniform distribution of copper across the outer layers to make the plating current density and plating in the holes more uniform.
Trump Copper Tariffs Spark Concern
07/10/2025 | I-Connect007 Editorial TeamPresident Donald Trump stated on July 8 that he plans to impose a 50% tariff on copper imports, sparking concern in a global industry whose output is critical to electric vehicles, military hardware, semiconductors, and a wide range of consumer goods. According to Yahoo Finance, copper futures climbed over 2% following tariff confirmation.
Happy’s Tech Talk #40: Factors in PTH Reliability—Hole Voids
07/09/2025 | Happy Holden -- Column: Happy’s Tech TalkWhen we consider via reliability, the major contributing factors are typically processing deviations. These can be subtle and not always visible. One particularly insightful column was by Mike Carano, “Causes of Plating Voids, Pre-electroless Copper,” where he outlined some of the possible causes of hole defects for both plated through-hole (PTH) and blind vias.
Trouble in Your Tank: Can You Drill the Perfect Hole?
07/07/2025 | Michael Carano -- Column: Trouble in Your TankIn the movie “Friday Night Lights,” the head football coach (played by Billy Bob Thornton) addresses his high school football team on a hot day in August in West Texas. He asks his players one question: “Can you be perfect?” That is an interesting question, in football and the printed circuit board fabrication world, where being perfect is somewhat elusive. When it comes to mechanical drilling and via formation, can you drill the perfect hole time after time?