-
-
News
News Highlights
- Books
Featured Books
- smt007 Magazine
Latest Issues
Current IssueIntelligent Test and Inspection
Are you ready to explore the cutting-edge advancements shaping the electronics manufacturing industry? The May 2025 issue of SMT007 Magazine is packed with insights, innovations, and expert perspectives that you won’t want to miss.
Do You Have X-ray Vision?
Has X-ray’s time finally come in electronics manufacturing? Join us in this issue of SMT007 Magazine, where we answer this question and others to bring more efficiency to your bottom line.
IPC APEX EXPO 2025: A Preview
It’s that time again. If you’re going to Anaheim for IPC APEX EXPO 2025, we’ll see you there. In the meantime, consider this issue of SMT007 Magazine to be your golden ticket to planning the show.
- Articles
- Columns
Search Console
- Links
- Media kit
||| MENU - smt007 Magazine
Is Captive Making a Comeback?
December 20, 2019 | Andy Shaughnessy, Design007 MagazineEstimated reading time: 15 minutes
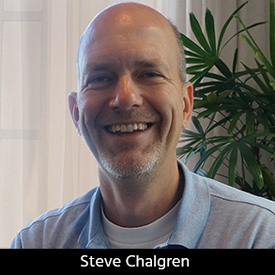
Andy Shaughnessy recently spoke with Altium’s Steve Chalgren, senior VP of business strategy and planning. Steve shared his thoughts about why improved manufacturing and automated EMS equipment, such as robotics, might lead smaller OEMs to become captive shops like the old days. Is captive making a comeback?
Andy Shaughnessy: Steve, it’s nice to meet you. Can you tell us a little bit about your background and current responsibilities?
Steve Chalgren: My current responsibilities at Altium are working closely with our CEO, COO, and other executives on various strategy options that we want to look at as we move forward and deliver end-to-end opportunities for our customers to be able to design their products all the way through to manufacturing prototypes. I have about nine years of experience in outsource manufacturing. I’ve worked at OEMs—mostly startup companies—managing the outsourcing effort to make the PCB assemblies and everything else you need to make products. Then, I spent almost 20 years in PLM, working at various companies like Agile, Oracle, and Arena Solutions.
Shaughnessy: You have some interesting thoughts on how the supply chain might change in the not-too-distant future. Tell us about that.
Chalgren: I see a lot of opportunity for disruption in high-tech manufacturing for PCBs to assembly (PCBAs). For many years, the common practice was to design a board and then send it out to be made at the PCB fabricator and have the assembly house build it for you. Or, you would buy the parts from Digi-Key or another distributor, kit it yourself, and send it out to have it made. Now that those manufacturers are not local as often, sometimes, you’re sending it hundreds of miles away or even further—not usually for prototypes, but definitely for production; that adds a lot of time to the entire process.
When you think about the digitization, and the automation that’s coming out—especially with robotics and with data flows in the cloud—one could imagine an engineer doing design work would be able to push a button and have that design go straight to the manufacturer and get it made. That’s great, but that manufacturer has to get the parts, and it’s still far away. So, what if there are opportunities in manufacturing with small robotic capabilities?
Think about printing. You can print plastics, you can print metalized, and now you’ll be able to print metalized and plastics together, similar to Voltera. Robotic assembly companies are also coming out, like Bright Machines, that are doing full-on in a box manufacturing box assembly where you can put the PCBAs in, and the robots will do the fine hand assemble into enclosure work for small-scale manufacturing.
If you are an OEM—maybe not a startup, but a little bit larger—you can start looking at verticalization options that you have given up 20–30 years ago so you could start manufacturing prototypes in-house again. Think of the quick turnaround you can have where you have your parts there and someone who loads this machine, which is not completely different from loading a copy machine. It’s maybe three times more complex than that, but not significantly different because the data flows automatically to the machines. There’s no programming on the machine; that has happened through the transfer of data from the design tool into the machine. When a person loads up the PCBs and parts, you can quickly make very fine pitch and robotically delivered pick-and-place PCBAs and assemble them into an enclosure.
Shaughnessy: It could be heralding the return of captives. OEMs could build all their own board like they used to.
Chalgren: When you outsource your manufacturing, you’re outsourcing a lot of know-how out of your company and adding a significant delay. That’s great if the cost is way cheaper—and that’s why people have done it—but if the cost isn’t way cheaper, all the math changes. And that’s one of the opportunities that we see in the next five years is the ability for low-cost PCB/PCBA printing or even the robotic assembly of products. That will have a dramatic impact on innovation because you could crank out a board two or three times a day. And you don’t have to design a board revision, send it out, and wait 48 hours or longer. You could push print, go downstairs, grab the PCB, have one person load the machine with parts that you automatically ordered/delivered as you designed them in an hour later, or so that you have it ready. Then, you can repeat it as needed.
Shaughnessy: As robotics and all this equipment gets better and better, it’s getting more foolproof and able to be used by OEMs.
Chalgren: And by people who aren’t as trained. When you think about technology, the technology stacks begin from the bottom (low-level stuff). Today, people aren’t writing machine language anymore; it is becoming easier and easier to program software. Two years ago, doing AI or machine learning was a job for Ph.Ds.; now, it’s frequently a job for people with bachelor’s degrees because of new open-source libraries like Tensorflow. Things get simplified, and manufacturing hasn’t had that shift yet, but it is ripe for it—especially with the advent of robotics and the ability for the robotics to be intelligent on how they do the assembly.
Shaughnessy: That ties in with 3D printing and the robotic assembly machines. You could do anything in-house except traditional fabrication; that would be the only thing that you would have to send out.
Chalgren: If you have metallized plastic printers that can do that too, you could print the board from plastic and metal. Voltera is on the market printing PCBs one by one, mostly for prototyping, but they just announced their boards are being tested in outer space by NASA. The lines are blurring from prototype to specialized singular, or small lot runs all in-house; it’s classic disruption from the bottom. Plastic printers exist already. Now, metallization is out, and you can imagine starting combining that in some sort of technology, you could print your own PCB, print it, and put it into your robot machines a closed unit like a super complex copy machine, but it’s in a PCB assembly machine. You put it in there and have a set of parts that you line up with cartridges in the back, and then it drops in and makes one or 10.
Shaughnessy: You’d be bringing the supply chain in-house.
Chalgren: Yes, especially if you consider the “send-out” cost of slower time-to-market impacts to an OEM’s revenue horizons. It could be less expensive to manufacture the prototype in-house. Of course, these machines will be higher priced at first to capture the disrupter value, but competition will drive the costs down. Right now, PCBA line manufacturers are focused on the volume contract manufacturers. The technology curve is going to make them wake up and build new, cheaper, and smaller machines for in-house manufacturing. Someone is going to see the opportunity and think, “I could sell it to a small set of contract manufacturers that grind me on price because they can, or I could sell it to thousands of OEMs. What am I going to design for?”
Shaughnessy: On your end, you’re thinking the typical designer is going to need a lot of this functionality built into the software in the future.
Chalgren: It’s super critical. The one thing you have to address is data goes through a lot of manual integrations today where you’re outputting it out of the design tool. People are looking at those files, but you might not have designed it correctly for the machine you’re going to use. Then, you have to go back and forth on design for manufacturing tests.
We have to solve that so that the data can flow seamlessly. And based on the machine that’s going to make the product, it automatically knows how to translate the data or give the feedback to the designer, as they’re designing; for example, if you’re going to build it on this machine or at this facility, you need to meet these design specifications. We’ll have that in the cloud available for that person to say, “If you’re going to manufacture that, here are our design rules.” You pull it down, do a DFM at your desk, and don’t have to send it out and get a report back in an email attachment.
Shaughnessy: All smart factories seem to be going on in Asia. But if you’re right about this, we’re basically going to have smart factories at the OEM level.
Chalgren: We’re talking about potential futures here, but yes, I think you’re right.
Shaughnessy: With fewer people touching it.
Chalgren: That’s the disruption; today, labor cost is a big deal. And that’s when you send it overseas, where they have lower labor costs and have low facility costs; that drives that deal. But once those disappear as a benefit or a thing you’re shooting for, then everything could change. And that’s where I think the disruption will drive manufacturing back to the OEMs worldwide. Maybe at super-high volumes, you’ll still use those contract manufacturers that have the current high-volume, low-mix lines.
Shaughnessy: To make iPhones, for example.
Chalgren: Sure. It will be the same kind of value/performance decision you see between a solid-state memory and hard drives. Hard drives never disappeared, but they almost have. You still have hard drives for big things because they are surviving by always being bigger and cheaper on a memory unit basis, but the solid-state memory keeps getting bigger and cheaper too, and what’s the preference? I’m going to get solid-state; it doesn’t break. I want performance over the value. That could happen with manufacturing, too; it’s the same battle. Outsourced manufacturers are hard drives, and in-house would be solid-state.
Shaughnessy: This would change everything. The OEM customers would say, “We don’t need you anymore.”
Chalgren: They will start small. And everyone will see it coming, but maybe not everyone will react. For instance, it took years and years before solid-state finally got big enough for hard drive companies to invest in them. I would imagine that the manufacturing companies would move to a high scale and use new automation and robotics to get theirs even more efficient. They will be fighting all the way down the cost line to keep the business because of robotics. They may deploy some new strategies, such as building manufacturing facilities, closer to the point of use so that the manufacturing facilities won’t be all in low-cost locations of labor. They will be in the locations because they’re closest to the customer, and the automation marginalized the value of low-cost labor over logistics. Logistics might become the more expensive thing in the cost analysis. Further, they might become worldwide manufacturers with a lot of smaller facilities that are highly automated, trying to push back the OEM’s in-house manufacturing facility that they buy in a box.
Shaughnessy: This would put North America back in the game.
Chalgren: It would. It’s great for the environment and innovators. It takes all that lag out of the system.
Shaughnessy: You’d be flying fewer miles.
Chalgren: And have fewer parts traveling around the world. The other thing is that every developing country has people coming out of their schools, but they don’t have the infrastructure; now, they can leapfrog the whole thing. For example, cellphones in Asia leapfrogged the whole landline system that no one uses anymore in the U.S.; all of a sudden, a developing company has instant world-class communications, and in the future, they could have a world-class tech manufacturing center. They buy some of these units, drop it in there, and start doing their design work. They can buy a computer and instantly start innovating and building products. They don’t have to have this huge capital availability to try to invest in their designs or ship it using difficult logistic methods; you can escape most of that. In that regard, manufacturing would be anywhere it is needed.
Shaughnessy: And once the model got rolling, OEMs could even start doing commercial work.
Chalgren: You never know. That was the reason they pushed it out in the first place. They bought these expensive lines for $5–10 million back then, and then they didn’t run them full blast. When you looked at it from a financial perspective, it was a huge waste of assets, and even if it was slightly more per unit to outsource, it was still less than buying and having an idle manufacturing line. That’s what drove the whole thing to outsource in the ‘80s like crazy. Now, it doesn’t matter if the machine’s idle because it’s not very much money, so the math changes. Maybe OEMs would start manufacturing. They won’t care for the equipment being idle because it’s not going to be this huge investment in capital. And the flexibility to meet demand could have significant revenue opportunity, especially at the end of a quarter.
Shaughnessy: And we’d have a lot more R&D taking place at the OEM level like it used to be when they were captives. There would be more R&D and more of a knowledge base in the U.S.
Chalgren: And having the designer close to the manufacturing process would be huge; there’s a natural learning process that they gain. If you’re walking over to your mini factory in the OEM, and you screw up the margins, or something didn’t work right, you see it right away and can fix it. For example, when you create your own stuff on a printer, the printer works, and there are idiosyncrasies from your printer at home vs. at work. That’s the benefit versus sending the file off; it comes back 48 hours later, and your margins are off. Now, the designer could viscerally understand the manufacturability that they need to do as they’re designing as well as having the design rules help them out. They will simply do better designs faster.
Shaughnessy: And it would get rid of the whole lack of communication between the designer and the fabricator because it’s you and the person down the hall.
Chalgren: Exactly. The team or the support engineer would make sure the parts are there, loaded on the machine, and available. There’s one company, Bright Machines, that’s tackling it at the factory level. They’re a startup from the former co-CEO of Autodesk, Amar Hanspal. There are some big names in that company, and they have around $180 million in funding. They’re building their own robots and machines and going after the manufacturing space.
The natural next step would be going from hundreds or thousands of customers to tens of thousands of OEM customers because those are the manufacturers, and they’re all consolidators. That has to be what they’re going after. I look at that from a positive perspective of innovation, and it’s going to be crazy. Think of the disruption Amazon caused by brick and mortar stores; Circuit City didn’t make it, but Best Buy did. It’s not going to be total doom and gloom for them, but they’re going to have to change their game plan.
Shaughnessy: And it’s going to change the way EDA tools are made.
Chalgren: Yes. When the model looks like that, the EDA tools are going to have to think end to end—not just at the design phase. How will it roll through and integrate? How does it deliver data to these different machines in a seamless way and in the correct way? And how do you get the proper feedback to the designer to help them do it right in the beginning?
Another thing to think about is the distributor’s model has changed too; even back in the ‘80s, they sold to OEMs, and the ones that didn’t have in-house manufacturing still bought the parts kitted and sent them out to their contract manufacturer. Then, the contract manufacturer looks for more margin, saying, “We can do the parts management for you and logistics, and we can make a little margin on it.” They have ascended as a major buyer directly from manufacturers or through major distributors.
If OEMs are buying parts for all their prototypes because they build in-house, maybe distributors will start changing their game a little bit too. Obviously, Digi-Key is a clear winner in that today, but maybe some of these other companies will start seeing the advantage of getting into the OEMs in a more direct way like they used to do. That might spawn a lot of salespeople or a much different e-commerce experience—something for the OEMs so that the parts are automatically ordered/delivered when they are designed in so they are there when they want to make those prototypes, and they’re easily returned (think Amazon) when they aren’t needed.
Shaughnessy: And they probably have to change the whole thing. Many components companies are saying you have to buy batches of thousands or millions because a lot of these OEMs aren’t going to need that many.
Chalgren: No. You can think these machines would probably change the whole concept of how you load a machine with reels and tape, etc., but there will probably be a lot more standardization on that. And as they see this opportunity, everyone’s going to try to get in the game. You might see distributors doing direct to stock programs where they come in and stock their shelves in your OEM house to make sure the parts are there so you can plug them in. The biggest problem is going to be having the parts.
Shaughnessy: Thank you for your time. This has been very interesting.
Chalgren: Thank you.
Suggested Items
From Execution to Intelligence: A Data-driven Approach to Modern Manufacturing
05/06/2025 | Barry Matties, I-Connect007In this discussion, Augusto Vilarinho, an MES expert at Critical Manufacturing, explores the essential functions of MES in tracking and tracing shop floor activities where AI and machine learning capabilities are purposely built into the MES through it's embedded data platform, capturing all machine data, integrating and connecting with different systems, ERPs, physical equipment, and people.
Join the Conversation: MESI 4.0 Summit 2025 Brings Manufacturing Experts to Porto
05/06/2025 | Critical ManufacturingThe MES and Industry 4.0 International Summit 2025 (MESI 4.0 Summit), hosted by Critical Manufacturing, will bring together manufacturing leaders, technology experts, and industry pioneers in Porto on June 12-13, offering a unique platform to explore practical strategies for digital transformation and smart manufacturing.
AMI achieves 52 consecutive weeks of First Pass Yield Rates above 98.72%
05/06/2025 | Alternative Manufacturing, Inc.AMI, a leading provider of high-quality PCB assembly (PCBA) solutions, proudly announces the achievement of 52 consecutive weeks of first pass yields at test, maintaining an exceptional success rate of 98.72% or better. This remarkable accomplishment underscores the company's unwavering commitment to manufacturing excellence, quality assurance, and customer satisfaction.
The Government Circuit: Trump’s Trade War Disrupts the Electronics Ecosystem
05/06/2025 | Chris Mitchell -- Column: The Government CircuitThere is certainly no shortage of work to be done in the IPC Government Relations department, as the U.S. waged a tariff campaign on practically every industrial country in the world and several countries embarked on high-tech initiatives with a mix of approaches to the crucial foundations of electronics manufacturing. Indeed, the breadth and speed of U.S. President Donald Trump’s tariff campaign continues to be a serious challenge for our industry.
Dixon, Inventec Form JV for PC Manufacturing in India
05/05/2025 | DixonDixon has entered into Joint Venture Agreement (JV Agreement) with Inventec. Pursuant to the said JV Agreement, Dixon IT Devices Private Limited (JV Company) will be 60% owned by Dixon and 40% owned by Inventec.