-
- News
- Books
Featured Books
- smt007 Magazine
Latest Issues
Current IssueSupply Chain Strategies
A successful brand is built on strong customer relationships—anchored by a well-orchestrated supply chain at its core. This month, we look at how managing your supply chain directly influences customer perception.
What's Your Sweet Spot?
Are you in a niche that’s growing or shrinking? Is it time to reassess and refocus? We spotlight companies thriving by redefining or reinforcing their niche. What are their insights?
Moving Forward With Confidence
In this issue, we focus on sales and quoting, workforce training, new IPC leadership in the U.S. and Canada, the effects of tariffs, CFX standards, and much more—all designed to provide perspective as you move through the cloud bank of today's shifting economic market.
- Articles
- Columns
- Links
- Media kit
||| MENU - smt007 Magazine
Estimated reading time: 11 minutes
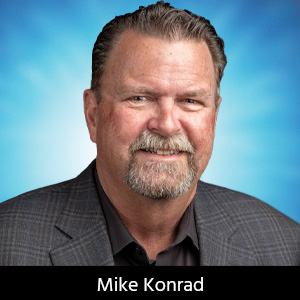
The Knowledge Base: Unlocking the Invisible—The Critical Role of X-ray Technology
From detecting voids under BGAs to solder defects in high-reliability applications, X-ray inspection has become an indispensable tool in modern manufacturing. But how is the technology evolving? What challenges do experts face in deploying X-ray inspection effectively and what does the future hold for this critical quality assurance method?
To answer these questions, I spoke with two experts in the X-ray industry, each bringing a unique perspective to the conversation. Jesper Lykke is the president and CEO of Viscom, a manufacturer of X-ray equipment, specializing in developing cutting-edge inspection technology. Jesper provides insight into how hardware and software innovations are shaping the next generation of X-ray systems and what manufacturers can expect in terms of capabilities and usability.
On the other side is Robert Boguski, CEO of Datest, a user of X-ray technology, operating a contract testing company that relies on this equipment daily to ensure product reliability. Their perspective highlights the practical challenges and benefits of implementing X-ray inspection in real-world production environments, from detecting hidden soldering defects to meeting industry standards for quality assurance.
Together, these two viewpoints offer a comprehensive look at X-ray technology's current state and how it is evolving to meet the increasing demands of the electronics manufacturing industry.
Questions for an X-ray equipment manufacturer:
What are the most significant advancements in X-ray inspection technology in recent years, and how have they improved defect detection in circuit assemblies?
Jesper Lykke: X-ray technology hasn't changed significantly, but the software that processes the images has advanced considerably. With AI-driven defect detection, identifying flaws, even those traditionally hard to spot, has become much easier. AI can filter out noise, assess the area based on experience, and indicate whether a potential defect is present. This allows operators to focus primarily on the most challenging defects, while AI efficiently handles routine detections. It's a win-win: Operators are not overwhelmed by excessive defect calls, and the company can maintain high product quality with greater ease.
How do you guide electronics manufacturers in selecting the right X-ray system for their specific inspection needs, such as quality control, failure analysis, or process monitoring?
Lykke: Through conversations, we aim to understand exactly what the customer expects from the machine. This involves asking numerous practical questions, such as:
- Will the system be used inline or offline?
- What inspection speed is required?
- What type of defect/process control does the system need to handle?
- How many boards need to be inspected daily?
- What are the space constraints on the production floor?
- Is this for a new line setup or integration into an existing line?
- What are the customer's specific process requirements?
By gathering this information, we can effectively guide the customer toward the best solution for their needs. This is not a quick, five-minute conversation. Our goal is to provide comprehensive support, ensuring we fully understand the customer's needs and expectations.
Can you explain the key differences between 2D, 3D, and CT X-ray imaging, and in what scenarios each technology provides the greatest value?
Lykke: The key difference lies in the level of detail: 2D provides fewer details, while CT offers the most comprehensive view. This all depends on the number of images captured for each area of interest; the more images, the clearer the solder joints or defects will appear. However, this comes with a tradeoff: CT takes longer than 2D. Choosing the right method is about balancing speed and inspection goals. For manual or semi-automated X-ray inspection in a lab environment, maximizing detail is often the priority since time is less critical. Conversely, for inline X-ray inspection, speed is essential, making 2D or 3D more suitable.
What role does automation and AI-driven analysis play in modern X-ray inspection systems, and how does it impact efficiency and accuracy in defect detection?
Lykke: This role is significant. As mentioned earlier, AI greatly simplifies defect detection, requiring far less effort while improving accuracy. Refer to the explanation above for more details.
With miniaturization and ultra-high-density interconnects (UHDI) becoming more common, how is X-ray technology evolving to keep up with these challenges?
Lykke: There are several ways to approach this, or even a combination of methods. One option is using higher-resolution X-ray technology, now capable of sub-1 micron focus spots, which generally improves the detection of smaller objects and defects. Additionally, AI plays a crucial role here for the same reasons mentioned earlier, enhancing detection accuracy with minimal effort.
Product design also impacts inspection results. Ideally, designing the product without heavy metal objects directly opposite fine-pitch components can improve visibility. However, this is rarely feasible since boards are typically designed with specific requirements in mind. In challenging cases, achieving sufficient visibility may require higher tube power, which can risk washing out fine defects.
What are the most common misconceptions about X-ray inspection in electronics manufacturing, and how do you address them when working with customers?
Lykke: Misconception: X-ray can detect every defect perfectly.
Reality: While X-ray is highly effective, it’s not foolproof. Certain defects, especially those involving subtle material inconsistencies or minimal density differences, can be challenging to detect. AI-enhanced image processing significantly improves detection rates but is still dependent on image quality and inspection parameters.
Misconception: Higher tube power always means better results.
Reality: Increasing tube power may improve penetration but can also wash out fine details as mentioned above, particularly in delicate components or small solder joints. Proper calibration and balancing resolution with power are critical.
Misconception: More images always mean better inspection.
Reality: Capturing excessive images can improve detail but may drastically slow the process. The key is finding the right balance between resolution, speed, and data volume, especially for inline inspection.
Misconception: X-ray inspection is only for complex boards.
Reality: While essential for complex PCBs with hidden joints (e.g., BGA, QFN), X-ray can also improve quality control on simpler boards by detecting solder voids, bridges, or alignment issues.
Misconception: X-ray inspection is too slow for inline production.
Reality: Modern inline X-ray systems are designed for high-speed inspection, especially with AI algorithms that reduce processing time by quickly identifying areas of concern.
Misconception: All X-ray systems provide the same results.
Reality: Different X-ray technologies, 2D, 3D, and CT vary in detail, speed, and suitability for certain applications as described above. Choosing the right method is crucial for achieving optimal results.
Questions for a contract testing company:
As a contract inspection provider, what are the most common reasons customers turn to X-ray inspection services for their circuit assemblies?
Robert Boguski: The reasons would include precise defect detection at higher resolution and magnification (we have a more powerful X-ray system than the customer, and they are skeptical about results from their own system); that X-ray sees what other inspection methods don’t (obvious example: underneath BGAs); and failure analysis, meaning that I know a problem exists, because there is an electrical failure, but thus far I haven’t been able to verify/validate the root cause. Other reasons include a need for second opinion, lack of X-ray capability at their own facility, and customer feedback, usually in the form of rejections and/or field failures.
Sometimes, the equipment or process isn’t working. It’s 4 p.m. Friday at the end of the quarter, and money is riding on the problem being resolved. It feels like we’re all going to die.
What best practices do you follow to ensure consistency and accuracy when inspecting a wide variety of assemblies from different manufacturers?
Boguski: Never take the customer’s description of the problem at face value. Frequently we find problems on the board, but in a different location than the customer initially suspects.
I recommend that you look at the entire board. Don’t focus solely on the customer’s area of interest. Ask the customer at the beginning of the engagement whether our finding nothing wrong would be a good thing or a bad thing. Their answer tells a lot.
Give the customer realistic expectations of the probability of finding the suspected defect. The more realistic the front-end setting, the calmer the relationship. If you manage the time and expectations at the beginning, there are typically fewer surprises and recriminations at the end.
Can you share an example of a particularly challenging inspection case where X-ray technology provided critical insights that other inspection methods could not?
Boguski: We recently did several projects for a medical startup, in which we were asked to X-ray and CT scan human blood vessels for signs of calcified plaque buildup. The images were used in clinical trials of a medical product. We had to design a process to reliably handle human tissue, especially to hold it steady during the imaging process (vibration distorts images). It took several months of trial-and-error engineering to achieve a repeatable, reliable process, but in the end, we did it, and the customer was happy.
How do you work with customers to interpret X-ray findings and help them resolve potential manufacturing defects or quality/reliability concerns?
Boguski: With a customer new to our service, the best way is to review the images of the first job with them, explaining to the uninitiated in X-ray technology exactly what they are seeing, and why what they are seeing either is or isn’t a legitimate defect. This can be done either in person or on a virtual call. Knowledge is power, and we believe in transmitting knowledge. An informed customer tends to be a satisfied customer, in our experience. Satisfied customers tend to return and tell others about us.
Once the review is complete, we are often asked to recommend process improvements. We are not process engineers, so we must tread carefully when asked this question. Usually, we provide a range of possible causes. If the customer pushes harder and wants to know the specific root cause of a problem, we often refer them to an industry colleague who is a process management consultant.
From your experience, what are the key differences in value between 2D and 3D X-ray technology, and how do you determine which method is best suited for a particular inspection need?
Boguski: 2D is conventional X-ray inspection; 3D is CT scanning. The terms are constantly mixed up and lead to much confusion. Unscrupulous persons often take advantage of this by playing on peoples’ ignorance. Conventional X-ray is cheaper by the hour than CT scanning. Most of our inspection engagements begin with conventional X-ray, if for no better reason than as a sanity check (even if the customer wants us to go directly to CT scanning). We usually take this conservative approach because it saves the customer money and arrives at the objective in a quicker and more systematic way. Customers typically are not put out when we save them money.
What advancements in X-ray inspection technology have had the biggest impact on your ability to serve customers effectively, and where do you see the technology heading in the future?
Boguski: The obvious answer is AI. It is removing some of the drudgery from the old school method of having one person reviewing hundreds of images from one board, with the attendant risk that operator fatigue will set in and something crucial will be missed. Having said that, AI does not eliminate the need for skilled, experienced Xray technicians and analysts, with time-based knowledge to distinguish false from true failures, and to evaluate subtle defects and judge their potential to contribute to future catastrophic board or system failures.
Also, digital detector technology in both X-ray and CT scanning systems is constantly improving, thereby enabling us to capture images, and defects, at finer resolutions (often in the sub-micron range), that are essential for today’s microelectronics failure analysis.
What are the biggest misconceptions of X-ray technologies?
Boguski: Confusion in terminology, especially between 2D and 3D X-ray. Shady operators exploit this ignorance to their own advantage. For example, CT scanning is nothing more than the amalgamation of multiple 2D X-ray images into a three-dimensional whole for analysis. A lot of powerful software and computing power is needed to achieve this, and we do it every day.
Another frequent human problem is the know-it-all—a “TechBro” process engineer who has anointed themselves as “God’s Gift to Failure Analysis,” and who has predetermined the outcome in their own minds. This often begs the question of why they are requesting our services in the first place. People are funny. Beware of anyone who prefaces the discussion with, “In my years of working in this industry, I have never seen a defect such as you claim to see,” to which we usually reply, “You need to get out more.” It’s tough to address a solid-state world possessed of a vacuum tube mindset.
Conclusion
Thank you to Jesper and Robert. In the fast-paced world of electronics manufacturing, the pursuit of reliability and precision is relentless. As circuit assemblies become more complex, with finer pitches, denser components, and hidden solder joints, traditional inspection methods often fall short. This is where X-ray technology steps in as a game-changer, allowing manufacturers to see beyond the surface, identify hidden defects, and ensure the integrity of their products.
This column originally appeared in the April 2025 issue of SMT007 Magazine.
More Columns from The Knowledge Base
The Knowledge Base: Cultivating Your Brand in the Age of ConnectionThe Knowledge Base: A Conference for Cleaning and Coating of Mission-critical Electronics
The Knowledge Base: Building the Workforce of Tomorrow With EMAC
The Knowledge Base: Beyond the Badge—Why Membership Matters More Than Ever
The Knowledge Base: At the Forefront of Electronics Manufacturing
The Knowledge Base: Challenges and Considerations of Harsh Environments
The Knowledge Base: My 2025 Industry Wish List
The Knowledge Base: The Era of Advanced Packaging