-
- News
- Books
Featured Books
- pcb007 Magazine
Latest Issues
Current IssueIn Pursuit of Perfection: Defect Reduction
For bare PCB board fabrication, defect reduction is a critical aspect of a company's bottom line profitability. In this issue, we examine how imaging, etching, and plating processes can provide information and insight into reducing defects and increasing yields.
Voices of the Industry
We take the pulse of the PCB industry by sharing insights from leading fabricators and suppliers in this month's issue. We've gathered their thoughts on the new U.S. administration, spending, the war in Ukraine, and their most pressing needs. It’s an eye-opening and enlightening look behind the curtain.
The Essential Guide to Surface Finishes
We go back to basics this month with a recount of a little history, and look forward to addressing the many challenges that high density, high frequency, adhesion, SI, and corrosion concerns for harsh environments bring to the fore. We compare and contrast surface finishes by type and application, take a hard look at the many iterations of gold plating, and address palladium as a surface finish.
- Articles
- Columns
Search Console
- Links
- Media kit
||| MENU - pcb007 Magazine
Not All Plating Lines Are Created Equal
February 12, 2020 | I-Connect007 Editorial TeamEstimated reading time: 12 minutes
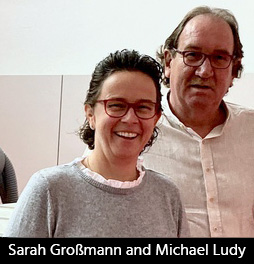
Barry Matties and Happy Holden met with CEO Michael Ludy and CMO Sarah Großmann from Ludy, a company specializing in galvanic plating equipment for PCBs. During one of I-Connect007’s visit to GreenSource Fabrication, the team found Ludy equipment being utilized there, so Barry and Happy traveled to their factory in Germany to learn more about the company.
The following interview gives an overview of Ludy and their latest advancements in PCB plating equipment.
Barry Matties: Let’s start with a little bit about your product.
Sarah Großmann: We produce galvanic plants for PCBs. That’s our main task. We have a highly specialized way of having the galvanic tanks and the geometry of the tanks, where the plating and the aspect ratio is much better. We tried to focus mainly on PCBs in the past years. We fulfilled the demands and ideas of Alex Stepinski and what he thought could work. We are flexible and gave him a plant with the newest technology. He can fulfill his plating demands and multiple processes internally.
Generally, this is the main thing we do, but we also do the research for waste-air-free and wastewater-free galvanic plants like the GalvanoMat® PCB. That’s our main idea of fulfilling a complete green fabrication in one. You have one container where the galvanic plant is inside, and one container getting the waste air, wastewater, and energy recovery, and everything goes in one circle. You don’t have to waste that much and fulfill all the green fabrication requirements that are needed.
We have it for metal finishing and PCBs. We’re trying to get back in the U.S. market. We were there already. The lines are still running, and it’s going more and more to green fabrication. This is why we mostly do R&D for the GalvanoMat® PCB.
Figure 1: Overview of the latest generation of Ludy plating line with split-tank hoist access.
Happy Holden: People would probably buy brand new plating equipment because of high-density interconnect (HDI) and substrate-like PCBs (SLPs). All of which have very tiny holes and a much higher aspect ratio, which the conventional anode to cathode and one-axis agitation or area agitation is not sufficient for the throwing power and things like that.
Großmann: The anodes are inside, and every one of those segmented anodes is separately controlled by a rectifier.
Holden: Can you do pulse plating too?
Großmann: It would be possible, depending on the chemistry. The problem is that in the galvanic plant area, the people stick to what they know and don’t want to invest high amounts of money for testing around. This is a problem. That’s why the research steps are not very fast compared to other machine areas. They know that the chemistry is also influencing this area, and if Atotech says they’re not sure, then nobody will invest money on that. That’s why we are pretty happy that our solution worked and was inclusive with a 3D agitation drive. We have a very good distribution overall of the PCB on both sides. Those are the main benefits of the system.
Holden: The North American market has the common board, but then they have leading-edge things for medical, aerospace, or radar, where they want to go to a much higher aspect ratio both on through-holes and on blind vias. The problem is typical galvanic equipment isn’t there yet. Some believe the Ludy equipment will take them there, which means adopting the old way. There’s a big difference in productivity between four hours and 50 minutes.Page 1 of 4
Suggested Items
Preventing Surface Prep Defects and Ensuring Reliability
06/10/2025 | Marcy LaRont, PCB007 MagazineIn printed circuit board (PCB) fabrication, surface preparation is a critical process that ensures strong adhesion, reliable plating, and long-term product performance. Without proper surface treatment, manufacturers may encounter defects such as delamination, poor solder mask adhesion, and plating failures. This article examines key surface preparation techniques, common defects resulting from improper processes, and real-world case studies that illustrate best practices.
RF PCB Design Tips and Tricks
05/08/2025 | Cherie Litson, EPTAC MIT CID/CID+There are many great books, videos, and information online about designing PCBs for RF circuits. A few of my favorite RF sources are Hans Rosenberg, Stephen Chavez, and Rick Hartley, but there are many more. These PCB design engineers have a very good perspective on what it takes to take an RF design from schematic concept to PCB layout.
Trouble in Your Tank: Causes of Plating Voids, Pre-electroless Copper
05/09/2025 | Michael Carano -- Column: Trouble in Your TankIn the business of printed circuit fabrication, yield-reducing and costly defects can easily catch even the most seasoned engineers and production personnel off guard. In this month’s column, I’ll investigate copper plating voids with their genesis in the pre-plating process steps.
Elephantech: For a Greener Tomorrow
04/16/2025 | Marcy LaRont, PCB007 MagazineNobuhiko Okamoto is the global sales and marketing manager for Elephantech Inc., a Japanese startup with a vision to make electronics more sustainable. The company is developing a metal inkjet technology that can print directly on the substrate and then give it a copper thickness by plating. In this interview, he discusses this novel technology's environmental advantages, as well as its potential benefits for the PCB manufacturing and semiconductor packaging segments.
Trouble in Your Tank: Organic Addition Agents in Electrolytic Copper Plating
04/15/2025 | Michael Carano -- Column: Trouble in Your TankThere are numerous factors at play in the science of electroplating or, as most often called, electrolytic plating. One critical element is the use of organic addition agents and their role in copper plating. The function and use of these chemical compounds will be explored in more detail.