Innovators Create Flexible, Printed Coil for Stringed Instruments
September 10, 2020 | Purdue UniversityEstimated reading time: 1 minute
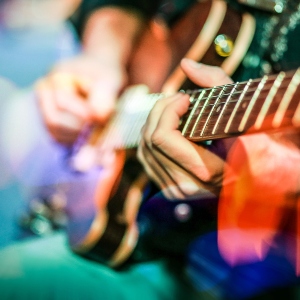
The wires inside an electric guitar to help produce quality sound can stretch for miles – even the length of a university campus. The copper wire, with the diameter of a human hair, is wrapped around magnets inside the guitar via a tedious and time-consuming process.
Now, Purdue University innovators have developed a solution to cut down that process and make the finished products better for players and manufacturers.
The team created a flexible, printed circuit board that imitates the conventional wire configurations inside an electric guitar. Existing guitars can be retrofitted with this innovation. The technology also has applications for other stringed instruments.
“We came up with a new approach to the electric guitar pickup – the magnetic transducer that helps create the musical sound,” said Davin Huston, an assistant professor of practice in engineering technology in the Purdue Polytechnic Institute. “Our circuit boards can be printed in large quantities and fit inside just about any electric guitar, which simplifies the manufacturing process but keeps the sound quality and reliability.”
The other members of the Purdue innovation team include Mark French, a professor of mechanical engineering technology in Purdue Polytechnic, and Kathryn Smith, a former graduate student in Huston’s lab.
The Purdue team’s circuit board works in the same general way as a conventional electric guitar pickup – string vibrations cause the electromagnetic field to oscillate and induce a voltage in the stationary coil. The electric signal generated is then carried to a power amplifier and speaker.
“With typical pickups, the wire coils often produce undesired feedback and need to be potted with wax or a polymer,” French said. “Our circuit board provides an alternative that is easier to produce with manufactured consistency.”
The team worked with the Purdue Research Foundation Office of Technology Commercialization to patent the technology. A U.S. patent has been granted on this technology.
The creators are looking for partners to continue developing their technology and license it. For more information, contact D.H.R. Sarma of OTC at dhrsarma@prf.org and reference track code 2013-HUST-66596.
Testimonial
"Advertising in PCB007 Magazine has been a great way to showcase our bare board testers to the right audience. The I-Connect007 team makes the process smooth and professional. We’re proud to be featured in such a trusted publication."
Klaus Koziol - atgSuggested Items
Global PCB Connections: Understanding the General Fabrication Process—A Designer’s Hidden Advantage
08/14/2025 | Markus Voeltz -- Column: Global PCB ConnectionsDesigners don’t need to become fabricators, but understanding the basics of PCB fabrication can save you time, money, and frustration. The more you understand what’s happening on the shop floor, the better you’ll be able to prevent downstream issues. As you move into more advanced designs like HDI, flex circuits, stacked vias, and embedded components, this foundational knowledge becomes even more critical. Remember: the fabricator is your partner.
MKS’ Atotech to Participate in IPCA Electronics Expo 2025
08/11/2025 | AtotechMKS Inc., a global provider of enabling technologies that transform our world, announced that its strategic brands ESI® (laser systems) and Atotech® (process chemicals, equipment, software, and services) will showcase their latest range of leading manufacturing solutions for printed circuit board (PCB) and package substrate manufacturing at the upcoming 17th IPCA Show to be held at Pragati Maidan, New Delhi from August 21-23, 2025.
MKS Showcases Next-generation PCB Manufacturing Solutions at the Thailand Electronics Circuit Asia 2025
08/06/2025 | MKS Instruments, Inc.MKS Inc, a global provider of enabling technologies that transform our world, today announced its participation in Thailand Electronics Circuit Asia 2025 (THECA 2025), taking place August 20–22 at BITEC in Bangkok.
Point2 Technology, Foxconn Interconnect Technology Partner to Revolutionize AI Cluster Scalability with Terabit-Speed Interconnect
08/06/2025 | BUSINESS WIREPoint2 Technology, a leading provider of ultra-low-power, low-latency mixed-signal SoC solutions for multi-terabit interconnect, and Foxconn Interconnect Technology (FIT), a global leader in precision interconnect solutions, have signed a Memorandum of Understanding (MOU) to accelerate the commercialization of next-generation Active RF Cable (ARC) and Near Pluggable e-Tube (NPE) solutions.
Advancing Electrolytic Copper Plating for AI-driven Package Substrates
08/05/2025 | Dirk Ruess and Mustafa Oezkoek, MKS’ AtotechThe rise of artificial intelligence (AI) applications has become a pivotal force driving growth in the server industry. Its challenging requirements for high-frequency and high-density computing are leading to an increasing demand for development of advanced manufacturing methods of package substrates with finer features, higher hole densities, and denser interconnects. These requirements are essential for modern multilayer board (MLB) designs, which play a critical role in AI hardware. However, these intricate designs introduce considerable manufacturing complexities.