-
- News
- Books
Featured Books
- pcb007 Magazine
Latest Issues
Current IssueVoices of the Industry
We take the pulse of the PCB industry by sharing insights from leading fabricators and suppliers in this month's issue. We've gathered their thoughts on the new U.S. administration, spending, the war in Ukraine, and their most pressing needs. It’s an eye-opening and enlightening look behind the curtain.
The Essential Guide to Surface Finishes
We go back to basics this month with a recount of a little history, and look forward to addressing the many challenges that high density, high frequency, adhesion, SI, and corrosion concerns for harsh environments bring to the fore. We compare and contrast surface finishes by type and application, take a hard look at the many iterations of gold plating, and address palladium as a surface finish.
It's Show Time!
In this month’s issue of PCB007 Magazine we reimagine the possibilities featuring stories all about IPC APEX EXPO 2025—covering what to look forward to, and what you don’t want to miss.
- Articles
- Columns
Search Console
- Links
- Media kit
||| MENU - pcb007 Magazine
DFM from the Fabricator’s Point of View
August 31, 2021 | Andy Shaughnessy, Design007 MagazineEstimated reading time: 4 minutes
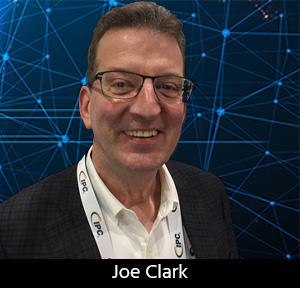
What do you think of when you hear the term DFM? By its very definition, design for manufacturing tends to focus on what designers need to do to make sure that fabricators can manufacture their boards according to design intent.
But what about the flip side of this equation? What should the fabricator do to facilitate better DFM practices? The I-Connect007 Editorial Team posed this question to a trio of design and fabrication experts: DownStream Technologies co-founders Joe Clark and Rick Almeida, and Max Clark, business unit manager for Valor at Siemens EDA. We think you’ll enjoy this wide-ranging conversation.
Andy Shaughnessy: We’ve run a lot of coverage of DFM, and it tends to be from the designer’s point of view, so we wanted to get it from the other side. Because you deal with both sides of the equation, what would the fabricator like to see from the designers, as far as DFM?
We’ve heard some designers say that fabricators won’t tell them their capabilities. They’ll say, “Look on our website.”
Joe Clark: Often the fabricators do keep their cards close to their chest.
Barry Matties: Why is that?
Joe Clark: Why do fabricators gladly accept Gerbers rather than intelligent data, which is going to make the handshake that much better? Max can certainly jump in here from his experience, but many times it’s nothing more than a fear that if they push them to get the intelligent data, the customer will go somewhere else. But virtually every CAD tool today supports ODB or 2581, so obtaining these formats should not be a problem.
Max Clark: That’s a good question. I suggest we divide this discussion into things like data exchange, and then maybe manufacturing capabilities exchange, because they’re two separate topics. From a data exchange, you’re right. Part of the challenge there is acceptance. I work with a lot of the OEM sides wanting to use ODB++ and the challenges that we go through there is they must accept internally that it’s what they want to do. It usually becomes a type of decision to say, “We’re going to send this, and that’s it.” And the fabricator just learns to live with it. That’s usually the way it seems to go.
But before they’re willing to make that leap, they don’t have confidence in themselves that the transfer will be successful, that the manufacturer can work with it. We end up going through what might be several weeks, or even several months, of back and forth, comparing designs. They want to try every type of design they have. If they have multiple EDA tools they want to test it on all the EDA tools because they want to commit to it all at once. Then we end up going back and forth with the fabricators to obtain their acceptance. While this is not DFM related it’s still what hinders them from a DFM perspective.
Matties: My understanding is that there are some manufacturers offering price discounts if you’re using IPC-2581.
Max Clark: Yes. That’s been tried even with ODB++ in the past, using it as a carrot to get data faster. The transfer is smarter; I don’t care whether you’re using 2581 or ODB++ from that perspective. The exchange is smarter, faster, it gets in the system, and more comes in correctly the first time, so that’s a huge advantage. I think the first hurdle people must get over when it comes to DFM acceleration is the acceptance of a new, better, or improved-upon way to transfer that data. The analysis that you perform, either on the design side or the fab side, is only as good as the data you’re being presented with. From my experience, trying to reverse engineer that intelligence into the Gerber data is only so accurate, and it is time consuming.
Matties: Is this a generational issue? Will the young engineers gladly use IPC-2581 if we train them to that?
Max Clark: I don’t think so. There’s a mirror image of this in silicon manufacturing where the foundries at first were very inward looking and they didn’t want to share a lot of information. I think it’s just a matter of maturity within the industry. It needs to evolve. Possibly the fabricators must do more insistence. Fabricators say, “They don’t want to lose any business.” They’re afraid the customers will go somewhere else. That fear has got to leave.
Rick Almeida: They’ve been using Gerber a long time, and with all its warts, it still works for the design side. These guys are getting older and older. It’s just ingrained in them that when you’re done you’re going to produce Gerber and go. Unless there’s some compelling reason to switch that process nobody really gets a couple months where there’s no work to do and they can go in and try a different process for the sake of trying a different process.
To read this entire conversation, which appeared in the August 2021 issue of PCB007 Magazine, click here.