-
- News
- Books
Featured Books
- pcb007 Magazine
Latest Issues
Current IssueSales: From Pitch to PO
From the first cold call to finally receiving that first purchase order, the July PCB007 Magazine breaks down some critical parts of the sales stack. To up your sales game, read on!
The Hole Truth: Via Integrity in an HDI World
From the drilled hole to registration across multiple sequential lamination cycles, to the quality of your copper plating, via reliability in an HDI world is becoming an ever-greater challenge. This month we look at “The Hole Truth,” from creating the “perfect” via to how you can assure via quality and reliability, the first time, every time.
In Pursuit of Perfection: Defect Reduction
For bare PCB board fabrication, defect reduction is a critical aspect of a company's bottom line profitability. In this issue, we examine how imaging, etching, and plating processes can provide information and insight into reducing defects and increasing yields.
- Articles
- Columns
- Links
- Media kit
||| MENU - pcb007 Magazine
New Methods for Quantifying PCB Design Weaknesses and Manufacturing Challenges
November 18, 2021 | Nolan Johnson, I-Connect007Estimated reading time: 3 minutes
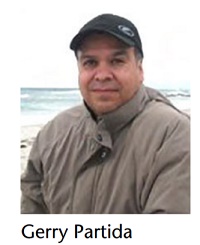
Nolan Johnson recently spoke with Summit Interconnect’s Gerry Partida about disruptive new methods for analyzing and quantifying potential manufacturing challenges in designs while still in the design phase.
Nolan Johnson: Gerry, what’s the background for the new methods we’re about to discuss?
Gerry Partida: The industry is at a new point in evolving how we look at building boards. Our industry has historically built boards and then tried to find a test for them. Then, when they found a test for it, they figured out that it needed to be analyzed before they built the board. We did this with electrical test. We built boards and down the road, as people started asking, “Why am I buying bad boards? We should electrically test them,” electrical test was introduced, reluctantly, into the test part of manufacturing printed circuit boards by suppliers or fabricators. Then they embraced it. But when we started testing boards, we did comparison tests. We would build a bunch of boards, put the first one on a tester, tell it to self-learn, and compare all the boards to the first board. If they all matched, they all shipped as matched boards, but if they had the same defect, they all shipped with the same defect. This did happen.
It wasn’t for another 10 or 15 years that we took extracted netlist from the CAD software and compared it to the Gerber data that would be used to fabricate the board, to find out whether everything was corrected before we started manufacturing. We would find that there was a problem, and we would fix it or get new data. Then when we knew we had a match, we started to manufacture the boards and downloaded the program to the tester. But this was an evolution of about 15 to 25 years. It depends on what point of view you take from it.
We’ve done the same thing with microvias. We’ve been building microvias. There are datasheets that talk about the modulus and the CTE expansion after reflow, before Tg, and after Tg, but no one really would do any math or science behind it. The PCB fabricator would just build the boards and ship them. Sometimes there are assembly problems, and the industry says, “There’s something going on with microvias. Three-stack and four-stack are not as safe as a single microvia and staggering them.” Everybody is trying to find out how strong or how weak they are. Most people were finding out at assembly because the standard IPC-6012 performance specs in the evaluation couldn’t identify a weak microvia very well. So, we came up with the OM tester, which is using the IPC-TM 650 2.6.27 test method, which actually takes a coupon with the same structures that are in the board and simulates reflow on the coupon before we ship the boards.
If that structure, which is in the board that we’re trying to ship, can survive reflow in a tester, then we know that the boards are more than likely going to pass and survive reflow and assembly. This works great. It will tell fabricators that if we process everything right, the board is going to be reliable through reflow. However, after a couple years of having the tester, we discovered we did everything right, but occasionally it wasn’t working. They were failing 6X reflow. Utilizing our extensive experience in microvia fabrication, our portfolio of reliability testing data, materials expertise and software tools, we can simulate the stack-up; you can actually input the microvia structure and the data output will tell you if it can survive six reflows or not.
To read this entire conversation, which appeared in the November 2021 issue of PCB007 Magazine, click here.
Suggested Items
TRI to Exhibit at SMTA Queretaro Expo 2025
07/16/2025 | TRITest Research, Inc. (TRI), the leading provider of test and inspection systems for the electronics manufacturing industry, is pleased to announce plans to exhibit at the SMTA Querétaro Expo 2025, scheduled to take place on July 24, 2025, at the Querétaro Centro de Congresos y Teatro Metropolitano.
Global PCB Connections: Let the Spec Fit the Board, Not Just the Brand
07/17/2025 | Jerome Larez -- Column: Global PCB ConnectionsIf you’ve ever seen an excellent PCB quote delayed, or worse, go cold because of a single line on the fab print, you’re not alone. Often, that line reads something like, “Use 370HR only,” or “IT-180A required.” These and other brand-name materials are proven performers, but unless your design needs that specific resin system (say, for RF performance, thermal reliability, or stringent CAF resistance), you may inadvertently be holding your job hostage.
IPC Hall of Fame Spotlight Series: Highlighting Lionel Fullwood
07/15/2025 | Dan Feinberg, I-Connect007Many IPC members who have contributed significantly to IPC and our industry have been awarded the IPC Raymond E. Pritchard Hall of Fame (HOF) Award. Though many early HOF members have passed away and are unknown to today’s IPC membership, their contributions still resonate. This special series on IPC Hall of Fame members provides a reminder of who was honored and why. As a bonus, for those who are still around, we get to find out what these talented individuals are up to today.
TRI Unveils New Platform for Diverse Board Sizes
07/14/2025 | TRITest Research, Inc. (TRI), the leading test and inspection systems provider for the electronics manufacturing industry, proudly introduces a new size configuration for SPI and AOI Models.
Seeing a Future in Mexico
07/09/2025 | Michelle Te, I-Connect007The Global Electronics Association (formerly known as IPC) has been instrumental in fostering a partnership with Guanajuato, a state north of Mexico City with 12 industrial clusters and close to 150 companies involved in electronics. This past spring, Alejandro Hernández, the undersecretary for investment promotion in Guanajuato, attended IPC APEX EXPO 2025 at the invitation of IPC Mexico Director Lorena Villanueva, where he met with several companies to discuss the opportunities available in Mexico. He is inviting electronics-related companies seeking long-term investment in a centrally located area with access to highways, railways, and ports.