All Flex Discusses Merger and New Medical Applications
November 19, 2021 | Nolan Johnson, I-Connect007Estimated reading time: 4 minutes
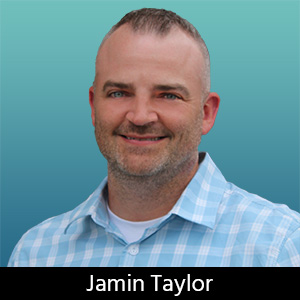
I recently spoke with Jamin Taylor, vice president of sales and marketing at All Flex Flexible Circuits in Minnesota. We discussed the company’s recent merger with Printed Circuits Inc., and some creative new flex applications, including flexible heaters and catheters for the medical field.
Nolan Johnson: There’s been some news recently for All Flex. Why don’t we start with the announcement of the merger?
Jamin Taylor: About nine months ago, our parent company purchased Printed Circuits Inc. out of Bloomington, Minnesota with the plans of merging the two companies. We’re in the planning process right now with PCI to create a single entity and look at rebranding. The two companies have really expanded our technologies, with All Flex and our flexible circuits, and PCI and their rigid flex capability. Now we can expand our product offering to our customer base in the U.S.
Johnson: Were there any pleasant surprises in capabilities now that you’ve got the two companies together?
Taylor: It’s always interesting to see different technologies amongst different companies. We’re working on a few new applications and products, like being able to do some fine lines and flex materials, but with large format, a longer format than usual. Some of their capabilities with lasering and fine features really help with our long flex capability; when we merge the two, we see a new market being created for that technology.
Johnson: I understand you’re now developing fine-line catheters. Tell me about that.
Taylor: Fine line means small features, 2-mil lines and spaces; that’s not new to the industry, but being able to do it in five-, six-, and seven-foot lengths is new. This is for catheter applications in the medical space. We trademarked Fine-Line Maxi Flex and CatheterFlex. The Medtronics and Boston Scientifics of the world that are doing heart-mapping, heart ablation for AFib, for example, will now be able to do it less invasively by going through the femoral artery up into the heart.
To map or to ablate, you need electronics; using traditional wires was okay, but they’re running out of space. You can’t make this as large as possible. The flexible circuit allows us to get 64 or 128 channels down the length of this catheter in a much smaller, much more flexible format than traditional wires. It’s really enabling the capability of mapping and providing more resolution for mapping of the heart. We’re seeing a pretty significant interest amongst the big players in this type of technology.
Johnson: Has there been other creative development ongoing in your R&D development team?
Taylor: Yes, we’re also looking at flexible heaters. Traditional flex circuits are made with copper low resistance, right? We’re transferring signals, or maybe some high current carrying features. There’s also the ability to use a resistive foil and create a heating element. The thin film of the traditional polyimides allows for extremely fast heat transfer; with COVID, and in some of the testing that’s been done, there’s a huge demand for heating elements in biomedical, bacterial, or viral testing. The flu, colds, and coronaviruses can all be tested in a lab and that lab has to heat up the tissue sample or the DNA sample to a specific temperature and then get a positive or a negative.
The flexible heater technology is not something new. There just haven’t been many players in that market. It has been beneficial to be able to do some fine line features, some long features, as well as etch resist to foils. We really looked at that market and think we can expand upon it. We can bring some of the rigid flex capabilities that PCI has, couple that together, and really broaden our market for flexible heating.
Johnson: I’m sensing that with this merger, you’re finding some creative ways to diversify.
Taylor: Absolutely. PCI has been a high-tech company. They’ve focused on military applications, complexity, multiple layer counts. So, they’ve developed a lot of good technologies for microvias, blind vias, and fill vias, and we’ve brought our flex knowledge with medical applications specifically. We’re able to bring a lot of medical customers into that rigid-flex territory. And then they’re able to bring a lot of the military and aerospace customers into the flex, and we also do full assembly in-house. That’s something that All Flex brings to the table, being able to populate these boards, and with rigid flex, it’s like a motherboard combined with an interconnect, right? There are always components being populated and PCI didn’t have that capability. Now we can do more value-add as a combined company and maybe in the future, box-build is something we could continue to look at.
Johnson: Jamin, thank you for the update.
Taylor: I appreciate it. Thank you very much.
This conversation originally appeared in the November 2021 issue of Design007 Magazine.
Suggested Items
I-Connect007 Editor’s Choice: Five Must-Reads for the Week
07/18/2025 | Nolan Johnson, I-Connect007It may be the middle of the summer, but the news doesn’t quit, and there’s plenty to talk about this week, whether you’re talking technical or on a global scale. When I have to choose six items instead of my regular five, you know it’s good. I start by highlighting my interview with Martyn Gaudion on his latest book, share some concerning tariff news, follow that up with some promising (and not-so-promising) investments, and feature a paper from last January’s inaugural Pan-European Design Conference.
Elephantech Launches World’s Smallest-Class Copper Nanofiller
07/17/2025 | ElephantechJapanese deep-tech startup Elephantech has launched its cutting-edge 15 nm class copper nanofiller – the smallest class available globally. This breakthrough makes Elephantech one of the first companies in the world to provide such advanced material for commercial use.
Copper Price Surge Raises Alarms for Electronics
07/15/2025 | Global Electronics Association Advocacy and Government Relations TeamThe copper market is experiencing major turbulence in the wake of U.S. President Donald Trump’s announcement of a 50% tariff on imported copper effective Aug. 1. Recent news reports, including from the New York Times, sent U.S. copper futures soaring to record highs, climbing nearly 13% in a single day as manufacturers braced for supply shocks and surging costs.
I-Connect007 Editor’s Choice: Five Must-Reads for the Week
07/11/2025 | Andy Shaughnessy, Design007 MagazineThis week, we have quite a variety of news items and articles for you. News continues to stream out of Washington, D.C., with tariffs rearing their controversial head again. Because these tariffs are targeted at overseas copper manufacturers, this news has a direct effect on our industry.I-Connect007 Editor’s Choice: Five Must-Reads for the Week
Digital Twin Concept in Copper Electroplating Process Performance
07/11/2025 | Aga Franczak, Robrecht Belis, Elsyca N.V.PCB manufacturing involves transforming a design into a physical board while meeting specific requirements. Understanding these design specifications is crucial, as they directly impact the PCB's fabrication process, performance, and yield rate. One key design specification is copper thieving—the addition of “dummy” pads across the surface that are plated along with the features designed on the outer layers. The purpose of the process is to provide a uniform distribution of copper across the outer layers to make the plating current density and plating in the holes more uniform.