-
- News
- Books
Featured Books
- pcb007 Magazine
Latest Issues
Current IssueVoices of the Industry
We take the pulse of the PCB industry by sharing insights from leading fabricators and suppliers in this month's issue. We've gathered their thoughts on the new U.S. administration, spending, the war in Ukraine, and their most pressing needs. It’s an eye-opening and enlightening look behind the curtain.
The Essential Guide to Surface Finishes
We go back to basics this month with a recount of a little history, and look forward to addressing the many challenges that high density, high frequency, adhesion, SI, and corrosion concerns for harsh environments bring to the fore. We compare and contrast surface finishes by type and application, take a hard look at the many iterations of gold plating, and address palladium as a surface finish.
It's Show Time!
In this month’s issue of PCB007 Magazine we reimagine the possibilities featuring stories all about IPC APEX EXPO 2025—covering what to look forward to, and what you don’t want to miss.
- Articles
- Columns
Search Console
- Links
- Media kit
||| MENU - pcb007 Magazine
Are You Still Over-materializing?
June 29, 2023 | Barry Matties, I-Connect007Estimated reading time: 9 minutes
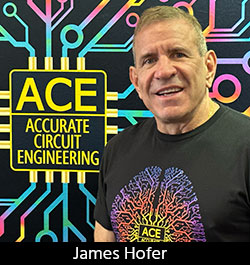
During the recent IEEE IMS2023 Exhibition in San Diego, we caught up with James Hofer, general manager of Accurate Circuit Engineering (ACE). The company is a prototype manufacturer of bare printed circuit boards that specializes in high-mix, low volume with an emphasis on RF, microwave, and antennas. A few years ago, we talked to James about the over-materialization of boards. In this recent discussion, we wanted to know if anything has changed regarding materials and approach. James also shares his thoughts on the changes in the design community.
Barry Matties: We're here at the microwave show, speaking with James Hofer. What does a show like this do in terms of helping you look at market trends?
James Hofer: This show is important not only because of the attendees but the exhibitors as well. I can walk the show floor, see what the exhibitors have, and their marketing direction. That helps us keep abreast of the changes in market technology and direction so that we can stay abreast of those.
Matties: You and I had done an interview regarding materials a few years ago on over-materializing, and you use a full range of materials in your shop. Talk about materials and what people should be thinking about right now.
Hofer: In RF, microwave, and antennas, you have your RX and TX layers, which are your receivers and transmitters. That’s where you sometimes need your more costly dielectrics, those that are more effective in that application. However, there are other layers, for example, in an antenna. Your feed layers are just directing the power to your antenna, your receiver, or your transmitter. Those layers can typically use a more cost-effective material. we don’t have issues using different materials working together in the same build . We’ve always been focused on doing hybrid stackups, which puts the expensive material where you need it and the more cost-effective material where you need it. We work with our customers to weed out costs from the board because, let's face it, if you want good performance you have to pay for it. Reducing costs where you can makes good sense. Why pay for a race car if you're only driving from stoplight to stoplight?
Matties: What do the designers need to know or why are they missing it?
Hofer: I've seen many engineers want their build to be bulletproof so they look for the absolute best performance materials they can get. They tend to look at this as, “If I change a material here or there, it may affect my performance.” In the current market, being the best performing, and the first one out is critical to almost everybody. It's your manufacturer’s job—our job—to help ease your concerns and show you that with data you don't have to overbuild. As an engineer, you just want to make it bulletproof. What you really need is to get the job done so that it lasts and performs well, but it doesn't have to necessarily be over-modeled right now.
Matties: Materials and density have changed a lot in the last handful of years. How is that affecting your business and what kind of technologies do you have to bring to match?
Hofer: Density is definitely an issue. We have been continuing to reduce line width, spacing, radius, hole size, and drill spans—there's just a plethora of technology emerging every day. I've looked at some alternative technologies, but unfortunately, they're not proven yet. However, we are keeping a keen eye on developments and technology. AI is strongly emerging in the software universe, we are poised and ready when it enters the hardware side.
Matties: When we start looking at the surface of the material, that’s obviously critical, so you partner with multiple suppliers. Talk about how that relationship with your core material suppliers and why it's so critical.
Hofer: ACE always strives to be our vendors’ best customer, and we work closely with a lot of the high-speed laminate manufacturers. We also work closely with the resistive FOIL folks. We're trying to stay on the cutting edge of beta testing these laminates and materials. We’re a prototype shop, so most of our customers are in the design stage—at the beginning of the release of their product. Our partnerships with manufacturers helps us not only recommend materials but It also helps in our availability of materials because we work so closely with our suppliers. We’re able to call someone and say, “Hey, can you pull out some of that sample material you have ?” Or “I know you've have a few panels from the test we ran a few months ago that you haven't used yet. Can you share those with us?” That brings in added benefits.
Matties: With density increasing, how important is material surface?
Hofer: We're doing more low-profile PTFE than ever. Weare changing rotation on parts to follow the weave of the glass on reinforced materials. Unreinforced, flat weave and spread weave product and material surface is very important. A lot of engineers feel that the surface of the copper—on the outer outermost region of the copper, not at the copper laminate interface—is as important as the dielectric copper interface. However, tests done by material manufacturers have shown that it’s not nearly as important. The most critical interface is the copper to the dielectric
However, we have had a lot of engineers ask about our surface roughness on top of the copper and one of the difficulties I face as a fabricator is explaining that your board design dictates the roughness of your surface copper. The surface, to me, is a processing surface because I don't process dielectric to copper; I process the outermost region of the copper. If you request via fill, or if you are at terminations of blind vias, that copper has to be rougher than if it is just a standard inner layer. If it's an outer layer and I'm electrodepositing copper on there, it is a lot smoother because I'm putting fresh, smooth copper on the surface. We work to communicate that. It’s absolutely an issue.
Matties: Are you seeing more front-end collaboration with the designers?
Hofer: Yes, with customers who have experience with us. One of our best attributes is, “Let me work with you on your design collaboration and we do this at no cost or obligation. So if you like the things we discussed write them into your documents because if you don't end up building with me, this will help you with your other fabricators as well.”
Matties: What do you think the core concern should be for designers today?
Hofer: That's a tough question because several answers come to mind. One is, “Trust but verify.” Two, don't always go with what the sales guys tell you. Talk to a process guy because they're the ones on the floor making it happen. Absolutely, the gospel should be to work with your fabricator.
Matties: One of the things that we see is an aging design community. Do you see younger designers coming into the space?
Hofer: Yes, I am also seeing a lot of folks bringing on young interns and helping them get interested in the industry.
Matties: Is their approach different than what we're traditionally accustomed to from a designer?
Hofer: It is where some of us (me included) dinosaurs in the industry that tend to want almost complete control over what we do, while the younger team wants to automate more and more. They want an intuitive situation, like AI, that can autofill, auto route and soon auto design. They're more technologically dependent but I personally use that hesitantly because I just don't know that it's entirely a good thing. I think the younger generation does bring fresh ideas and approaches to the table, and that's good. That's always good in every situation.
Matties: It seems to be because of the digital upbringing. I mean, they were born with a digital device in their hand. Are they looking for more of a digital factory, that digital interface?
Hofer: Yes and no. Automation is great and important in many areas. But I'm fortunate in that, from my experience, much of the next generation is okay with a bit of personal interface. That seems to work in our favor because they don't get that from all manufacturers. They seem surprised. Some of the more common statements I hear are, “Wow, I didn't know you could tell me that”. Or “I didn't know I could call you and see how my boards are doing”. Or ‘I didn't know I could come down and see them in process”. Of course my favorite is “Thanks for lunch.” I want to keep promoting that real life interface because you simply can't get from digital interface what you can get from human interface.
Matties: It's interesting that you mentioned coming down into the factory because sometimes we hear, “I don't need to see a factory. They can give me a video tour. I can see it online.” It's just not the same, as you're pointing out.
Hofer: I will give you a great example. Anybody can make a video that details all their best aspects. But when you walk through the factory, you can turn your head and maybe see what wouldn’t be included in a video—things that would spur a question that I can answer on the spot. I run into this all the time with customers on a video call, where I'll explain something, and they really don't know what I'm talking about. If only I could just show them, I know they’d get it. Hence, my favorite comment is “thanks for lunch”. I know a good way to lure engineers is good food: “Yeah, come down and I'll feed you as we walk through.”
Matties: How many jobs are you processing through your facility a month?
Hofer: On a good month, about a couple hundred jobs through the shop. On a slower month, about 100 from front to back, all the way through.
Matties: That's a lot of moving parts. Any final thoughts that you'd like to share with industry?
Hofer: Stay with it. Young people who think, they are not really interested electrical design or printed circuit board design, should know that the technologies that are emerging today, that you can be hands on from the start. are tomorrows world. For me, I love what I do because I'm working on stuff that we'll see in three years, and in 10 years will be part of our everyday life. It's so cool to help bring tomorrow’s world into realization..
Matties: Oftentimes, I feel like we don't share enough of that end result purpose that this industry is affecting. We're going to the moon, we're in autonomous cars, medical devices; we're saving lives, simply by building a circuit board.
Hofer: Yeah, that's exactly right. I try to make an added effort to show the result of the boards we build back to the shop, right down to my guy who's just cutting laminate or copper sheets all day. I let them know that the car that you just watched somebody call for while they waited at a corner, the car came by itself picked them up and drove them off—that board you cut material for last week or last month or last year was part of what made that happen
Matties: James, thank you.
Hofer: Thank you.
Suggested Items
RF PCB Design Tips and Tricks
05/08/2025 | Cherie Litson, EPTAC MIT CID/CID+There are many great books, videos, and information online about designing PCBs for RF circuits. A few of my favorite RF sources are Hans Rosenberg, Stephen Chavez, and Rick Hartley, but there are many more. These PCB design engineers have a very good perspective on what it takes to take an RF design from schematic concept to PCB layout.
Trouble in Your Tank: Causes of Plating Voids, Pre-electroless Copper
05/09/2025 | Michael Carano -- Column: Trouble in Your TankIn the business of printed circuit fabrication, yield-reducing and costly defects can easily catch even the most seasoned engineers and production personnel off guard. In this month’s column, I’ll investigate copper plating voids with their genesis in the pre-plating process steps.
Elephantech: For a Greener Tomorrow
04/16/2025 | Marcy LaRont, PCB007 MagazineNobuhiko Okamoto is the global sales and marketing manager for Elephantech Inc., a Japanese startup with a vision to make electronics more sustainable. The company is developing a metal inkjet technology that can print directly on the substrate and then give it a copper thickness by plating. In this interview, he discusses this novel technology's environmental advantages, as well as its potential benefits for the PCB manufacturing and semiconductor packaging segments.
Trouble in Your Tank: Organic Addition Agents in Electrolytic Copper Plating
04/15/2025 | Michael Carano -- Column: Trouble in Your TankThere are numerous factors at play in the science of electroplating or, as most often called, electrolytic plating. One critical element is the use of organic addition agents and their role in copper plating. The function and use of these chemical compounds will be explored in more detail.
IDTechEx Highlights Recyclable Materials for PCBs
04/10/2025 | IDTechExConventional printed circuit board (PCB) manufacturing is wasteful, harmful to the environment and energy intensive. This can be mitigated by the implementation of new recyclable materials and technologies, which have the potential to revolutionize electronics manufacturing.