-
-
News
News Highlights
- Books
Featured Books
- smt007 Magazine
Latest Issues
Current IssueWhat's Your Sweet Spot?
Are you in a niche that’s growing or shrinking? Is it time to reassess and refocus? We spotlight companies thriving by redefining or reinforcing their niche. What are their insights?
Moving Forward With Confidence
In this issue, we focus on sales and quoting, workforce training, new IPC leadership in the U.S. and Canada, the effects of tariffs, CFX standards, and much more—all designed to provide perspective as you move through the cloud bank of today's shifting economic market.
Intelligent Test and Inspection
Are you ready to explore the cutting-edge advancements shaping the electronics manufacturing industry? The May 2025 issue of SMT007 Magazine is packed with insights, innovations, and expert perspectives that you won’t want to miss.
- Articles
- Columns
- Links
- Media kit
||| MENU - smt007 Magazine
Emerald EMS Enhances Efficiency, Performance with IDENTCO Label Feeder
July 11, 2023 | Emerald EMSEstimated reading time: 1 minute
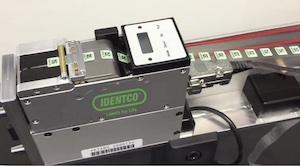
Emerald EMS, a renowned leader in electronics assembly, has taken a significant stride towards optimizing manufacturing operations at its Saline, MI location by acquiring the state-of-the-art IDENTCO ILP-45 Label Feeder through The Murray Percival Company. This strategic investment highlights Emerald’s commitment to exceeding customer expectations through cutting-edge technology and process enhancements.
The IDENTCO ILP-45 Label Feeder brings a range of benefits to their production line, including a remarkable reduction in operator manual labor, improved placement accuracy, accelerated labeling processes, and an overall increase in the output of finished PCBs. By integrating this advanced label feeder into its operations, Emerald EMS is poised to achieve new levels of efficiency and productivity.
As a customer-centric organization, Emerald EMS consistently strives to solve the most complex technical challenges while maintaining an unwavering commitment to flexibility. The company has built a reputation for assembling a passionate, talented, and technically-oriented team, resulting in successful partnerships with an array of remarkable clients.
The addition of the IDENTCO ILP-45 Label Feeder allows users to further optimize their investment in automation technologies. By automating the label placement process, the label feeder significantly reduces labor costs while ensuring maximum accuracy and efficiency. The seamless integration of the label feeder onto the existing pick-and-place equipment minimizes the need for additional floor space, making it a practical and space-efficient solution.
"The acquisition of the IDENTCO ILP-45 Label Feeder represents our unwavering dedication to providing superior manufacturing solutions to our clients," stated Randy Ferrell, Process Engineering Manager at Emerald EMS, Saline, MI. "By streamlining our labeling process, we anticipate a significant boost in productivity and operational excellence, ultimately delivering enhanced value to our customers. We appreciate our rep, The Murray Percival Company, for recognizing a need for this in our facility and bringing us a solution.”
IDENTCO, renowned for its industry expertise, has skillfully engineered the label feeder to exceed labeling requirements. When combined with the appropriate auto-apply labels, the IDENTCO ILP-45 Label Feeder ensures optimal performance, contributing to manufacturers' pursuit of operational perfection and data delivery control.
With features like maximum label placement accuracy, flexible solutions for circuit board applications, and low maintenance costs, the IDENTCO ILP-45 Label Feeder aligns seamlessly with Emerald EMS’ mission to offer trusted solutions for high-reliability and mission-critical products.
Suggested Items
July 2025 PCB007 Magazine: Sales—From Pitch to PO
07/18/2025 |Though all parts of a company are essential for holistic success, it is a foundational truth that a company lives and dies by its sales. If there are no sales, the company eventually ceases to exist, or as Henry Ford says, “Nothing happens until someone sells something.” In the July issue of PCB007 Magazine, we break down the sales stack and provide a guide to up your sales game.
Tightening of LPDDR4X Supply Drives Up Prices; Smartphone Brands to Accelerate Adoption of LPDDR5X
07/17/2025 | TrendForceTrendForce’s latest investigations reveal that major Korean and U.S. memory suppliers are expected to significantly reduce or even cease production of LPDDR4X in 2025 and 2026.
Beyond Design: Refining Design Constraints
07/17/2025 | Barry Olney -- Column: Beyond DesignBefore starting any project, it is crucial to develop a thorough plan that encompasses all essential requirements. This ensures that the final product not only aligns with the design concept but is also manufacturable, reliable, and meets performance expectations. High-speed PCB design requires us to not only push technological boundaries but also consider various factors related to higher frequencies, faster transition times, and increased bandwidths during the design process.
Knocking Down the Bone Pile: Addressing End-of-life Component Solderability Issues, Part 4
07/16/2025 | Nash Bell -- Column: Knocking Down the Bone PileIn 1983, the Department of Defense identified that over 40% of military electronic system failures in the field were electrical, with approximately 50% attributed to poor solder connections. Investigations revealed that plated finishes, typically nickel or tin, were porous and non-intermetallic.
Digital Twin Concept in Copper Electroplating Process Performance
07/11/2025 | Aga Franczak, Robrecht Belis, Elsyca N.V.PCB manufacturing involves transforming a design into a physical board while meeting specific requirements. Understanding these design specifications is crucial, as they directly impact the PCB's fabrication process, performance, and yield rate. One key design specification is copper thieving—the addition of “dummy” pads across the surface that are plated along with the features designed on the outer layers. The purpose of the process is to provide a uniform distribution of copper across the outer layers to make the plating current density and plating in the holes more uniform.