-
- News
- Books
Featured Books
- smt007 Magazine
Latest Issues
Current IssueMoving Forward With Confidence
In this issue, we focus on sales and quoting, workforce training, new IPC leadership in the U.S. and Canada, the effects of tariffs, CFX standards, and much more—all designed to provide perspective as you move through the cloud bank of today's shifting economic market.
Intelligent Test and Inspection
Are you ready to explore the cutting-edge advancements shaping the electronics manufacturing industry? The May 2025 issue of SMT007 Magazine is packed with insights, innovations, and expert perspectives that you won’t want to miss.
Do You Have X-ray Vision?
Has X-ray’s time finally come in electronics manufacturing? Join us in this issue of SMT007 Magazine, where we answer this question and others to bring more efficiency to your bottom line.
- Articles
- Columns
- Links
- Media kit
||| MENU - smt007 Magazine
Estimated reading time: 5 minutes
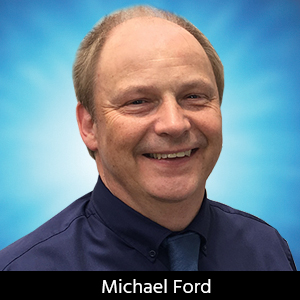
Smart Factory Insights: The Sustainability Gold Rush
A gold rush represents an opportunistic, get-rich-quick scheme. With just one or very few potential winners in each case, most participants are left disappointed with their share, especially when compared to how much effort they put in. These scenarios are usually not thought through very well, even by the winners. When it comes to sustainability in manufacturing, I’ve seen a gold rush of sorts to find solutions, but the pieces are disjointed and not uniform. Sustainability needs to be a forever thing—not a race to find gold, but rather a race to work together.
The simple discovery of a gold nugget in California on Jan. 24, 1848, started a movement of pioneers, each set on getting rich the quickest. Unfortunately, in the seven years that followed, as many as a hundred thousand people may have lost their lives in their quest for the gold. Masked by hopes of success, they ignored the risks. How many of us today find that risk to be attractive in our modern business plans?
In fact, modern gold rushes happen more frequently than we might imagine. Good examples would be the rush to dominate the videotape format, Industry 4.0, cloud computing, and blockchain. The opportunity to make money is a key driver for industry and the economy, as is the opportunity to save money. Sustainability, however, is quite an emotive subject because it brings sudden lifestyle changes into both business operations and society. We often implement urgent initiatives without fully thinking them through.
For example, finding discarded plastic bottles on beaches led to biodegradable plastics, without really considering the effects these new plastics themselves would have as they degrade. According to recent studies, we each consume a credit-card worth of plastic every week—the damage is done. The core problem has always been those who carelessly discard dangerous items, such as plastic bottles, disposable barbecues, and glass, rather than making the effort to recycle them. Everyone ends up paying a greater price due to the acts of careless individuals. Meanwhile, companies see this and meet the demand, provide solutions—and gain revenues. Unfortunately, they often just shift the problem rather than solve it, all at the customers’ expense.
Therefore, it is natural that companies feel powerless and frustrated with growing sustainability requirements. Demands are made on them to take responsibility, and openly collect and share data. There is a vast new level of reporting overhead to meet customer and government sustainability requirements at a time when there is no form, structure, or interoperability throughout the industry, nor even agreement on how things should be measured and presented. Groups of companies and organizations, usually within a narrow segment of their respective industries, are currently being driven to “go for gold,” creating whatever solutions they can to fulfill these sudden sustainability requirements. Companies then devise countless offset schemes to provide quick wins without really considering the impact of not really changing anything. They demand a high degree of pioneer-based investment for development and adoption, followed by a high cost of ongoing ownership and connectivity, with a high risk that their solutions will fall short of customer requirements, or exceed supplier capability. Manufacturers are currently left daunted with an unbearable cost and risk.
Providers of quick-and-dirty sustainability solutions are springing up everywhere to meet immediate needs, but are these really thought through? Almost every manufactured product has a complex supply network behind it—companies of all sizes creating and supplying materials from the most critical to the least significant. They can be based anywhere in the world and support a variety of customers and industry segments simultaneously. It is very unlikely that a small group of closely related entities will come up with solutions that are scalable, secure, and acceptable for those who currently are rightly very concerned about leakage of IP as well as privacy.
Learning from hindsight is a lazy excuse for not initially thinking things through, and for setting goals that are too short-term. Let’s envisage where we need to be for sustainability in a way that suits individual business needs, is interoperable with others, scalable, and sustainable. We need a mechanism for exchanging information that defines, discloses, and shares facts with shared universal definitions. They will be proofs of actions, events, measurements, results, or constituents, all exchanged in the form of signed digital certificates (credentials). There is, therefore, no need to expose any existing internal design, manufacturing, supply network, or other restricted business data.
This is the subject of IPC’s new sustainability standard. It’s the ability to automatically create declarations that satisfy all matters related to sustainability, as well as provenance, supply-network trust, traceability, and cybersecurity. It’s all included in one mechanism and fueled by the data that is already a part of the Smart manufacturing software we use today.
The best modern MES solutions, utilizing the IPC Connected Factory Exchange (CFX) standard, for example, are already capable of recording energy usage at any point in the factory. When this is combined with exact material traceability, enough information is available to enable the automated accumulation of material sustainability credentials against products, including all materials and manufacturing conditions. Manufacturing data in the digital domain is flexible enough to be formatted into whatever sustainability reports are required. Automating the required reporting and proof of conformance comes, therefore, with very little additional cost to the manufacturing operation. Substantial benefits are made in parallel as reduced wasted energy consumption helps reduce manufacturing costs significantly.
The greatest challenges and opportunities for manufacturing today involve sustainability. Having a pragmatic approach using existing tools in a collaborative, sustainable, standards-based ecosystem, in which an open market of sustainability credential solutions are appropriate to the scale of the manufacturing company, sector and material type, make them “plug and play.”
The idea for a “sustainability gold rush” may sound very exciting, until you realize it is your gold that companies are after. Better to think first and avoid the risk and waste of poorly thought-out solutions with limited scope. Please contact me or IPC if you are interested in understanding more about the collective approach.
This column originally appeared in the December 2023 issue of SMT007 Magazine.
More Columns from Smart Factory Insights
Smart Factory Insights: Making Rework a Smart Business OpportunitySmart Factory Insights: Today’s Manufacturing Jobs Require a New Skill Set
Smart Factory Insights: Compose Yourself, Mr. Ford
Smart Factory Insights: The Smart Business Case for Local PCB Manufacturing
Smart Factory Insights: Manufacturing Digital Twin—Spanners in the Works
Smart Factory Insights: Machines, People, and AI
Smart Factory Insights: Is Sustainability in Manufacturing a Benefit or Burden?
Smart Factory Insights: Manufacturing Meets the Flintstones