-
- News
- Books
Featured Books
- design007 Magazine
Latest Issues
Current IssueProper Floor Planning
Floor planning decisions can make or break performance, manufacturability, and timelines. This month’s contributors weigh in with their best practices for proper floor planning and specific strategies to get it right.
Showing Some Constraint
A strong design constraint strategy carefully balances a wide range of electrical and manufacturing trade-offs. This month, we explore the key requirements, common challenges, and best practices behind building an effective constraint strategy.
All About That Route
Most designers favor manual routing, but today's interactive autorouters may be changing designers' minds by allowing users more direct control. In this issue, our expert contributors discuss a variety of manual and autorouting strategies.
- Articles
- Columns
- Links
- Media kit
||| MENU - design007 Magazine
Hidden (and Obvious) Design Mishaps With Big Cost Impacts
August 14, 2024 | Jen Kolar, Monsoon SolutionsEstimated reading time: 2 minutes
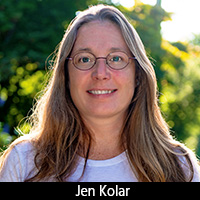
At Monsoon Solutions, we provide PCB layout services for the full lifecycle of products, from one-off prototypes to items manufactured in production volume. We also manage manufacturing and assembly for prototype and smaller production runs for both customer-produced and in-house layouts. As a result, we see various manufacturing data packages and work with many different manufacturers. I asked our PCB design engineers and program managers to share the cost adders and cost savers that designers can affect, and it was interesting to see that in addition to more technical responses, some of the biggest culprits were rather simple.
Fabrication Note Errors
Starting with PCB fabrication, one of the most obvious and simplest cost adders is incorrect or missing fabrication notes. As designers, we all like to have a starting point for a layout rather than having to start from scratch, and that often means starting from a similar board, which comes with existing fabrication notes. As a service bureau, we also often work on revisions of designs, and thus we inherit fabrication notes from the previous design. A common mistake I see from designers is when they leave notes the new designer doesn’t understand or know if they are required. I will often see them ask the customer about the notes, and it’s not uncommon for the customer to not know if they apply either. Rather than removing them, they commonly remain “just to be safe.” This often leads to extra processes like via fill, planarize, and plate. It may lead to building to Class 3 vs. Class 2 or extra testing and paperwork requirements. It may lead to adding hard gold vs. just ENIG. It may lead to ordering more exotic materials where standard FR-4 was fine. It also can lead to back-and-forth DFM questions as the fabricator must confirm what does or doesn’t apply, and with which offshore vendors can mean delays of multiple days.
Similarly, if there are no fabrication notes, the fabrication vendor is left guessing and may choose processes or materials that are more expensive or not absolutely needed, or they may miss important aspects of the design, like controlled impedances or that a specific thickness is needed for edge connectors. Make sure to review your notes for clarity and correctness before sending them to the fabrication shop. If you are unsure how to specify your requirements, talk to your fabricator.
To read the entire article, which originally appeared in the August 2024 Design007 Magazine, click here.
Testimonial
"Our marketing partnership with I-Connect007 is already delivering. Just a day after our press release went live, we received a direct inquiry about our updated products!"
Rachael Temple - AlltematedSuggested Items
Partnerships Drive Innovation for a Brighter Manufacturing Future
08/26/2025 | Barry Matties, I-Connect007When Schweitzer Engineering Laboratories (SEL) opened its greenfield facility in 2023, it did so with careful attention to choosing its suppliers. In this discussion, Collin Peters, electronics business director for North America at MKS’ Atotech, and Justin Kennedy, manager of engineering at SEL, explore their unique partnership that includes collaborative efforts to develop innovative solutions like the Uniplate® PLBCu6 line.
August 2025 PCB Magazine: Inventing the Future With SEL
08/18/2025 | I-Connect007 Editorial TeamTwo years after launching its state-of-the-art PCB facility, Schweitzer Engineering Laboratories shares lessons in vision, execution, and innovation, plus insights from industry icons and technology leaders shaping the future of PCB fabrication. The August 2025 issue of PCB007 Magazine takes you inside the facility to hear from its founder, Dr. Ed Schweitzer, its manufacturing team leaders, and several of the supplier vendors that make this a cutting-edge fabrication plant.
Global PCB Connections: Understanding the General Fabrication Process—A Designer’s Hidden Advantage
08/14/2025 | Markus Voeltz -- Column: Global PCB ConnectionsDesigners don’t need to become fabricators, but understanding the basics of PCB fabrication can save you time, money, and frustration. The more you understand what’s happening on the shop floor, the better you’ll be able to prevent downstream issues. As you move into more advanced designs like HDI, flex circuits, stacked vias, and embedded components, this foundational knowledge becomes even more critical. Remember: the fabricator is your partner.
Advint and Sayron Bring Advanced Rectifier Solutions to High-Reliability PCB Manufacturers
08/01/2025 | Advint IncorporatedAdvint Incorporated has partnered with Sayron, a leading global rectifier manufacturer, to supply cutting-edge IGBT-based DC rectifiers to high-performance PCB manufacturers across North America and beyond. Sayron’s precision-engineered rectifiers align with the stringent requirements of advanced PCB processes.
Direct Metallization: A Sustainable Shift in PCB Fabrication
07/31/2025 | Jim Watkowski, Harry Yang, and Mark Edwards, MacDermid Alpha Electronics SolutionsThe global electronics industry is undergoing a significant transformation, driven by the need for more resilient supply chains and environmentally sustainable manufacturing practices. Printed circuit boards (PCBs), the backbone of interconnection for electronic devices, are at the center of this shift. Traditionally, PCB fabrication has relied heavily on electroless copper, a process that, while effective, is resource-intensive and environmentally hazardous. In response, many manufacturers are turning to direct metallization technologies as a cleaner, more efficient alternative.