Estimated reading time: 3 minutes
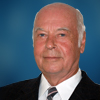
Contact Columnist Form
Karl's Tech Talk: Wafer Bumping Technology Choices
Editor's Note: This column originally appeared in the October 2011 issue of The PCB Magazine.
Tech Talk introduced the topic of wafer bumping some time ago (Tech Talk #170, CircuiTree Magazine, November 2009) with a short reflection on the history of wafer bumping, going back to IBM’s introduction of the C4 process (controlled-collapse chip connection). Bumping is done at the wafer-level, before chip singulation. As I/O count increased, wire-bonding of chips with peripheral array I/O patterns became more difficult and drove the technology of bumped area array I/Os.
The dominant bumping technologies are ball-drop, stencil printing and plating. Given these choices: How does one select the best and most cost-effective process for a given flip-chip type package? There are several considerations, most importantly pitch and desired stand-off height (i.e., the gap between the chip and the package top surface).
Figure 1 shows an overview of different bumping technologies options in relationship to bump pitch and bump height.
Figure 1: Bumping Technologies and Options by Bump Height and Pitch (courtesy: Dr. M. Toepper, IZM Fraunhofer Institut, Berlin, Germany)
As pitch becomes smaller, the technology moves from ball placement (which does not require photolithography) to stencil printing, which may employ a metal stencil or thick dry film photoresist, to electroplating which uses dry film photoresist, single-coating liquid photoresist or multiple coatings of liquid photoresist, depending on bump height requirements. As Figure 1 illustrates, there are pitch ranges where these technologies overlap.
When plated solder bumps are reflowed, the shape of the bump approaches that of a sphere. Thus, the volume of the plated solder will determine the bump height as well as the achievable pitch. As pitch goes down, so does stand-off height, a fact that may not be welcome because under-filling becomes more difficult and co-planarity requirements become more stringent. In case there is no reflow operation such as with gold bump plating for tape automated bonding (TAB) or chip-on-glass (COG) applications, very fine low-profile bumps are achieved (see Figure 1, lower left hand corner). An interesting new technology is the formation of bumps with copper pillars, capped with solder or tin (see Figure 2). The copper pillar is plated first, followed by solder plating. After resist stripping, the solder is reflowed whereby the shape of the plated solder changes from a flat disc to dome-shaped cap. Since the copper does not reflow, it retains its original pillar shape, allowing the formation of fine-pitch, high stand-off bumps. These copper columns give the package interconnection higher reliability because of the good compliance of copper under stress.
Figure 2: Copper Pillar with Solder Cap (source: Amkor Technology®)
Figure 3 shows an array of plated copper pillars with tin caps before resist stripping.
Figure 3. Copper Pillars with tin caps before resist stripping (Source: DuPont Electronics & Communication)
As shownin Figure 1, there are overlapping technologies in wafer bumping. This also applies to the use of liquid versus dry film photoresist, and the use of a single coat of liquid resist versus multiple coatings. A curious process has developed that stretches the ability of thin resist coatings to form relatively high solder bumps. The solder is deliberately over-plated, forming solder mushroom heads over the resist (“mushroom plating,” see Figure 4). After resist stripping and solder reflow, the mushroom reshapes into a solder sphere whose position on the UBM is defined by the developed resist pattern.
Figure 4: Mushroom plating of solder bumps (Source: DuPont Electronics & Communication)
It should be noted that for this technology, compatible photoresists and strippers have to be selected so that the stripped resist is in liquid form or very fine suspended particles to allow clean stripping under the over-plated metal.
As mentioned above, if solder paste is stenciled, one can use a metal stencil or a suitable dry film photoresist that is exposed and developed to form the openings that define the location of the stenciled solder paste. Since the solder paste needs to be partially reflowed before resist stripping to keep the stenciled paste in place during and after stripping, the resist needs to be rather thermally stable.
Karl Dietz is President of Karl Dietz Consulting LLC. He offers consulting services and tutorials in the field of circuit board and substrate fabrication technology. Reach Dietz at karldietz@earthlink.net or by phone at (001) 919-870-6230.
More Columns from Karl's Tech Talk
Karl's Tech Talk: Digital Imaging UpdateKarl’s Tech Talk: Electronic Packaging Levels
Green Legislation and the Impact on Electronic Materials and Processes
Digital Imaging Revisited
Dry Film Photoresist Thickness Selection Criteria
Quick-Turn Circuit Board Shops
Optical Interconnects
Signal Loss