-
- News
- Books
Featured Books
- pcb007 Magazine
Latest Issues
Current IssueInventing the Future with SEL
Two years after launching its state-of-the-art PCB facility, SEL shares lessons in vision, execution, and innovation, plus insights from industry icons and technology leaders shaping the future of PCB fabrication.
Sales: From Pitch to PO
From the first cold call to finally receiving that first purchase order, the July PCB007 Magazine breaks down some critical parts of the sales stack. To up your sales game, read on!
The Hole Truth: Via Integrity in an HDI World
From the drilled hole to registration across multiple sequential lamination cycles, to the quality of your copper plating, via reliability in an HDI world is becoming an ever-greater challenge. This month we look at “The Hole Truth,” from creating the “perfect” via to how you can assure via quality and reliability, the first time, every time.
- Articles
- Columns
- Links
- Media kit
||| MENU - pcb007 Magazine
Estimated reading time: 1 minute
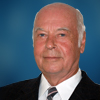
Contact Columnist Form
Quick-Turn Circuit Board Shops
Quick-turn circuit board shops specialize in the speedy delivery of small lots or prototype boards. Thus, they value any processing technique and technologies that reduce the time of the critical path between receiving the CAD data and shipping the finished boards. Some of the technologies that enable fast delivery are also suitable for mass production. The following are some examples of quick-turn processing.
Phototooling
The creation of a silver halide phototool involves a number of time-consuming steps such as plotting, development, fixing, drying, and equilibrating the phototool to the temperature and humidity of the working environment. Equilibration is particularly time-consuming.
Some quick-turn shops have tried to shortcut the equilibration step with limited success. The target dimensions of the phototool features are those of a damp phototool. Typically, the dryer temperature of the processor is set lower than normal so that the film exits the processor just a little damp and relatively cool. The film is measured within minutes after processing and sent directly to the imaging area. A film processed and used this way will slowly change size over the next several hours while it is in use, but when used quickly after processing and measuring, and if the tolerances are fairly forgiving, this approach can be viable in reducing overall processing time.
Digital Imaging
Laser direct imaging, or other digital imaging processes, has been first adopted by prototype and quick-turn shops for the obvious reason that they eliminate all phototool processing steps. The other big advantage of LDI is its ability to scale the image (i.e., change the dimensions slightly, for best fit to image features on another layer).
Direct Metallization Processes
Direct metallization processes allow copper plating in through-holes without having to go the lengthy electroless copper process. Direct metallization process uses either carbon, graphite, or palladium catalyst, or a conductive polymer to initiate copper electroplating on the dielectric hole wall. These processes avoid the use of problematic chemicals that are part of the electroless copper formulation; they use less water, typically have a smaller equipment footprint, and use fewer processing steps, which allow the quick-turn shop to reduce processing time. Table 1 compares a graphite-based direct metallization process with the sequence of steps that make up the electroless copper process.
Editor's Note: This article originally appeared in the May 2015 issue of The PCB Magazine.
More Columns from Karl's Tech Talk
Karl's Tech Talk: Digital Imaging UpdateKarl’s Tech Talk: Electronic Packaging Levels
Green Legislation and the Impact on Electronic Materials and Processes
Digital Imaging Revisited
Dry Film Photoresist Thickness Selection Criteria
Optical Interconnects
Signal Loss
Karl's Tech Talk: Miniaturization and Reliability