-
- News
- Books
Featured Books
- pcb007 Magazine
Latest Issues
Current IssueInventing the Future with SEL
Two years after launching its state-of-the-art PCB facility, SEL shares lessons in vision, execution, and innovation, plus insights from industry icons and technology leaders shaping the future of PCB fabrication.
Sales: From Pitch to PO
From the first cold call to finally receiving that first purchase order, the July PCB007 Magazine breaks down some critical parts of the sales stack. To up your sales game, read on!
The Hole Truth: Via Integrity in an HDI World
From the drilled hole to registration across multiple sequential lamination cycles, to the quality of your copper plating, via reliability in an HDI world is becoming an ever-greater challenge. This month we look at “The Hole Truth,” from creating the “perfect” via to how you can assure via quality and reliability, the first time, every time.
- Articles
- Columns
- Links
- Media kit
||| MENU - pcb007 Magazine
Estimated reading time: 2 minutes
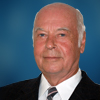
Contact Columnist Form
Optical Interconnects
When we hear of optical interconnects or optical signal transmission, we think of the long-distance signal transmission through glass fibers, the conversion of ocean floor cables to glass fibers, and the establishment of glass fiber transmission lines between cities in the late 1990s, followed by intra-city glass fiber lines and glass fiber networks that connect buildings.
Then, chip-to-chip optical interconnects were explored, and when data rate transmissions in backplanes pushed beyond 10Gbits/sec, the limitations of conversional signal transmission through copper over 500 mm line length, and beyond, became apparent, especially with conventional, affordable dielectric material platforms. Signal attenuation and signal shape distortion became unavoidable, even with differential signaling and back-drilling of metalized through-holes. Optical backplanes hold the promise of avoiding these problems. There are practically no transmission losses and no electromagnetic interferences, and the capacity to transmit an enormous amount of data is unsurpassed.
Optical transmission can be through optical fibers, waveguides, or through air, or a combination thereof. However, the cost of the optoelectronic components and the cost of precision mounting has been a major hurdle to moving to optical backplanes.
Lucent looked at the development of optical backplanes in the early 2000s, but financial problems interfered. Of particular interest were organic waveguides based on dry film photoresist technology such as DuPont’s Polyguide. UV exposure changes the optical properties of the waveguide from the surrounding unexposed material. The material base for such waveguides was acrylate chemistry, which limited the transmission distances because of the lossy material and was limited to a transmission mode called multimode. The use of lower-loss photosensitive fluorinated polyimides was technically feasible but costly and raised concerns about the toxicity of the chemicals.
Waveguides come in a variety of material constructions: organics, glass, silica, silicon, etc. The properties that are important to the performance of waveguides include:
- Intrinsic absorption loss
- Low optical scattering loss
- Low waveguide fabrication loss
- High thermal stability
- Environmental stability
- Precise control of refractive index
- Low birefringence
- Mechanical toughness
Before waveguides were considered for optoelectronic integration into PWBs, notably backplanes, they could be found in wafer-scale packaging. A polymer cladding is typically applied onto either silica or silicon wafer supports using spin coating technology. Good coating uniformity and precision is achieved with this process over the surface of the wafer. Then a guide polymer of a higher refractive index than the cladding is spun on and patterned either by virtue of its own photosensitivity or with a layer of photoresist, sometimes over a metal mask. The thicknesses of the waveguide layer are in the range of 5–60 microns. The waveguide pattern is then formed by etch-back, usually by plasma, but sometimes by solvent. Then a final layer of cladding is spun on and the wafer is complete. It is diced, connected to fibers, mounted on a support such as glass or ceramic, perhaps on a heater or thermoelectric cooler, placed in a package and electrically connected.
Editor's Note: This article originally appeared in the March issue of The PCB Magazine.
For more about Optical Interconnects: Read our interview with TTM's Marika Immonen.
More Columns from Karl's Tech Talk
Karl's Tech Talk: Digital Imaging UpdateKarl’s Tech Talk: Electronic Packaging Levels
Green Legislation and the Impact on Electronic Materials and Processes
Digital Imaging Revisited
Dry Film Photoresist Thickness Selection Criteria
Quick-Turn Circuit Board Shops
Signal Loss
Karl's Tech Talk: Miniaturization and Reliability