-
- News
- Books
Featured Books
- pcb007 Magazine
Latest Issues
Current IssueInventing the Future with SEL
Two years after launching its state-of-the-art PCB facility, SEL shares lessons in vision, execution, and innovation, plus insights from industry icons and technology leaders shaping the future of PCB fabrication.
Sales: From Pitch to PO
From the first cold call to finally receiving that first purchase order, the July PCB007 Magazine breaks down some critical parts of the sales stack. To up your sales game, read on!
The Hole Truth: Via Integrity in an HDI World
From the drilled hole to registration across multiple sequential lamination cycles, to the quality of your copper plating, via reliability in an HDI world is becoming an ever-greater challenge. This month we look at “The Hole Truth,” from creating the “perfect” via to how you can assure via quality and reliability, the first time, every time.
- Articles
- Columns
- Links
- Media kit
||| MENU - pcb007 Magazine
Estimated reading time: 1 minute
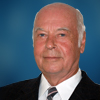
Contact Columnist Form
Karl's Tech Talk: Digital Imaging Update
Through the years, I have repeatedly covered and updated digital imaging in this column, from as far back as 1997 in CircuiTree, through a column in this magazine in November 2015. Several reasons for this extended coverage include the fact that technology had a slow, long incubation time that eventually led to accelerated improvements and acceptance for mass production. It might also be argued that, next to the development of microvia technologies, digital imaging is probably the most innovative technology to achieve high-density interconnects in acceptable yields.
It is worth mentioning that digital imaging is a more appropriate term to refer to this technology than laser direct imaging (LDI) because LDI is just one example of digital imaging, albeit its pioneering version.
The advantages of digital circuitization techniques have been described in detail by suppliers of equipment and photoresist. Since phototool generation and conditioning are omitted, there is the advantage of shorter lead time. Small lots can be customized at no extra cost (e.g., with added date and lot number information). Maybe the biggest advantage is the ability to scale (i.e., to change the dimension of each individual exposure for best fit to reference points on an underlying pattern of a multilayer structure). However, early digital imaging systems had substantial drawbacks, such as Orbotech’s DP100 which used an argon ion laser with limited radiation power, high power usage, and high cooling requirements.
For years, laser direct imaging (LDI) was synonymous with digital imaging. While most early, commercially successful digital processes involved the use of lasers, other more recent processes use non-laser light sources such as LEDs (light emitting diodes) that consume less power, last longer, and have higher light intensity output. Alternatively, various types of mercury lamps are employed, with more than one wavelength used for imaging. Others use inkjet technology to build digitally imaged patterns such as legend print, soldermask or etch resist.
Editor's Note: This article originally appeared in the July 2016 issue of The PCB Magazine.
More Columns from Karl's Tech Talk
Karl’s Tech Talk: Electronic Packaging LevelsGreen Legislation and the Impact on Electronic Materials and Processes
Digital Imaging Revisited
Dry Film Photoresist Thickness Selection Criteria
Quick-Turn Circuit Board Shops
Optical Interconnects
Signal Loss
Karl's Tech Talk: Miniaturization and Reliability