Estimated reading time: 6 minutes
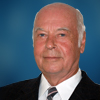
Contact Columnist Form
Karl's Tech Talk: Copper Surface Preparation for Dry Film Lamination, Part A
Editor's Note: This article originally appeared in the May 2012 issue of The PCB Magazine.
Introduction
This column represents the first in a five-part series that will revisit and update the topic of copper surface preparation for dry film lamination. The series will include the following topics:
- Copper topography and dry film conformation;
- Characterizing the copper topography and establishing topography specifications;
- Dry film adhesion to the copper surface, understanding the chemical interactions at the copper and resist surfaces;
- Characterizing the copper surface chemistry and establishing criteria for acceptable surfaces based on empirical adhesion tests; and
- A summary of copper surface preparation processes, their advantages and limitations.
It is understood that there are a number of other surface preparation operations in PCB fabrication that will not be covered here. These include the preparation of innerlayer copper circuits with a multilayer bonder coating, the desmear preparation of the hole wall prior to the electroless copper process step sequence, and possibly the preparation of the outerlayer copper circuit pattern for the so-called “soldermask over bare copper” application. In a broader sense, the beveling of the board edges can be viewed as surface preparation, and so can be the de-burring step after through-hole drilling. As such, these two operations will not be covered here.
Background
For copper-to-dry-film adhesion forces to take effect, there first has be good contact, i.e., conformation, of the dry film with the copper surface. It would be easiest for the film to conform to a smooth copper surface, however, such a smooth surface is not desirable. An optimal surface roughness is required to multiply the anchoring points for the weak chemical interactions between dry film and copper and to provide mechanical interlocking to resist lateral shear. Yet, too much roughness is not beneficial since under the limitations of resist flow, resist thickness, lamination time, pressure and temperature, the film will not conform to a surface that is too rough.
It is useful to review the failure modes due to insufficient dry film adhesion as well as excessive adhesion in the various processes (Figure 1).
Figure 1: Failure modes.
There are several potential failure modes, or sources of yield losses, if the copper surface is not properly prepared:
- Failure to achieve good adhesion in a print-and-etch (P/E) process will cause etchant attack under the resist and ultimately an “open” defect.
- Failure to achieve good adhesion in a plating process will cause tin/lead underplating, ultimately leading to “shorting” defects (“shorts”).
- Failure to achieve good release of unexposed resist during development can cause etch retardation in a print-and-etch process, ultimately leading to shorts.
- Failure to achieve good release of unexposed resist during development in a plating process can cause poor adhesion of the plated copper to the copper base (“copper-copper peelers”).
- Failure to achieve good release of exposed resist in a print-and-etch process on innerlayers can inhibit the formation of copper oxide multilayer bonder (or alternative bonders) on such a copper surface.
- Failure to achieve good release of exposed resist in a plating process can cause etch retardation.
To understand the various aspects of the copper topography, it will be useful to become familiar with laminate (base material, or CCL) structures and copper types.
Rigid laminate is typically reinforced by woven glass. Copper clad laminate, as received from the laminate manufacturer, has waviness in the surface which means the copper foil contours the weave pattern of the glass cloth in the resin (Figure 2). The waviness is more or less pronounced depending on the resin contents of the dielectric, the coarseness of the glass fibers and the weave pattern. Even after electroless and electrolytic copper plating, this waviness pattern may still be noticeable to some extent. All surface structuring that we achieve in surface preparation is actually a microstructure superimposed on the primary waviness pattern. The waviness pattern typically shows peak-to-peak distances varying from 0.5 to 1.0 mm (20 to 40 mil) and peak-to-valley heights (Wt) ranging from 0.75 to 7.0 microns (30 to 280 microinches). Specialty laminates may have filler and no glass weave, or a non-woven reinforcement. Flex substrates are not reinforced.
Figure 2: Laminate weave pattern.
The most common copper foil used in CCL manufacture is the ED foil (electrodeposited foil). Figure 3 shows a schematic of the ED (electrodeposited) copper foil process. One can picture the equipment as a large plating bath, filled with a solution of copper sulfate and a cathode in the form of a slowly revolving titanium drum onto which the copper plates-out in a film, or foil. Rotation speed determines the plating time. Rotation speed and current density determine the ultimate thickness of the foil. The copper foil is peeled off and rolled up. The drum side is the smoother copper side. The rougher side of the foil is the one that faced the plating solution. It is the smoother drum side that is typically on the outside of the CCL and faces the dry film in lamination. This surface of the ED copper is also referred to as standard vendor copper. The rough side is “treated” for better adhesion to the resin of the dielectric core between the copper foils. If the rough copper side is on the outside of the CCL, this construction is referred to as “reverse treated foil.” Other sources of copper foils (or cladding) are RA copper (rolled annealed) which is often used in flex circuits, and in rare cases, the copper layer may have been formed directly on the dielectric surface by sputtering (or electroless plating) a seed layer that is then electroplated up to the desired thickness.
Figure 3: Schematic of the ED manufacturing process.
Figure 4 compares the relatively smooth standard vendor copper foil with reverse-treated foil (RTF), which looks much rougher. In the case of RTF, the rough side of the foil faces the outside. This type of construction is popular for innerlayers. The only surface preparation is typically diluted acid to remove chromate and oxides, followed by rinsing and drying.
Figure 4: Comparison of reverse treated foil and standard vendor copper.
Figure 5 compares standard vendor copper foil with so called “double-treated” foil. One can see the fine micro-roughness of the double-treated surface, which yields good dry film adhesion. The foil is more expensive than standard foil because it has a zinc or brass treatment on both sides, as the name suggests. Such a surface typically does not require a surface preparation process. Some films may adhere too much to this surface, so compatibility needs to be checked. The surface is known to scoff easily, i.e., the fine structure is easily mechanically damaged. AOI equipment may have to be adjusted to read this surface correctly.
Figure 5: Comparison of double-treated foil and standard vendor copper.
Figure 6 compares standard vendor foil with electroplated copper as we see it on panel-plated boards. This surface is very smooth due to grain refining (brightener) additives in the plating bath. So the surface preparation method has to roughen the copper for better dry film adhesion. Since the electroplating process may cause the formation of so called copper nodules on the surface that detrimentally affect the tenting process, a de-noduling step may be included in the surface preparation, a process typically performed with special ceramic brushes.
Figure 6: Comparison of electroplated surface and standard (ED) vendor foil.
Karl Dietz is president of Karl Dietz Consulting LLC. He is offering consulting services and tutorials in the field of circuit board and substrate fabrication technology. Dietz may be reached by e-mail at karldietz@earthlink.net or phone at (001) 919-870-6230.
More Columns from Karl's Tech Talk
Karl's Tech Talk: Digital Imaging UpdateKarl’s Tech Talk: Electronic Packaging Levels
Green Legislation and the Impact on Electronic Materials and Processes
Digital Imaging Revisited
Dry Film Photoresist Thickness Selection Criteria
Quick-Turn Circuit Board Shops
Optical Interconnects
Signal Loss