Estimated reading time: 3 minutes
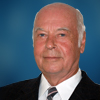
Contact Columnist Form
Karl's Tech Talk: Screen Printing Applications, Part I
Several screen printing applications are used in the fabrication and assembly of PCBs and electronic packages and devices. They include:
- Screen printing of non-photoimageable, UV-curable, or thermo-curable ink through a screen that has been patterned with a photosensitive emulsion. The ink can be screened onto single-sided copper-clad laminate for print and etch circuitization or as a plating resist for double-sided and multilayer boards, or as a soldermask.
- Screen printing of photoimageable liquid soldermask onto finished circuit boards. This operation can be double-sided in a vertical mode, or single-sided in a horizontal mode.
- Application of “legend print,” typically by screen printing, but more recently by inkjetting, after soldermask application, so called “legend print” is applied. This white lettering on top of the usually green soldermask coating may contain information regarding lot numbers, date of manufacture, position markings for component mounting, component type, etc.
- Application of solder paste by screen or stencil printing in assembly; i.e., the mounting of active and passive components onto the board through solder joint connections.
- B2it process, which includes multiple screen printing steps forming cone-shaped bumps with silver paste that serve as Z-axis interconnects in a coreless microvia HDI package.
- Screen printing of conductors and via fill with thick film conductive pastes on LTCCs (low temperature co-fired ceramics).
- Screen or stencil printing of conductive or non-conductive via fills in PCBs.
- Screen printing of silver paste conductors on solar cells.
- Screen printing of embedded capacitor and resistor structures in PCBs, modules and substrates.
All of these printing steps must be able to handle the customary board formats, with the exception of solder paste printing, which may be performed after the board has been broken up into smaller patterns that were possibly repeated two, four, or six times (2-up, 4-up, and 6-up format) on the board. This process is called singulation. Thus, for solder paste printing, the original board size is the largest that is handled. More often, solder paste printing is done after singulation with half-size, one-quarter-size, or one-sixth-size formats.
The smallest board size is typically 12 x 12 inch. The reason some boards are processed in such small formats has to do with the difficulty of achieving good registration and fine line resolution on larger formats. Other common formats are 12 x 18, 18 x 24, and 20 x 24 inch, whereby 18 x 24 inch is by far the most common. Boards typically travel through the various processing modules with the longer size in machine direction (and the smaller side in transverse direction), which means that for an 18 x 24 inch board the squeegee stroke length of a screen printer would be 24 inches.The screen is typically patterned with a polyvinyl acetate or polyvinyl alcohol-based photosensitive emulsion. The emulsion is coated onto the screen mesh, dried, exposed through a phototool, and developed. Alternatively, the emulsion pattern can be formed on a support sheet and subsequently transferred to the screen.
The substrate is placed under the screen frame, ink is applied on top of the patterned screen, and a squeegee then pushes the ink through the openings of the screen. Several types of squeegee profiles and materials are in use and the proper selection will depend on the application. A diamond-cut profile squeegee is fairly rigid and is sensitive to the screen printer settings, especially the required “parallelism.” This type of squeegee is used for high resolution patterns in small formats. A rectangular or flexible squeegee is less sensitive to printer settings and is used for high-speed printing of large patterns. A dual or triple composite durometer squeegee is a reasonable compromise to pattern large areas with good resolution. The harder durometer composite backs up the softer layer, or in the case of triple composite, is sandwiched between two softer layers.
The following table is a glossary of terms used in screen printing (Source: DuPont):
The next Tech Talk, “Screen Printing Application in Electronics, Part II" will look at a few of these applications in more detail.
Karl Dietz is president of Karl Dietz Consulting, LLC, which offers consulting services and tutorials in the field of circuit board and substrate fabrication technology. Dietz may be reached by e-mail at karldietz@earthlink.net or phone (001) 919-870-6230.Editor's Note: This article originally appeared in the January 2013 issue of The PCB Magazine.
More Columns from Karl's Tech Talk
Karl's Tech Talk: Digital Imaging UpdateKarl’s Tech Talk: Electronic Packaging Levels
Green Legislation and the Impact on Electronic Materials and Processes
Digital Imaging Revisited
Dry Film Photoresist Thickness Selection Criteria
Quick-Turn Circuit Board Shops
Optical Interconnects
Signal Loss