-
- News
- Books
Featured Books
- design007 Magazine
Latest Issues
Current IssueShowing Some Constraint
A strong design constraint strategy carefully balances a wide range of electrical and manufacturing trade-offs. This month, we explore the key requirements, common challenges, and best practices behind building an effective constraint strategy.
All About That Route
Most designers favor manual routing, but today's interactive autorouters may be changing designers' minds by allowing users more direct control. In this issue, our expert contributors discuss a variety of manual and autorouting strategies.
Creating the Ideal Data Package
Why is it so difficult to create the ideal data package? Many of these simple errors can be alleviated by paying attention to detail—and knowing what issues to look out for. So, this month, our experts weigh in on the best practices for creating the ideal design data package for your design.
- Articles
- Columns
- Links
- Media kit
||| MENU - design007 Magazine
Estimated reading time: 8 minutes
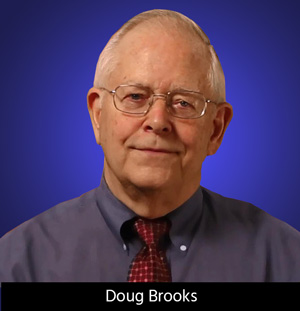
Contact Columnist Form
Trace Currents and Temperature, Part 1: The Basic Model
This column originally appeared in the November 2012 issue of The PCB Design Magazine.
This first of a four-part series on trace currents and temperature covers the role of resistance and then formulates a basic model for analysis. Subsequent parts will explore various results that have been empirically obtained, how we can use the melting temperature of a trace to our advantage, and how to deal with vias.
Role of Resistance
Traces heat up (increase temperature) because of power dissipation within the trace itself. If no current flows, there is no heating. If current does flow, then the power dissipated in the trace is equal to i2R, where i is the current down the trace and R is the resistance of the conductor.
In my column “What Is Current And Why Do We Care,” I provide the fundamental definition in electronics: Current is the flow of electrons. I develop that definition in that column and in more detail in an article on our website[1]. Individual electrons really flow very slowly down a copper conductor. More accurately, they jump from one atom to another, displacing an electron in that atom. That electron then jumps to another atom, displacing an electron in that atom, and so on. The individual electrons do not travel at the speed of light, but the displacement of electrons from one atom to another does progress at the speed of light.
Heat (or temperature) is movement[2]. As the temperature of a material increases, atomic and molecular motion within that material speeds up. In particular, there is random motion at the electron level, which also speeds up with temperature. This results in random collisions between electrons in conductors. If we try to push a signal down a conductor with many such collisions going on, we must overcome (at least to some extent) the effects of the collisions. We do that with a force that, in our world, equates to voltage. It is the effect of these collisions, impeding the flow of the electrons, that we call resistance.
The resistance that a signal sees as it propagates down a conductor is primarily the result of these collisions. There are fewer collisions at lower temperatures than at higher temperatures, and therefore the resistance of a conductor is smaller at lower temperatures and increases with temperature. The number of available electrons for current flow increases with cross-sectional area, making it easier for a signal to find a path through the collisions (i.e., there are more paths available with bigger cross-sectional areas). Therefore, as a general rule, the resistance of a conductor decreases with increasing cross-sectional area and increases with increasing temperature.
So as we pass a signal down a conductor, a small amount of the energy in the signal is dissipated within the conductor as power dissipation: i2R. It is this power dissipation that heats up the conductor. There is generally higher energy lost at higher temperatures, and lower energy lost with larger conductors (i.e., those with larger cross-sectional areas).
Resistivity
The characteristic of a material that reflects its electrical resistance is a property called resistivity. All materials have resistivity and there are numerous tables in printed media and on the Web that provide resistivity information for various materials. Silver, copper, and gold, respectively, have the lowest resistivity of all elements. It is typically given by the values:
Silver 1.6x10-8 ohm*mCopper 1.7x10-8 ohm*mGold 2.2x10-8 ohm*m
Note: Units are ohm-meters.
Since resistivity increases with temperature (see discussion above), electrical resistivity must be specified at a particular temperature. This is usually specified as ambient, or room temperature, at 20oC.
As noted, the units of resistivity are ohms-length. If we divide resistivity by the cross-sectional area of a conductor, we get units of:
Ohms-length/area = ohms/unit length.
Now, if we multiply that by the length of the conductor, the units become:
Ohms/unit length X length = ohms (or, simply, resistance).
So, the standard formula for the resistance of a conductor, based on its resistivity, is[3]:
[Eq. 1] R = (ρ/A) * L
Where:
ρ (rho) is the resistivity of the conductorA is the cross-sectional area of the conductorL is the length of the conductor.
And since resistivity is given relative to a specific temperature, then the resistance of a trace calculated with Equation 1 applies at a specific temperature.
Thermal Coefficient of Resistivity
The thermal coefficient of resistivity is usually represented by the symbol alpha, α. It is the factor that resistance increases with increasing temperature. Its usage is shown in Equation 2. Take the resistance of a conductor at some reference temperature (usually, but not necessarily 20oC) and multiply it by one plus alpha, times the change in temperature from the reference:
[Eq. 2] R = Rref(1+ α*ΔT)
Where:
R = Resistance at the desired temperatureRref = Resistance at the reference temperatureα = thermal coefficient of resistivity, andΔT = desired temperature – reference temperature (oC).
The thermal coefficient of resistivity for silver, copper, and gold is[4]:
Silver 0.003819 per degree CCopper 0.004041 per degree CGold 0.003715 per degree C
The thermal coefficient of resistivity is very roughly 0.4% per degree C.
Resistance of Copper Wires and Traces
The resistance of copper wires of arbitrary size is readily available in standard texts and Web pages. The standard table of resistance is usually based on the American Wire Gauge table which itself is based on what was known as the Brown and Sharpe Wire Gauge table first formulated in 1857[5]. While these types of tables readily equate resistance and wire size for some 44 different wire sizes (gauges) they are not particularly useful for determining resistance vs. size for PCB traces. UltraCAD has created a freeware calculator for conveniently converting between trace size and wire gauge, available on our website[6].
An illustration of this calculator is shown in Figure 1.
Figure 1: UltraCAD’s Wire Gauge Calculator, v3.
The top portion of the calculator allows the user to enter any two of three parameters (wire gauge, trace thickness, and trace width) and solve for the third. Then if the user enters a trace length and a specific environmental temperature, the calculator will solve for the trace resistance at that temperature. Finally, if the user enters the current flowing down the trace, the calculator provides the voltage drop across the trace (a simple Ohm’s Law calculation).
Model for Trace Temperatures
We now have everything we need to develop a model for trace current/temperature relationships. Such a model is shown in Figure 2.
Figure 2: Model for trace current/temperature effects.
Figure 2 illustrates a trace on a substrate. The trace is subjected to heating as a result of the power dissipated in the trace (i.e., the i2R loss). The trace will cool as a result of conduction and convection. A stable temperature is reached when the heating effect and the cooling effect are equal and cancel.
Therefore, we can start with the idea that the change in temperature (of the trace) is proportional to i2R, or:
[Eq. 3]
Since R is inversely proportional to the area, A, we can rewrite this as:
[Eq. 4]
And rearranging terms leads to:
[Eq. 5]
[Eq. 6]
[Eq. 7]
Note that each successive equation (Equations 6 and 7) gets progressively more general.
There are two reasons for the more general equation. The first is that the area of the trace is involved in both the heating of the trace and the cooling of the trace. Therefore, one would expect it to have a different exponent than the ΔT term. The other reason for a more general approach is because the resistivity changes with temperature. Assume the only important factor is power dissipation. Then it would intuitively seem that 0.5 would be the correct exponent for ΔT. But as the trace heats up the resistivity changes. Therefore, for a given current, there is more heating at higher temperatures than there is at lower temperatures. Consequently, we would expect the exponent of ΔT to be slightly different from 0.5.
In an article in 1997, McHardy and Gandhi[7] attempted to fit Equation 7 to the original IPC data we all know and love; more on that in Part 2 of this series. They concluded that the form factor of a trace may be important in the relationship. That is, the temperature rise may be different for a wide, relatively skinny trace than it would be for a narrow, thicker one of the same cross-sectional area. This would be because a wider trace may cool better than a narrow trace would. Thermal stability would occur when the heating of the trace (caused by i2R) equaled the cooling of the trace (related to the surface area, or more directly to the width, W). We may be able to improve the model in Equation 7, therefore, by looking at the form factor of the trace (i.e., the width and the thickness) instead of just the cross-sectional area. We can modify the model in Equation 7 to adjust for this by breaking the area term into its width and thickness components, as in Equation 8:
[Eq. 8]
Equation 8, then, becomes an appropriate model for investigation of the relationship between trace currents and trace temperatures. We will look at some empirical results of this model in Part 2 of this series.
References
- For a more extensive discussion of current and its relationship to Maxwell’s Equations, see my article “What is This Thing Called "Current: Electrons, Displacement, Light, or What?”
- For example, the definition of absolute zero temperature is when ALL motion at the atomic level stops.
- It is really easy to mix up units when using this formula. Make sure that resistivity, area, and length are all expressed in the same length units or errors will result!
- The thermal coefficient of resistivity is very sensitive to a particular alloy. Therefore different sources may give different values, based on different alloy assumptions.
- For a good discussion of this, as well as a complete table, visit Wikipedia.
- See www.ultracad.com.
- “Empirical Equation for Sizing PWB Traces,” John McHardy, Mahendra Gandhi. Presented at IPC Works ’97 October 5 - 9, 1997, IPC Technical Paper S06-2
Douglas Brooks has an MS/EE from Stanford University and a Ph.D. from the University of Washington. He has spent most of his career in the electronics industry in positions of engineering, marketing, general management, and as CEO of several companies. He has owned UltraCAD Design Inc. since 1992. He is the author of numerous articles in several disciplines, and has written articles and given seminars all over the world on signal integrity issues since founding UltraCAD. His book, Printed Circuit Board Design and Signal Integrity Issues was published by Prentice Hall in 2003. Visit his website at www.ultracad.com.
More Columns from Brooks' Bits
Brooks' Bits: Internal Trace Temperatures—More Complicated Than You ThinkBrooks' Bits: Electromagnetic Fields, Part 3 - How They Impact Coupling
Brooks' Bits: Electromagnetic Fields, Part 2: How They Impact Propagation Speed
Brooks' Bits: How Electromagnetic Fields Determine Impedance, Part 1
Trace Currents and Temperature, Part 4: Via Heat
Trace Currents and Temperature, Part 3: Fusing Currents
The Skinny on Skin Effect, Part 3: Crossover Frequency
Brooks' Bits: The Skinny on Skin Effect, Part 2