Estimated reading time: 4 minutes
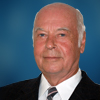
Contact Columnist Form
Karl's Tech Talk: Screen Printing Applications, Part II
Several screen printing applications are used in the fabrication and assembly of printed circuit boards and electronic packages and devices:
- Screen printing of non-photo-imageable, UV-curable or thermo-curable ink through a screen that has been patterned with a photosensitive emulsion. The ink can be screened onto single-sided copper-clad laminate for print and etch circuitization, or as a plating resist for double-sided and multi-layer boards, or as a soldermask.
- Screen printing of photo-imageable liquid soldermask onto finished circuit boards. This operation can be double-sided in a vertical mode, or single-sided in a horizontal mode.
- After soldermask application, so-called legend print is applied, typically by screen printing, more recently also by inkjetting. This white lettering on top of the typically green soldermask coating may contain information regarding lot numbers, date of manufacture, position markings for component mounting, component type, etc.
- In assembly, i.e., the mounting of active and passive components onto the board through solder joint connections, solder paste can be applied by screen or stencil printing.
- B2it process: multiple screen printing steps form cone-shape bumps with silver paste that serve as Z-axis interconnects in a coreless microvia HDI package.
- Screen printing of conductors and via fill with thick film conductive pastes on LTCCs (low temperature, co-fired ceramics).
- Screen or stencil printing of conductive or non-conductive via fills in PCBs.
- Screen printing of silver paste conductors on solar cells.
- Screen printing of embedded capacitor and resistor structures in PCBs, modules and substrates
Let’s take a closer look at screen printing of soldermask and legend print.
Soldermask
Historically, soldermask was a non-photoimageable ink that needed to be patterned onto the circuit board through a coated with a photosensitive emulsion exposed through a phototool and then developed. The soldermask ink was then squeegeed onto the board through the open areas of the screen, dried and cured. With the advent of the photoimageable, liquid-soldermask inks, the process changed. The ink was either applied by curtain coating, sequentially from both sides, or spray coated, or screen printed simultaneously from both sides. The screen coater was typically a double-sided, vertical blank (or flood) screen printer (Figure 1) that applied the soldermask ink in the desired uniform thickness, covering the entire board. Imaging followed in a photolithographic step, followed by development and curing. The most popular soldermask inks are two-component epoxy formulations, a resin and a curing agent, that are mixed before screen printing. After mixing, the ink has a limited shelf life. Curtain coating of soldermask ink was dominant in the early to mid-1980s and is still common in Europe, but not in the U.S. where screen printing is the norm. In Asia, we see all three application methods.
Screen printing of solder ink requires less solvent (thinner) than spray coating or curtain coating. Typical thinners for spray or curtain coating are propyleneglycol monomethylether acetate or propyleneglycol monomethyl ether (PM). There is a small amount of solvent in the resin, as supplied. Such solvents are typically carbitol acetate or dipropyleneglycol monomethylether. Development of screen printed soldermask inks is typically aqueous, i.e., an aqueous sodium carbonate solution, whereas curtain-coated inks may require a solvent such as butyrolactone. To clean the screens after printing, one used to employ chlorinated hydrocarbons, but that process has now switched to water-miscible solvents based on glycol ethers or acetates.
Figure 1: Vertical, double-sided soldermask screen printer. (source: Circuit Automation)
Legend Print
Legend refers to printed information, typically in white, on top of the typically green soldermask. The legend may contain information regarding lot numbers, date of manufacture, position markings for component mounting, component type, etc. Military PCBs typically specify epoxy-based ink formulations. There has been an ongoing debate about the need for legend print, but this has not changed the reality that it is still alive and well. Most legend is screen printed with non-photoimageable inks, i.e., they require a patterned screen. Figure 2 outlines the rather involved processing sequence for such an application. This process still has the aura of an art form, and screen printers are sometimes viewed as the last prima donnas in the industry. In today’s digital environment, they appear to be losing ground to a new, much simpler legend print process based on inkjetting, as shown in Figure 3. There is no lead time for phototool preparation and screen patterning. The legend information can be digitally changed, even from board to board, if needed. Yet, the printing process is slower compared to screen printing so that early applications favor prototyping and small lot manufacturing, just like laser direct imaging (LDI) found its early adoptions in these applications.
Figure 2: Process flow for conventional screen printing of legend. (source: Printar)
Figure 3: Process flow for legend print by inkjetting. (source: Printar)
Karl Dietz is President of Karl Dietz Consulting LLC. He is offering consulting services and tutorials in the field of circuit board and substrate fabrication technology. Dietz may be reached by e-mail at karldietz@earthlink.net or phone (001) 919 870 6230.Editor's Note: This article originally appeared in the February 2013 issue of The PCB Magazine.
More Columns from Karl's Tech Talk
Karl's Tech Talk: Digital Imaging UpdateKarl’s Tech Talk: Electronic Packaging Levels
Green Legislation and the Impact on Electronic Materials and Processes
Digital Imaging Revisited
Dry Film Photoresist Thickness Selection Criteria
Quick-Turn Circuit Board Shops
Optical Interconnects
Signal Loss