-
- News
- Books
Featured Books
- design007 Magazine
Latest Issues
Current IssueProper Floor Planning
Floor planning decisions can make or break performance, manufacturability, and timelines. This month’s contributors weigh in with their best practices for proper floor planning and specific strategies to get it right.
Showing Some Constraint
A strong design constraint strategy carefully balances a wide range of electrical and manufacturing trade-offs. This month, we explore the key requirements, common challenges, and best practices behind building an effective constraint strategy.
All About That Route
Most designers favor manual routing, but today's interactive autorouters may be changing designers' minds by allowing users more direct control. In this issue, our expert contributors discuss a variety of manual and autorouting strategies.
- Articles
- Columns
- Links
- Media kit
||| MENU - design007 Magazine
EchoStar’s Les Beller Shares the PCB Design-to-Fab Process
May 10, 2015 | Barry Matties, I-Connect007Estimated reading time: 15 minutes
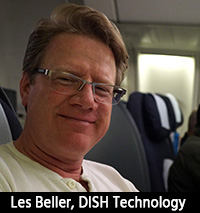
Recently, I had the opportunity to meet and interview Les Beller of EchoStar Technologies. Beller’s career began in the early 1980s as a circuit board designer, eventually leading him to EchoStar, where he has managed the PWB design group and spent time as a PCB quality engineer. He is now a manufacturing process engineer specializing in DFx.
In this interview, Beller focuses on the many challenges circuit board designers face, strategies for bridging the gap between circuit design and fabrication, and the future of circuit designers.
Barry Matties: Les, tell us about your history in the circuit board industry. How did you get started?
Les Beller: I began by hand-drafting schematics and then went into tape and Mylar. That was in 1982 or so, when I was 18. That led into AutoCAD-based software tools for circuit board design and working for design agencies. I ended up selling Layout and fab work in a small prototype board shop using the Daisy/Cadnetix and P-CAD platforms in the front-end.
From there, I ended up moving into a higher-volume consumer products company at EchoStar Technologies, which designs set top boxes (STBs).
Matties: How does that design and fab experience translate into what you're doing now? Does it give you any insight into your role in manufacturing?
Beller: I can't even imagine how many times it has helped me out. Most manufacturing engineers that I had worked with prior would know what they wanted to happen on the manufacturing line, but didn't know what the PCB was capable of. They were relying upon the energy level or the motivation of the layout person, who in some cases was with a job shop with little or no motivation for further improving the product.
It is a big limitation when you don't have a PCB fabrication and design background and you're on the shop floor, because you don't know what the PCB is capable of or what you can do to the PCB to make it more successful as a substrate.
Matties: I would think the types of products you are currently putting PCBs into are all home-use products for the television, probably on the scale of millions.
Beller: That is correct. We bring our customer design and manufacturing solutions at the STB and application level, so that they can focus on the marketing side. STBs are our primary focus as well as support for mobile devices…linking them into consumers’ home content.
Matties: Is all your circuit board design done inside your company or do you farm that out?
Beller: Currently, we have three design sites that are captive held offices. Two design centers in the U.S. and one in the UK. Separate of that is our Bangalore, India office which uses a third-party layout group. Behind those layout groups are about 50-60 hardware engineers. We also have industrial design, sheet metal and plastics design capability in-house, tying together the mechanical puzzle-pieces nicely.
Matties: When EchoStar’s designers are working, what challenges do they face or what obstacles do they see?
Beller: The biggest is the challenge of taking 2x the amount of electrical bits and stuffing it into a 1.5x smaller box. Some hardware or management level people may not understand that you need to do more front-end work in the design to be successful—you need to have floor planning, and you need to have a good engineer and mechanical designer behind you that can make adjustments to the requirements of the product on-the-fly. Occasionally, we may even take the changes all the way back to the Industrial design if applicable.
We’ve developed several ways of estimating our density, estimating our pin count, net count, connection count, and using historical numbers to establish a methodology to estimate how much we can put in a given design based on the available space from our mechanical drawing. It’s been one of the better layout practices we have developed.
Matties: So the way it works is engineers imagine a product, draw it up, and come back and say, "We need a board that fits into this," and your job is to get a board that fits.
Beller: That is correct. That's one of the first challenges that every layout guy would be nodding his head to right now—how to communicate back to the engineers exactly where you need more space or if your hands are too tied to do what they need in the layout.
Some of the other challenges are component selection, such as engineers wanting more real estate than their circuit can support or requires, and working with different engineers on the same design. Our layout designers are working with probably six or eight different design engineers (on larger boards), and they each have different approaches and sub-schedules to attain.
One way that we've answered this challenge is by using Mentor; we're using the team product, which is a design-sharing layout tool that allows us to put more than one designer on a given project, each of them working with different design engineers in parallel, allowing us shorter layout design cycles.
One designer always takes lead role in a design, responsible for schedule and integration, ECOs, etc. The entire layout team takes responsibility for their respective circuits. Another challenge is just having engineers that are, let's face it, different. Some engineers know exactly what they want, and some need to see the layout as you go along. You've got to be able to work with different personalities, and professional levels as well as different functional areas such as digital, power, RF, DDR, etc.
Matties: Being a captive facility, however, I would think that you guys have an advantage over a design shop because your teams can easily communicate, whereas if I'm a design service bureau I just get a spec and I have to make it fit.
Beller: We do have a benefit over a design bureau in that we do have the engineers there. If the layout person has an issue, he calls the engineer over. The engineer sits down with him and they solve the challenge together immediately. There is heavy ownership by both the engineer and the layout person and we find fewer mistakes are the result. We don’t have the additional challenge of answering to different customer needs like a design bureau does.Page 1 of 3
Testimonial
"In a year when every marketing dollar mattered, I chose to keep I-Connect007 in our 2025 plan. Their commitment to high-quality, insightful content aligns with Koh Young’s values and helps readers navigate a changing industry. "
Brent Fischthal - Koh YoungSuggested Items
Mastering PCB Floor Planning
08/28/2025 | Stephen V. Chavez, Siemens EDAPlacement of PCB components is far more than just fitting components onto a board. It’s a strategic and critical foundational step, often called “floor planning,” that profoundly impacts the board’s performance, reliability, manufacturability, and cost. Floor planning ties into the solvability perspective, with performance and manufacturability being the other two competing perspectives for addressing and achieving success in PCB design.
Elementary Mr. Watson: Routing Hunger Games—May the Traces Be Ever in Your Favor
08/26/2025 | John Watson -- Column: Elementary, Mr. WatsonI’d like to share a harsh truth, and I say this as a friend: PCB designers are often their own worst enemy. It’s rarely the complexity of the circuit, the last-minute changes from mechanical, the limited enclosure space, or the ever-expanding list of design rules that send projects to the dust heap of failed boards. More often, it's our own decisions, made too quickly and narrowly, and with too little foresight, that sabotage an otherwise good design.
Target Condition: Floor Planning Without a Floor
08/27/2025 | Kelly Dack -- Column: Target ConditionBy a show of hands, how many PCB designers have been asked to start a layout without a board outline, keep-out zones, or even height constraints? How many have had to work within a specific enclosure before the schematic was finalized? If this sounds familiar, you're not alone. Starting a PCB layout without critical constraints is like hiring an interior designer to buy furniture and carpet for a house you haven’t even purchased yet, or, even worse, trying to fit four bedrooms' worth of furniture in a one-room cabin.
I-Connect007 Editor's Choice: Five Must-Reads for the Week
08/22/2025 | Andy Shaughnessy, I-Connect007In this week’s roundup, we have a variety of articles covering design, manufacturing, sustainability, and, of course, tariff negotiations. We have a milestone anniversary to celebrate as well, with Dan Beaulieu about to publish his 1,000th column. When does Dan even sleep? Here’s to hoping that we have 1,000 more weeks of "It’s Only Common Sense."
New Episode Drop: MKS’ ESI’s Role in Optimize the Interconnect
08/26/2025 | I-Connect007In this latest episode, Casey Kruger, director of product marketing at MKS’ ESI, joins On the Line With… host Nolan Johnson to share how CO₂ laser technology delivers faster, more accurate vias in a smaller, more energy-efficient footprint.