-
-
News
News Highlights
- Books
Featured Books
- smt007 Magazine
Latest Issues
Current IssueWhat's Your Sweet Spot?
Are you in a niche that’s growing or shrinking? Is it time to reassess and refocus? We spotlight companies thriving by redefining or reinforcing their niche. What are their insights?
Moving Forward With Confidence
In this issue, we focus on sales and quoting, workforce training, new IPC leadership in the U.S. and Canada, the effects of tariffs, CFX standards, and much more—all designed to provide perspective as you move through the cloud bank of today's shifting economic market.
Intelligent Test and Inspection
Are you ready to explore the cutting-edge advancements shaping the electronics manufacturing industry? The May 2025 issue of SMT007 Magazine is packed with insights, innovations, and expert perspectives that you won’t want to miss.
- Articles
- Columns
- Links
- Media kit
||| MENU - smt007 Magazine
BGA or CGA: When Is It Right for You?
May 25, 2015 | Barry Matties, I-Connect007Estimated reading time: 6 minutes
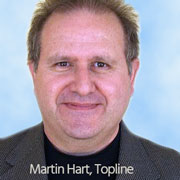
In this interview with TopLine President and Founder Martin Hart, the focus is column grid array (CGA) and how CGA can solve delamination problems. CGAs, also known as CCGA, are not necessarily new but are making a strong comeback in the high reliability market.
Barry Matties: Martin, I've known you for years, but I really haven't understood clearly what your background is. Please give our readers a brief summary.
Martin Hart: I graduated with an electrical engineering degree back in the age of dinosaurs. My engineering background helps to develop products and build a company.
Matties: How long has TopLine been in business and what is it that your company provides?
Hart: TopLine is celebrating 25 years and it has been an exciting run. We entered the market in the late 1980s when SMT technology was taking off. We started off by providing dummy components and test vehicles to run through pick-and-place machines. We helped customers with process development. We've seen a lot of new technologies transition over the past two and a half decades. We've seen technologies come and go. Some technologies have stuck while other technologies have been improved upon.
TopLine's mission is to assist process engineers who are developing new products and assembly processes. Our core product line has been daisy chain IC packages for process development. We have stayed in that niche for quite a while.
Our new thrust product is column grid arrays (CCGA). There has been a big need for improving BGAs reliability in terms of relieving stress that is caused by CTE (coefficient of thermal expansion) mismatch between the BGA substrate and the PC board.
Matties: One thing that I hear quite a bit about is head-in-pillow issues. Does this help address that as well?
Hart: That’s a good question. Column grid arrays are not susceptible to a head-in-pillow phenomena.
In a CCGA, a large solder fillet is formed by reflowing solder-paste around both ends of the solder column. The solder fillet is not only at the chip side, but also on the PC board side. Head-in-pillow has not been the predominant issue with CCGA. There are a lot of other issues when it comes to attaching solder columns. We've been working through the issues and providing customers with solutions.
The main benefit of using column grid arrays is absorbing CTE mismatch between materials.
Matties: How does the CGA marketplace look for you?
Hart: The column grid array market is a niche market. It is an area that TopLine feels really comfortable working in.
The customers who buy CCGAs, high-end mil/aero defense contractors, need a solution and they're coming to TopLine for that solution with column grid arrays.
Matties: With a customer list like that, price isn't an issue, right?
Hart: The advantage of working in a niche market is that we are actually solving customer problems. Price is the last thing that is discussed. Here’s why: The actual chip might cost $25,000 or $50,000. So the cost of attaching the solder columns is trivial compared to the actual end-user cost for the device itself.
Matties: Were these customers using BGAs previously?
Hart: The crossover is when the BGA chip substrate is large, especially if it's made out of ceramic. You cannot reliably use solder balls on large ceramic BGAs. Large ceramic BGAs are prone to solder ball delamination with temperature cycling. Cycling means that temperature swings from hot to cold and then again to hot, with as much as ± 100 degrees from ambient temperature. Solder balls will crack or rip off the board, whereas a solder column will keep attached to the chip and to the PC board.
Such devices often go into space where re-work in the field is not possible. When you use a large ceramic BGA, there is actually a 10 ppm per degree Celsius mismatch between the chip and the PC board. 10ppm doesn't sound like much, but it can cause solder balls to delaminate over time.
To calculate the stress on BGA balls, use simple arithmetic. Take 10 ppm multiplied by the temperature swing multiplied by the distance from corner-to-corner of your device. For example, a device that is 45 mm square can have as much as 75 microns of movement from corner to corner of the BGA. That is 3 mils, which translates into the thickness of a sheet of paper. That doesn't sound like much, but if your device is constantly moving under stress, the distance of a sheet of paper is a huge percentage of the diameter of the solder ball that is holding the BGA onto the board. The way to increase reliability is to replace solder balls with solder columns.
A column will survive 2,000–3,000 temperature cycles, whereas a BGA with solder balls may delaminate after 100 temperature cycles for these large ceramic devices.
Matties: So it is substantially better in this particular application?
Hart: Yes, CCGAs are better suited than BGA for large ceramic substrate devices. Column grid arrays have been available in the market for a long time. CCGA is a legacy technology. It's not a new technology. It is still a very valid technology for large ceramic CCGA devices for absorbing CTE mismatch on a FR-4 or polyimide PC board. Solder column technology prevents delamination.
Matties: So it is re-emerging because because of reliability requirements?
Hart: Exactly. There have been a few market dynamics that have come about that have helped to propel our CCGA product line. IBM, who was a major producer of column grid arrays, exited the market last year. They left a void that needed to be filled. The need for CCGA product didn't go away even though IBM exited the market. The need for CCGA is present. We are helping customers find the solution by filling the need.
Matties: It has been great to hear your story. Anything else that you would like to add that you think people should know?
Hart: Specifically concerning column grid arrays, TopLine is open, ready, and willing to work on solutions with any customer. We are developing new products such as columns with a lower thermal resistance path that can dissipate heat through the column, as opposed to relying on the traditional method of mounting a large heat sink on the IC package.
In outer space, thermal dissipation behaves differently. A heat sink is not as effective when you go up to zero gravity. Whereas, if you can dissipate some of the heat through a column into the ground plane of a PC board, that's the preferred choice.
Matties: When should a customer consider this technology?
Hart: It really comes down to the size of the BGA device. If you're dealing with smaller BGAs, say 10 mm square, there's probably no reason to go with a solder column. Once you start moving up to devices that are 25 mm, basically an inch or more, to 35–45 mm sizes, the advantages of CCGA start to become evident.
Anyone using a large size ceramic mounted onto a PC board would benefit by looking at a CCGA solution. The bigger the device gets, the more stress it will handle due to CTE mismatch. That's when the IC package really needs solder columns.
Matties: It's been great talking to you today.
Hart: Thank you very much.
CLICK FOR RELATED VIDEO:
Suggested Items
Silicon Mountain Contract Services Enhances SMT Capabilities with New HELLER Reflow Oven
07/17/2025 | Silicon Mountain Contract ServicesSilicon Mountain Contract Services, a leading provider of custom electronics manufacturing solutions, is proud to announce a significant upgrade to its SMT production capability with the addition of a HELLER 2043 MK5 10‑zone reflow oven to its Nampa facility.
Knocking Down the Bone Pile: Addressing End-of-life Component Solderability Issues, Part 4
07/16/2025 | Nash Bell -- Column: Knocking Down the Bone PileIn 1983, the Department of Defense identified that over 40% of military electronic system failures in the field were electrical, with approximately 50% attributed to poor solder connections. Investigations revealed that plated finishes, typically nickel or tin, were porous and non-intermetallic.
SHENMAO Strengthens Semiconductor Capabilities with Acquisition of PMTC
07/10/2025 | SHENMAOSHENMAO America, Inc. has announced the acquisition of Profound Material Technology Co., Ltd. (PMTC), a premier Taiwan-based manufacturer of high-performance solder balls for semiconductor packaging.
KYZEN to Highlight Understencil and PCB Cleaners at SMTA Querétaro Expo and Tech Forum
07/09/2025 | KYZEN'KYZEN, the global leader in innovative environmentally responsible cleaning chemistries, will exhibit at the SMTA Querétaro Expo & Tech Forum, scheduled to take place Thursday, July 24, at Centro de Congresos y Teatro Metropolitano de Querétaro.
Driving Innovation: Direct Imaging vs. Conventional Exposure
07/01/2025 | Simon Khesin -- Column: Driving InnovationMy first camera used Kodak film. I even experimented with developing photos in the bathroom, though I usually dropped the film off at a Kodak center and received the prints two weeks later, only to discover that some images were out of focus or poorly framed. Today, every smartphone contains a high-quality camera capable of producing stunning images instantly.