-
- News
- Books
Featured Books
- smt007 Magazine
Latest Issues
Current IssueWhat's Your Sweet Spot?
Are you in a niche that’s growing or shrinking? Is it time to reassess and refocus? We spotlight companies thriving by redefining or reinforcing their niche. What are their insights?
Moving Forward With Confidence
In this issue, we focus on sales and quoting, workforce training, new IPC leadership in the U.S. and Canada, the effects of tariffs, CFX standards, and much more—all designed to provide perspective as you move through the cloud bank of today's shifting economic market.
Intelligent Test and Inspection
Are you ready to explore the cutting-edge advancements shaping the electronics manufacturing industry? The May 2025 issue of SMT007 Magazine is packed with insights, innovations, and expert perspectives that you won’t want to miss.
- Articles
- Columns
- Links
- Media kit
||| MENU - smt007 Magazine
EMI-caused EOS Sources in Automated Equipment
July 23, 2015 | Vladimir Kraz, OnFILTER Inc.Estimated reading time: 10 minutes
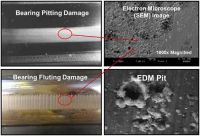
"Electrical overstress (EOS) is the number one cause of damage to IC components" states Intel in its Manufacturing Enabling Guide1. While most manufacturers are concerned with electrostatic discharge (ESD), not enough attention is paid to the much more damaging EOS phenomenon.
Significant source of EOS in manufacturing environment is high-frequency noise (often called electromagnetic interference, or EMO). High-frequency noise is present in most manufacturing tools such as pick-and-place machines, lead trimmers, wire bonders and many others. This noise is caused by operation of various electric and electronic equipment, both inside the tool and by the tools nearby or even far away. Understanding the sources of EMI and how to mitigate EMI-caused EOS exposure is important for safe handling of sensitive components.
Sources of EMI in Tools
Every electrical and electronic equipment generates some sort of artifacts on power line and ground during its operation. Different types of equipment generate different types of noise.
Commutation of Power
Figure 1: Power line transient from turning on heat gun.
Commutation of power, such as turning equipment on and off causes strong transient signals. Figure 1 shows typical voltage spike caused by turning on a regular heat gun. The more powerful the load, the stronger the spike. This type of transient noise does not easily follow an observable pattern and often is difficult to diagnose, in part because the spike can originate quite far away from the source and propagate via power lines and ground.
It doesn't take an entire tool to be turned on or off in order to produce a significant transient signal - all it takes is to have heating element, solenoid or other load within the tool to be turned on or off. The resulting transient signal propagates throughout the tool via common power and ground.
Dimmers/Gradual Heat Control
Figure 2: Noise from the dimmer.
Common power line dimmers that control light brightness, such as in microscope light, or temperature of certain heating elements produce periodic spikes synchronized with the power line frequency. Typical waveform of noise from dimmer is shown in Figure 2.
Switched Mode Power Supplies (SMPS)
While many power supplied provide small manageable level of noise, there are enough SMPS in use that skip on noise suppression and serve as a major source of electromagnetic interference. Switch mode power supplies generate DC voltage from AC mains using high-frequency pulses (typically between 40 and 200kHz). These pulses have sharp edges which are the main culprits in generating undesirable noise. This noise may have rather complex waveform as illustrated in Figure 3. It is important to know that SMPS generate noise both on DC output and on AC mains.
Uninterruptable Power Supplies (UPS)
Figure 3: Noise on AC mains generated by several switched mode power supplies.
UPS provide AC power to your equipment when main AC power either fails completely or when its key parameters fall below acceptable levels. In such cases UPS reconstructs AC mains power from its internal battery. The output power in case of mains failure, however, is far removed from the expected sinewave. It is most likely a square wave with sharp edges that cause significant high frequency noise at the output.
Figure 4 shows AC output of a typical UPS (blue trace) and resulting high-frequency pulses on power line (red trace). Power conditioning in absolute majority of UPS does not include noise filtering and, in those that do, it is mostly sub-standard.
Figure 4: Noise from UPS.
Servo and Variable Frequency Motors
Almost every equipment with moving parts utilizes either servo or variable frequency motors. They are a workhorse of today's automation. Unfortunately, they are also the strongest source of EMI in the tools. These motors are driven by the pulses ranging typically between 8kHz and 20kHz with sharp edges only a few nanoseconds long. This pollutes the entire tool, especially its ground, with strong sharp transients with repetition rate of that of drive pulses.
Figure 5 shows how rising edge of servo motor drive pulse (red trace) is synchronized with ground current inside the tool (blue trace). This current was measured using Tektronix' CT1 current probe and with its 5mV/mA ratio the ground current peak-to-peak measure is almost 2A with width of pulses of under 100nS.
Figure 5: Effect of servo motor pulse on ground noise.
A typical production tool has several servo/variable frequency motors, sometimes more than 10. Combined electrical noise from all motors can significantly pollute the ground of the entire tool.
Page 1 of 3
Suggested Items
Seeing a Future in Mexico
07/09/2025 | Michelle Te, I-Connect007The Global Electronics Association (formerly known as IPC) has been instrumental in fostering a partnership with Guanajuato, a state north of Mexico City with 12 industrial clusters and close to 150 companies involved in electronics. This past spring, Alejandro Hernández, the undersecretary for investment promotion in Guanajuato, attended IPC APEX EXPO 2025 at the invitation of IPC Mexico Director Lorena Villanueva, where he met with several companies to discuss the opportunities available in Mexico. He is inviting electronics-related companies seeking long-term investment in a centrally located area with access to highways, railways, and ports.
The Global Electronics Association Releases IPC-8911: First-Ever Conductive Yarn Standard for E-Textile Application
07/02/2025 | Global Electronics AssociationThe Global Electronics Association announces the release of IPC-8911, Requirements for Conductive Yarns for E-Textiles Applications. This first-of-its-kind global standard establishes a clear framework for classifying, designating, and qualifying conductive yarns—helping to address longstanding challenges in supply chain communication, product testing, and material selection within the growing e-textiles industry.
IPC-CFX, 2.0: How to Use the QPL Effectively
07/02/2025 | Chris Jorgensen, Global Electronics AssociationIn part one of this series, we discussed the new features in CFX Version 2.0 and their implications for improved inter-machine communication. But what about bringing this new functionality to the shop floor? The IPC-CFX-2591 QPL is a powerful technical resource for manufacturers seeking CFX-enabled equipment. The Qualified Product List (QPL) helps streamline equipment selection by listing models verified for CFX compliance through a robust third-party virtual qualification process.
The Knowledge Base: A Conference for Cleaning and Coating of Mission-critical Electronics
07/08/2025 | Mike Konrad -- Column: The Knowledge BaseIn electronics manufacturing, there’s a dangerous misconception that cleaning and coating are standalone options, that they operate in different lanes, and that one can compensate for the other. Let’s clear that up now. Cleaning and conformal coating are not separate decisions. They are two chapters in the same story—the story of reliability.
Advancing Aerospace Excellence: Emerald’s Medford Team Earns Space Addendum Certification
06/30/2025 | Emerald TechnologiesWe’re thrilled to announce a major achievement from our Medford, Oregon facility. Andy Abrigo has officially earned her credentials as a Certified IPC Trainer (CIT) under the IPC J-STD-001 Space Addendum, the leading industry standard for space and military-grade electronics manufacturing.