-
- News
- Books
Featured Books
- smt007 Magazine
Latest Issues
Current IssueWhat's Your Sweet Spot?
Are you in a niche that’s growing or shrinking? Is it time to reassess and refocus? We spotlight companies thriving by redefining or reinforcing their niche. What are their insights?
Moving Forward With Confidence
In this issue, we focus on sales and quoting, workforce training, new IPC leadership in the U.S. and Canada, the effects of tariffs, CFX standards, and much more—all designed to provide perspective as you move through the cloud bank of today's shifting economic market.
Intelligent Test and Inspection
Are you ready to explore the cutting-edge advancements shaping the electronics manufacturing industry? The May 2025 issue of SMT007 Magazine is packed with insights, innovations, and expert perspectives that you won’t want to miss.
- Articles
- Columns
- Links
- Media kit
||| MENU - smt007 Magazine
Estimated reading time: 6 minutes
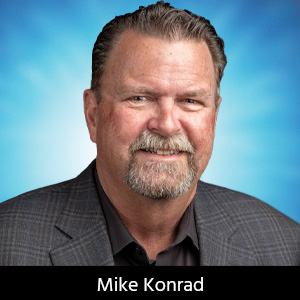
The Knowledge Base: A Conference for Cleaning and Coating of Mission-critical Electronics
In electronics manufacturing, there’s a dangerous misconception that cleaning and coating are standalone options, that they operate in different lanes, and that one can compensate for the other.
Let’s clear that up now.
Cleaning and conformal coating are not separate decisions. They are two chapters in the same story—the story of reliability. When done properly, they protect the assembly from environmental threats and internal failure mechanisms alike. But when shortcuts are taken—when one is ignored or rushed—the results can be costly and, in high-reliability environments, catastrophic.
This is the kind of conversation the SMTA High-Reliability Cleaning and Coating Conference, coming up Aug. 12–14, 2025, at the Westin DFW Airport in Dallas, was built for. The goal? Equip manufacturers with practical, evidence-based strategies for building and protecting assemblies that last.
In this column, we’ll explore why cleaning and coating are so intertwined, what the best practices look like, and how a thoughtful, combined approach is the only way to ensure product reliability in today’s demanding environments.
The Real Job of Cleaning
After reflow, circuit assemblies are often left with flux residues, board and component fabrication contamination, and environmental particulates. These aren’t always visible, but they’re very real, and very dangerous.
Here’s why: Ionic contamination, particularly residues from flux activators, even from no-clean fluxes, can be hygroscopic, attracting moisture from the air, creating a localized, conductive path across the surface of the assembly. This phenomenon, electrochemical migration (ECM), can lead to parasitic leakage, dendritic growth, corrosion, and ultimately, failure.
If you’ve ever inspected a failed board and seen tree-like metal structures or white, fuzzy residues growing between leads, you’ve seen ECM in action in the form of dendritic growth. It doesn’t take a flood to get there. In many cases, condensation from temperature swings or trapped humidity under low-standoff components is all it takes to trigger the process.
It’s important to note: No-clean doesn’t mean don’t clean. Flux residues from no-clean formulations are still there; they’re just harder to see. With today’s high-density designs, tighter spacing, and bottom-terminated components, there’s even less tolerance for residue than ever before.
Cleaning removes those residues. But more importantly, it removes the potential for reliability defects that don't always show up right away. They wait—and they show up later, in the field, under load, when failure is most expensive.
What Coating Is—and Isn’t
Conformal coating has one job: to protect the board from external environmental threats like moisture, dust, chemicals, and mechanical abrasion. It acts as a barrier, sealing the assembly and extending its service life in harsh conditions.
But here’s the truth: Coating is not a fix for contamination.
If you coat a dirty board, you’re not protecting it; you’re sealing in the problem. Ionic residues trapped beneath the coating can continue to attract moisture, corrode metal surfaces, and/or trigger ECM. Since many conformal coatings are moisture permeable, they won’t stop water vapor from getting through. That moisture just gets stuck inside, next to the contaminants you tried to ignore.
Worse yet, residues interfere with coating adhesion. That can lead to delamination, cracking, or bubbling.
In other words, coatings only work when applied to clean surfaces. If you skip or shortcut cleaning, you’ve just wasted your coating, and your time.
Cleaning Best Practices: What Good Looks Like
Good cleaning isn’t about blasting boards with a cleaning solution and hoping for the best. It’s a defined, measurable process with inputs and outputs that can, and should, be monitored.
Here’s what matters:
1. Know your contaminants.
What residues are you dealing with? Flux type, board and component fabrication residues, handling residues, and environmental particles all need to be considered. You can’t solve what you haven’t defined.
2. Choose the right cleaning chemistry.
While aqueous-based cleaning technology is the most popular cleaning method, semi-aqueous, and solvent-based systems each have their place. The chemistry must be compatible with the residue type, assembly materials, and your environmental and safety constraints.
3. Focus on under-component cleaning.
Low standoff components like QFNs and BGAs trap contamination underneath. Cleaning systems must produce the right fluid dynamics—wide diffusion, high impingement, and shadow-mitigating spray patterns—to get under those components and flush contaminants out.
4. Rinse thoroughly.
It’s not just about cleaning, it’s about rinsing away both residues and cleaning chemistry. Deionized (DI) water rinsing, with real-time resistivity monitoring, helps confirm that the job is done.
5. Dry completely.
Moisture left behind is a recipe for trouble. Use a combination of convection and radiant drying (if available) and confirm that drying cycles are long enough to remove water from under components.
6. Validate and monitor.
Process validation tools include:
- SIR testing (for process validation and IPC-required objective evidence)
- Resistivity of solvent extract (ROSE) testing (for IPC-required process monitoring)
- Visual inspection
- In situ rinse water resistivity measurement
With the new IPC J-STD-001J, manufacturers are now expected to produce objective evidence of cleanliness via surface insulation resistance (SIR) testing and process monitoring via ionic contamination (ROSE) testing, not just pass a test at the end.
Coating Best Practices: Seal the Deal
Once a board is clean, it’s ready to be coated. But that doesn’t mean the hard part is over.
1. Pick the right coating.
Each material has trade-offs:
- Acrylics: Easy to apply and rework, but permeable
- Urethanes: Tougher, more chemical resistant
- Silicones: High temperature, moisture resistant
- Parylenes: Best barrier, vacuum deposited, expensive
Base your choice on the actual environment the assembly will face, not just what’s on the datasheet.
2. Control the environment.
Apply coatings in a clean, controlled area. Dust, oils, and humidity can all interfere with adhesion and create defects.
3. Apply correctly.
Spray, dip, brush, or vapor-deposit: each method has pros and cons. Robotic selective spray systems provide precision and repeatability. Whatever the method, ensure:
- Proper thickness (typically 25–75 µm)
- Full coverage without bridging or voids
- Avoidance of trapped air and bubbles
4. Cure thoroughly.
Some coatings air-dry. Others require heat or UV. Incomplete cure means incomplete protection. Always follow the material specs and confirm final properties through testing.
Clean and Coat: When You Need Both
There are environments where cleaning alone might suffice. But when the stakes are high, when you’re building for aerospace, defense, automotive, industrial controls, or mission-critical consumer devices, you don’t want to guess.
You clean to eliminate the root causes of failure. You coat to protect against what’s coming.
Together, they provide layered protection. Alone, they may leave gaps.
A Word on Standards
If you haven’t already studied the latest changes in section 8 of IPC J-STD-001J, it’s time. The industry has moved away from legacy subjective “pass/fail” cleanliness limits and toward objective evidence and process monitoring. That means manufacturers need to understand their cleaning process in a far more detailed way than ever before.
Likewise, IPC-CC-830 and IPC-HDBK-830 provide critical guidance on coating material performance, inspection criteria, and defect prevention.
This is exactly the kind of content being explored at the SMTA High-Reliability Cleaning and Coating Conference in Dallas this August. If you’re serious about reliability, this is a conference worth attending.
Final Thoughts: Reliability Is a Process
Electronic failures rarely happen at the point of manufacture. They happen later, on a snowy runway, in a hot enclosure, or after 10,000 operating cycles. They happen when a shortcut taken today turns into a field return tomorrow.
Cleaning and conformal coating are not just production steps. They are reliability strategies. When done correctly, and together, they provide insurance against the unseen, the unexpected, and the unavoidable.
The industry is evolving. So are the contaminants. So is the demand for data-driven cleanliness and protection.
The question is, are we evolving with it?
More information on the SMTA High-Reliability Cleaning and Coating Conference is available here: smta.org/cleaning
This column originally appeared in the July 2025 issue of SMT007 Magazine.
More Columns from The Knowledge Base
The Knowledge Base: Building the Workforce of Tomorrow With EMACThe Knowledge Base: Beyond the Badge—Why Membership Matters More Than Ever
The Knowledge Base: Unlocking the Invisible—The Critical Role of X-ray Technology
The Knowledge Base: At the Forefront of Electronics Manufacturing
The Knowledge Base: Challenges and Considerations of Harsh Environments
The Knowledge Base: My 2025 Industry Wish List
The Knowledge Base: The Era of Advanced Packaging
The Knowledge Base: The Impact of Harsh Environments on Residue Tolerance