-
- News
- Books
Featured Books
- pcb007 Magazine
Latest Issues
Current IssueInventing the Future with SEL
Two years after launching its state-of-the-art PCB facility, SEL shares lessons in vision, execution, and innovation, plus insights from industry icons and technology leaders shaping the future of PCB fabrication.
Sales: From Pitch to PO
From the first cold call to finally receiving that first purchase order, the July PCB007 Magazine breaks down some critical parts of the sales stack. To up your sales game, read on!
The Hole Truth: Via Integrity in an HDI World
From the drilled hole to registration across multiple sequential lamination cycles, to the quality of your copper plating, via reliability in an HDI world is becoming an ever-greater challenge. This month we look at “The Hole Truth,” from creating the “perfect” via to how you can assure via quality and reliability, the first time, every time.
- Articles
- Columns
- Links
- Media kit
||| MENU - pcb007 Magazine
The Sum of All Parts: Planning for a First-Time-Right PCB Design
May 17, 2016 | Sam Sangani, PNC Inc.Estimated reading time: 2 minutes
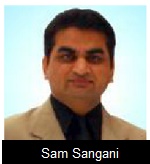
The development of highly integrated and high-speed, chip-based circuit boards brings several functional benefits. But at the same time, these can introduce additional challenges to the actual board itself. Therefore, developing an effective plan for designing, developing, testing and producing the final PCBs is a good business practice.
Lack of communication between PCB designers and PCB fabricators is one of the most significant issues we have faced in our industry. This has led to disconnect in the mutual understanding between these two entities. Subsequently, a scenario has arisen where manufacturers lack the understanding of design guidelines and some designers are not always aware of the manufacturing processes and capabilities of a PCB manufacturer during their design/layout phase.
If we are going to succeed—particularly at the domestic level—we need to open up channels of communication.
Several steps in the PCB design and manufacturing process include areas that allow enhancements that would improve the ease with which boards can be manufactured and decrease the loss rate. Many elements of the process, from the design process to final board test, should be reviewed for improvements that can affect the board’s manufacturability. The ideal way to negate the aforementioned drawbacks would be to design and produce under one roof but, until such a time where this is possible on a large scale, certain measures can be taken to optimize the process as much as possible.
Here are five reasons why designers and PCB manufacturers need to communicate:
1. Critical tolerances vs. yield
With regard to determining what the process can and cannot do, this is a very important factor which affects yield and cost associated in PCB manufacturing.
2. Component placement and solderability
A variation in component density over a PCB surface impacts the uniformity of the soldering of components. Very dense areas may not get enough heat during the reflow process and could result in cold solder joints.
3. Size and uniformity
As the surface area of a PCB gets larger, it brings unwanted irregularities in manufacturing such as the registration of via to pad and warpage on the board surface, making SMT pads or BGA balls unconnected to the PCB. If the proper thickness and stack-up design are taken into account in the initial stages, it would help resolve these types of issues earlier.
4. Transparency
Designers and fabricators working side by side on R&D projects opens up doors not only for the parties involved, but also makes an overall contribution to the industry. Stay up-to-date on new development in processes and technologies. The industry—especially now—is changing rapidly.
5. Long-term business relationships
Once a designer and the PCB manufacturer are actively engaged and get know each other, designers are less likely to try to switch PCB suppliers and start building their relations from scratch. Instead, they can keep building better products when they better understand each other.
Fortunately, communications are moving in the right direction. More and more designers and board houses are starting to engage in productive discussions. Designers are reaching out for plant tours and are developing an interest in the manufacturing process. Golden advice to designers: Do not miss open houses and seminars organized by PCB vendors. Golden advice to PCB suppliers: Do your best to understand designers’ needs.
Sam Sangani is president and CEO of PNC Inc.
Testimonial
"In a year when every marketing dollar mattered, I chose to keep I-Connect007 in our 2025 plan. Their commitment to high-quality, insightful content aligns with Koh Young’s values and helps readers navigate a changing industry. "
Brent Fischthal - Koh YoungSuggested Items
Dr. Jennie Hwang to Present on ‘Solder Joint Reliability’ at SMTA International 2025
09/03/2025 | Dr. Jennie HwangDr. Jennie Hwang to address “Solder Joint Reliability” at the 2025 SMTA International Conference on Monday, October 20. Leveraging her decades of extensive real-world experiences and deep knowledge,
Indium to Highlight Energy-Efficient, High-Reliability Solder Solutions for EV and Electronics at Productronica India
09/03/2025 | Indium CorporationIndium Corporation, a leading materials refiner, smelter, manufacturer, and supplier to the global electronics, semiconductor, electric vehicle (EV), thin-film, and thermal management markets, will feature a range of sustainable, high-reliability solder products at Productronica India, to be held September 17-19 in Bengaluru, India.
Altus Supports Datalink Electronics with Advanced Selective Soldering Solution to Boost Manufacturing Efficiency
09/02/2025 | Altus GroupDatalink Electronics has partnered with Altus Group to integrate a cutting-edge automated soldering solution, enhancing its production capabilities and reinforcing its strategic focus on quality, automation, and scalability.
Connect the Dots: How to Avoid Five Common Causes of Board Failure
09/03/2025 | Matt Stevenson -- Column: Connect the DotsBoards fail for various reasons, and because I’ve been part of the PCB industry for a long time, I’ve seen most of the reasons for failure. As part of my ongoing crusade to help designers design for the reality of manufacturing, here are five common causes for board failure and how to avoid them.
More Than a Competition: Instilling a Champion's Skill in IPC Masters China 2025
09/01/2025 | Evelyn Cui, Global Electronics Association—East AsiaNearly 500 elite professionals from the electronics industry, representing 18 provinces and municipalities across China, competed in the 2025 IPC Masters Competition China, March 26–28, in Pudong, Shanghai. A total of 114 contestants advanced to the practical competition after passing the IPC Standards Knowledge Competition. Sixty people competed in the Hand Soldering and Rework Competition (HSRC), 30 in the Cable and Wire Harness Assembly Competition (CWAC), and 24 in the Ball Grid Array/Bottom Termination Components (BGA/BTC) Rework Competition.