-
- News
- Books
Featured Books
- pcb007 Magazine
Latest Issues
Current IssueThe Hole Truth: Via Integrity in an HDI World
From the drilled hole to registration across multiple sequential lamination cycles, to the quality of your copper plating, via reliability in an HDI world is becoming an ever-greater challenge. This month we look at “The Hole Truth,” from creating the “perfect” via to how you can assure via quality and reliability, the first time, every time.
In Pursuit of Perfection: Defect Reduction
For bare PCB board fabrication, defect reduction is a critical aspect of a company's bottom line profitability. In this issue, we examine how imaging, etching, and plating processes can provide information and insight into reducing defects and increasing yields.
Voices of the Industry
We take the pulse of the PCB industry by sharing insights from leading fabricators and suppliers in this month's issue. We've gathered their thoughts on the new U.S. administration, spending, the war in Ukraine, and their most pressing needs. It’s an eye-opening and enlightening look behind the curtain.
- Articles
- Columns
- Links
- Media kit
||| MENU - pcb007 Magazine
Multiple Markets Merge for PCBs at H&T Global
August 19, 2016 | Patty Goldman, I-Connect007Estimated reading time: 7 minutes
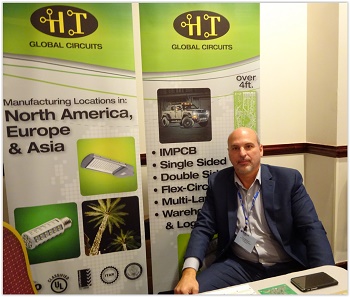
While at the SMTA-Ohio expo I met Rob DiGiovanni, VP of sales and marketing with H&T Global, a printed circuit manufacturer based in Florida. I was attracted to the H&T booth by a large photo of an Army jeep. I wanted to learn what this particular photo had to do with PCBs, and Rob had a ready answer.
Patty Goldman: Hi, Rob. It’s great to see you here in Cleveland. We've already been talking a few minutes here, but one of the things I really want to hear about is this army vehicle which has LED lighting in it. You said it was bringing two worlds together.
Rob DiGiovanni: In printed circuit board manufacturing, two of our strongest market places are military applications and LED lighting. We supply low-to-high volume production of PCBs to these markets. You notice the picture that I've got on our display here and it happens to be a military vehicle with LED lighting. The LED lighting applications are just extraordinary across the marketplace in commercial applications, industrial applications, automotive applications and so on.
Goldman: Someone else also told me that.
DiGiovanni: It is an exploding market. We are heavily invested in the PCB manufacturing for LED lighting as well as military applications. We now manufacture up to 4-foot long metal and fiberglass PCBs. We are Mil-P-55110 certified and ITAR-registered.
Goldman: You literally combined them.
DiGiovanni: Correct. This manufacturer, if you would, is bringing two worlds together.
Goldman: Very disparate worlds. Also automotive, I guess.
DiGiovanni: It is. Even though it's a military vehicle, it is an automotive application, which is a third category, in essence. Automotive is another marketplace that we are heavily invested in. Our facilities are all TS16949 certified. We're automotive certified. Interestingly enough, we talked about LED exploding, but automotive in North America has made a huge surge. Numbers are climbing back to record levels where anybody in the automotive industry is experiencing phenomenal growth right now and are reaping the rewards of a robust economy in that market.
Goldman: Now, you're talking not just automotive, but automotive electronics? The applications continue to almost snowball in the automotive industry.
DiGiovanni: Years ago, the car was just a big piece of metal with some rubber tires on it.
Goldman: And a radio.
DiGiovanni: And a radio. I remember reading a report when I was younger that at some point 60% of the price of the vehicle was going to be electronic related. That's where we are today. Sixty percent of the cost of the car that you buy to drive to work every day, you're paying for the electronics in the vehicle.
Goldman: Amazing, isn’t it? And everything else in there has become a commodity, right?
DiGiovanni: Correct.
Goldman: Then again like you said for LED lighting, whoever thought there would be a circuit board in a light bulb?
DiGiovanni: It's a necessity right now. That's just where the technology is today. High output LEDs require proper heat sinking, heat management, and it starts with the circuit board. You just cannot get the outputs that are required to replace your standard incandescent light bulbs without heat management. So metal circuit boards, insulated metal printed circuit boards (IMPCBs), insulated metal substrate (IMS), there's a number of different acronyms for the technology. It’s very interesting. A common misconception is that the technology is the aluminum on the backside of the circuit board, when in fact all it is a heat sink. The technology lies in the dielectric material. It moves heat away from the components. It takes a little bit in getting to know the product and the technology and understanding what it does. Different dielectrics will perform differently. It's application-specific or whether it's a class driven product. We have access to and can recommend a best fit material for those applications.
Goldman: Yeah, that's a whole area I'm not very familiar with, I have to say.
DiGiovanni: Think of it this way. You can drive a Chevrolet Cruze to work and put six people in the car, and the car will get you to work. It'll struggle a little bit but it will get you there. You can go out and buy a fully loaded Chevrolet Impala and it's going to get all six of you to work a little bit more comfortably and a lot less effort on the vehicle.
Or the six of you can climb into a great big Cadillac limousine and just cruise to work with no effort and no cares whatsoever. Now, the dielectric materials are exactly the same way. There are some materials that move you and struggle. There are some materials that move you comfortably. Then there are some materials that move you with ease. Now translate that into moving heat. Some materials will move heat better, faster, and more efficiently. That's the technology between metal back circuit board.
Goldman: There's always all this heat, especially with LED lighting, you say?
DiGiovanni: Correct.
Goldman: I didn't realize that.
DiGiovanni: As you walk around, here at the SMTA event in Ohio there are a few LED products out and about. Some are on displays. Some are on a table, whatnot. A great example is you can walk into a Home Depot and buy an LED light bulb to screw into any standard A19 fixture in your bedroom. If you ever open one up, you'll realize that the technology that went into that light bulb that now costs ten dollars is remarkable. Because it's replacing a dollar light bulb, the technology has been around for a hundred years. The incandescent light bulb, if you put your hand up close to it, you'll burn your hands. It gets hot if it's on all day. The LED light bulbs, they can't do that. They're electronic. Just like any electronics, heat is its enemy. If the LED continues to get hotter and hotter throughout the day, it'll burn up. Heat management can keep it operating at a standard operating temperature, which has been designed for its most efficient output, so that it can give you hours and hours and hours of consistent light.
Goldman: Then the heat has to be pulled away.
DiGiovanni: In order to do that, heat has to be pulled away and it’s done through metal circuit boards, one of our core products, as they are the foundation of the electronic side of the unit. In a lot of cases it'll use heat sink housing or heat sink assemblies in addition to it. It's all designed by engineers who know a lot more about that than I do.
Page 1 of 2
Suggested Items
I-Connect007 Editor’s Choice: Five Must-Reads for the Week
07/11/2025 | Andy Shaughnessy, Design007 MagazineThis week, we have quite a variety of news items and articles for you. News continues to stream out of Washington, D.C., with tariffs rearing their controversial head again. Because these tariffs are targeted at overseas copper manufacturers, this news has a direct effect on our industry.I-Connect007 Editor’s Choice: Five Must-Reads for the Week
Digital Twin Concept in Copper Electroplating Process Performance
07/11/2025 | Aga Franczak, Robrecht Belis, Elsyca N.V.PCB manufacturing involves transforming a design into a physical board while meeting specific requirements. Understanding these design specifications is crucial, as they directly impact the PCB's fabrication process, performance, and yield rate. One key design specification is copper thieving—the addition of “dummy” pads across the surface that are plated along with the features designed on the outer layers. The purpose of the process is to provide a uniform distribution of copper across the outer layers to make the plating current density and plating in the holes more uniform.
Trump Copper Tariffs Spark Concern
07/10/2025 | I-Connect007 Editorial TeamPresident Donald Trump stated on July 8 that he plans to impose a 50% tariff on copper imports, sparking concern in a global industry whose output is critical to electric vehicles, military hardware, semiconductors, and a wide range of consumer goods. According to Yahoo Finance, copper futures climbed over 2% following tariff confirmation.
Happy’s Tech Talk #40: Factors in PTH Reliability—Hole Voids
07/09/2025 | Happy Holden -- Column: Happy’s Tech TalkWhen we consider via reliability, the major contributing factors are typically processing deviations. These can be subtle and not always visible. One particularly insightful column was by Mike Carano, “Causes of Plating Voids, Pre-electroless Copper,” where he outlined some of the possible causes of hole defects for both plated through-hole (PTH) and blind vias.
Trouble in Your Tank: Can You Drill the Perfect Hole?
07/07/2025 | Michael Carano -- Column: Trouble in Your TankIn the movie “Friday Night Lights,” the head football coach (played by Billy Bob Thornton) addresses his high school football team on a hot day in August in West Texas. He asks his players one question: “Can you be perfect?” That is an interesting question, in football and the printed circuit board fabrication world, where being perfect is somewhat elusive. When it comes to mechanical drilling and via formation, can you drill the perfect hole time after time?