-
-
News
News Highlights
- Books
Featured Books
- design007 Magazine
Latest Issues
Current IssueAll About That Route
Most designers favor manual routing, but today's interactive autorouters may be changing designers' minds by allowing users more direct control. In this issue, our expert contributors discuss a variety of manual and autorouting strategies.
Creating the Ideal Data Package
Why is it so difficult to create the ideal data package? Many of these simple errors can be alleviated by paying attention to detail—and knowing what issues to look out for. So, this month, our experts weigh in on the best practices for creating the ideal design data package for your design.
Designing Through the Noise
Our experts discuss the constantly evolving world of RF design, including the many tradeoffs, material considerations, and design tips and techniques that designers and design engineers need to know to succeed in this high-frequency realm.
- Articles
- Columns
- Links
- Media kit
||| MENU - design007 Magazine
Beyond Design: How to Handle the Dreaded Danglers, Part 2
October 12, 2016 | Barry Olney, In-Circuit Design Pty LtdEstimated reading time: 2 minutes
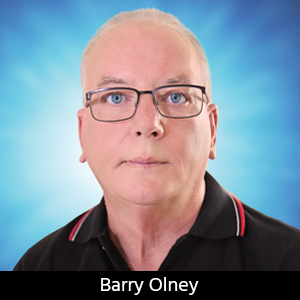
In Part 1 of this series, I deliberated on how dangling via stubs distort signals passing through an interconnect and also decrease the usable bandwidth of the signal. This is due to the via stub acting as a transmission line antenna, which has a resonant frequency determined by the quarter wavelength of the structure. The conventional solution to this problem is to back-drill (or control depth drill) the vias to bore out the via stub barrels, so that the via stubs are reduced in length if not completely removed. This month I will look into all the possible solutions to alleviate this issue.
1. Back-drill the stub
Back-drilling is a process to remove the stub portion of a plated through-hole (PTH) via. It is a post-fabrication drilling process where the back-drilled hole is of larger diameter than the original PTH. This technology is often used instead of blind via technology to remove the stubs of connector vias in very thick high-speed backplane designs. State-of-the-art board fabrication shops are able to back-drill to within 8 mils of the signal layer, so there will always be a small stub portion attached to the via.
High-speed, SERDES, serial link-based backplanes generally have thick substrates. This is due to the system architecture and backplane to card interconnect requirements such as press-fit connectors. Back-drilling the via stub is a common practice, on thick PCBs, to minimize stub length for bit-rates greater than 3Gbps (1.5GHz). However, at transmission rates >10Gbps (5GHz), back-drilling alone may not be adequate to reduce jitter and bit error rate (BER).
Figure 1 shows the effects of excessively long via stubs on a high-speed differential pair. On the left, the differential pair is simulated using a pseudo random bit stream (PRBS) with lossy transmission lines enabled; note the open eye pattern. However, on the right, I had included via modelling, which enables the via parasitics and highlights the effects of via resonance. The high-frequency harmonics are attenuated, rolling off the signal rise time, distorting the signal, reducing bandwidth and closing the eye.
Vias can appear as capacitive and/or inductive discontinuities. These parasitics contribute to the degradation of the signal as it passes through the via. At high frequencies and with thick backplane substrates, it is imperative that these issues are addressed.
Back-drilling typically requires specialized equipment, and further requires that the back-drill be precisely located over the vias. As such, the back-drilling process, especially two sided back-drilling, is expensive due to drill breakage and yield issues and is very time-consuming.
To read this entire article, which appeared in the September 2016 issue of The PCB Design Magazine, click here.
Suggested Items
Excellon Installs COBRA Hybrid Laser at Innovative Circuits
06/23/2025 | ExcellonExcellon is pleased to announce the successful installation of a second COBRA Hybrid Laser System at Innovative Circuits, located in Alpharetta, Georgia. The Excellon COBRA Hybrid Laser System uniquely combines both UV and CO₂ (IR) laser sources on a single platform—making it ideal for high-density prototype and production printed circuit boards (PCBs).
Gorilla Circuits Elevates PCB Precision with Schmoll’s Optiflex II Alignment System
06/23/2025 | Schmoll MaschinenGorilla Circuits, a leading PCB manufacturer based in Silicon Valley, has enhanced its production capabilities with the addition of Schmoll Maschinen’s Optiflex II Post-Etch Punch system—bringing a new level of precision to multilayer board fabrication.
The Evolution of Picosecond Laser Drilling
06/19/2025 | Marcy LaRont, PCB007 MagazineIs it hard to imagine a single laser pulse reduced not only from nanoseconds to picoseconds in its pulse duration, but even to femtoseconds? Well, buckle up because it seems we are there. In this interview, Dr. Stefan Rung, technical director of laser machines at Schmoll Maschinen GmbH, traces the technology trajectory of the laser drill from the CO2 laser to cutting-edge picosecond and hybrid laser drilling systems, highlighting the benefits and limitations of each method, and demonstrating how laser innovations are shaping the future of PCB fabrication.
Sierra Circuits Boosts High Precision PCB Manufacturing with Schmoll Technology
06/16/2025 | Schmoll MaschinenSierra Circuits has seen increased success in production of multilayer HDI boards and high-speed signal architectures through the integration of a range of Schmoll Maschinen systems. The company’s current setup includes four MXY-6 drilling machines, two LM2 routing models, and a semi-automatic Optiflex II innerlayer punch.
Driving Innovation: Traceability in PCB Production
05/29/2025 | Kurt Palmer -- Column: Driving InnovationTraceability across the entire printed circuit board production process is an increasingly important topic among established manufacturers and companies considering new PCB facilities. The reasons are apparent: Automatic loading of part programs, connection with MES systems and collection of production data, and compliance with Industry 4.0 requirements