-
- News
- Books
Featured Books
- smt007 Magazine
Latest Issues
Current IssueIntelligent Test and Inspection
Are you ready to explore the cutting-edge advancements shaping the electronics manufacturing industry? The May 2025 issue of SMT007 Magazine is packed with insights, innovations, and expert perspectives that you won’t want to miss.
Do You Have X-ray Vision?
Has X-ray’s time finally come in electronics manufacturing? Join us in this issue of SMT007 Magazine, where we answer this question and others to bring more efficiency to your bottom line.
IPC APEX EXPO 2025: A Preview
It’s that time again. If you’re going to Anaheim for IPC APEX EXPO 2025, we’ll see you there. In the meantime, consider this issue of SMT007 Magazine to be your golden ticket to planning the show.
- Articles
- Columns
Search Console
- Links
- Media kit
||| MENU - smt007 Magazine
The Taken-for-granted Via
November 8, 2016 | W. Scott Fillebrown, Libra IndustriesEstimated reading time: 3 minutes
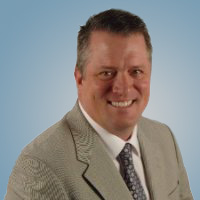
Vias are interesting little creatures. They are so simple, yet they can be so complex at the same time. Designed properly, they complete a circuit. However, a poorly designed via can be a reliability nightmare. The bottom line is that, in many ways, they are the unsung hero to a circuit board, much like an offensive line is to a football team.
Historically, we have tried to minimize their use to save money at the bareboard manufacturer. While this is still common practice, there are times extra vias are a good, useful addition to the board. In today's world, standard vias have very little impact on the costing structure. Complex vias, on the other hand, can add cost and potentially decrease the reliability—clearly not the bargain you wanted.
So what are the different types of vias, and why are they complex? First, the types of vias really have not changed. The most typical are standard vias, which are drilled from one side of the board to the other. Then you have your blind via that can be seen only from one side of the board. Finally, you have your “crazy uncle” via that we call the buried via. He is the one we hide in the middle of the board so no one can see him! While each of these vias has been around for a long time, space constraints have caused significant design approach changes to support them through the manufacturing process.
The largest growth area for vias is blind and buried vias. Many of us remember the days when using a blind or buried via was considered a death nail in the cost structure of our bareboard. We did just about anything to avoid using them. A couple of the micro via approaches including laser drilled vias, and via in pad made them avoidable a while longer. However, over time, blind and buried vias became unavoidable. While still expensive, their use typically is not optional due to space requirements or signal integrity issues. In the past, blind and buried vias required very expensive processes through the board manufacturer, like sequential lamination.
However, today there are many approaches to accomplishing blind and buried vias, which have helped reduce the cost of their implantation. A few of these processes include control depth drill, flip drill, stacked via and staggered vias. Each of these methods has their place, and can be reliable when used properly. However, they also can have their drawbacks. The best recommendation is to become best friends with your board manufacturer and rely on their experience to make recommendations for the most reliable and cost-effective approach for your application. Clearly, blind and buried vias still are a more expensive approach and should be avoided if at all possible. Now, regarding their older brother, standard through-the-board vias, could more be better?
When it comes to a standard via, there are times when more can be better. So often we see a via as another hole in the board; however, many times they can be used for more than a conduit from one layer to another. In the R&D process, they can be used for a simple task like probing to diagnose issues or as a point in the circuit to solder a blue wire for engineering changes. While the engineering lab hopefully is a short stay for your board, having additional vias is not just a short-term gain. The biggest gain for having additional vias is for flying probe test. Flying probe is well on its way to being the standard for testing assembled boards in North America. With the advent of dual-sided testers, you have the potential to reach 95% test coverage. Unlike bed-of-nails testers that requires a 30–40 mil test point, flying probe requires a simple via with a 20 mil pad and a 10 mil hole. This approach gives the high-mix, low- to medium-volume manufacturer a viable test approach that supports every company’s desire for high quality.
To read this entire article, which appeared in the November 2016 issue of SMT Magazine, click here.
Suggested Items
Libra Industries Cleveland Facility Completes AS 9100D Certification
06/07/2021 | Libra IndustriesLibra Industries, a privately-held systems integration and electronics manufacturing services (EMS) provider, is pleased to announce the certification of its Cleveland facility’s Quality Management System to AS 9100D.
RTW SMTAI: Libra's Rod Howell Discusses Tariffs Issue
10/24/2018 | Real Time with...SMTAIRod Howell, CEO of EMS firm Libra Industries, speaks with I-Connect007 Managing Editor Nolan Johnson about the ongoing tariffs issue, how it impacts the global electronics manufacturing supply chain, and their strategic response to address the issue.
Libra Industries Enhances SPI Capabilities
03/27/2017 | Libra IndustriesEMS provider Libra Industries has completed the installation of a third Omron CKD VP5200-V Solder Paste Inspection system at its Mentor facility. The company also runs one Omron SPI system at its Dallas facility.
Libra Industries' Glenn Watson Completes AS9100 Lead Auditor Training
01/11/2017 | Libra IndustriesLibra Industries has announced that Glenn Watson, quality manager at its Dallas facility, recently completed his AS9100 Aerospace Quality Management Systems Lead Auditor training.
Libra Industries Dallas Renews Defense and Medical Certifications
12/05/2016 | Libra IndustriesEMS firm Libra Industries has announced that its Dallas facility has passed the recertification audits for its ISO 9001:2008 and ISO 13485:2012 certifications.