Estimated reading time: 9 minutes
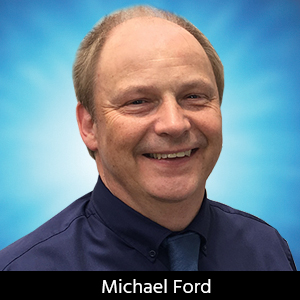
Contact Columnist Form
Smart for Smart's Sake, Part 2: Material Management
Data collection in the factory is not just about machine interfaces and gathering data from related assembly processes, it is also about transactional events that directly affect the production operation. In part 2 of this series, we look at how Lean supply-chain logistics are an essential component of a “smart factory,” and for good reasons, not least of which are the significant benefits that are brought to the operation.
Last time, we looked at how added-value is created by the normalization of data collected from all machines and processes in the factory, as applied to asset utilization, productivity, visibility, and operational improvement. Whatever we each choose to call this digital revolution in electronics manufacturing, it is actually quite familiar for the old-school industrial engineers among us. It is not just “smart for smart’s sake,” because real ROIs are created that provide business success and opportunity. Does this ROI still hold true, however, when we look at material management? This is where the “old-school” could learn some new tricks.
The term “material management” is probably one of the most misused terms in the industry because it has been applied to a range of technologies and solutions, from the simple storage of materials in a generic warehouse to fully featured and automated Lean material-logistics solutions.
We will need to start at the beginning, where incoming materials are received and logged into the enterprise resource planning (ERP) system, to understand the evolution of material management. ERP management is ultimately responsible for the whole factory inventory, and they will use material requirements planning (MRP) as the tool to order materials based on requirements calculated from the factory production plan and current stock levels. ERP needs to decrement materials while they are used to be able to maintain stock level information, which, in the traditional model, is as products are completed ready for shipping either to the customer or to the next significant internal factory process, referencing the associated bill of material.
This seemingly simple process is complex for electronics, especially in SMT production. Materials are over-supplied to production where they are then only partially used because most materials are on carriers, such as reels. Many opportunities exist for attrition throughout the material setup process on the machines and during the machine operation. Unaccounted material creates inaccurate inventory levels within ERP, which leads to unexpected internal material shortages. This situation occurs quickly and is a serious problem for operations with a higher product mix. Because ERP holds increasingly inaccurate representations of inventory, large buffer stocks have to be maintained and a regular physical stock-check has to be performed to prevent unexpected internal material shortages, both of which are expensive processes for the manufacturing operation.
Even the simplest task of putting materials away in the warehouse can lead to problems. For a warehouse to be successfully managed, the space has to be fully utilized, while ensuring that people can easily and quickly find materials when needed. The easiest way to manage warehouse locations is by part number, which is fine for the ERP managers because they only then need to record within the system the general area in which the materials are stored, which may even be just the warehouse name. Materials are physically easy to find if they are stored in locations that are managed alpha-numerically by part number.
Unfortunately, this is inefficient from a space-usage perspective because storage volume requirements for each part number differ depending on the material size, and the quantity needed for each can fluctuate significantly. New part numbers and end-of-life materials can create significant physical issues for re-order material locations, with associated handling issues. Using “random locations” is far more efficient because each location can be used to their maximum capacity for a greater amount of time, where any location can be used for any material.
The issue then is remembering where the materials are. Where the materials are placed must be recorded, and each “carrier” of materials, such as a reel, needs to be managed using a unique ID, which usually is just a simple barcode created and applied when material is received into ERP. Logistics tasks typically require a mobile barcode reader, which is a little extra work for materials operators. A computer system is needed to manage the database of materials and their locations, which most often is not practically supported within ERP. The materials-management functions in the manufacturing execution system (MES) can provide supporting warehouse management or even can be the dedicated warehouse management software.
The use of material carousels creates automated and managed storage locations that are efficient on space. These still require reading the material barcodes into the storage, but at least the need to remember the locations is avoided. The units, where big enough, can exist as a named warehouse as far as ERP is concerned. The limitation with the use of carousels is the time that it takes to get materials into and out of the carousel, which often becomes a bottleneck for the operation. However, another benefit of some carousels is that they offer a dry environment for materials, so that baking and separation of moisture-sensitive materials into dry-store locations is unnecessary. Automated carousels cannot be used for all materials, however, especially the larger assembly items and so, in practice, the carousel system in almost all cases has to coexist within a larger overall material management system.
The first part then of our smart solution is to manage material locations, potentially in multiple warehouses, ensuring that no materials are lost, that good use is made of space, and that materials logistics are managed efficiently.
As well as coming into the warehouse, materials also have to leave the warehouse to be used in production. The old-school method of doing this is to prepare a kit of materials well in advance of the product changeover on the line. Preparing material kits has two challenges. The first is to locate the materials, which our “smart” warehouse location system should solve, but the other issue is that there are often not enough materials available. This can be caused by the oversupply of materials to the shop-floor in other kits, as well as the material spoilage, or attrition of material, accumulated over time, for which the additional buffer stocks have been exhausted.
Because this is a frequent occurrence, with a serious effect on production, preparing kits well in advance is a common practice. Often, in higher mix environments, an entire line of material kits will be prepared in advance for each line. The cost of this legacy practice is ridiculously high; for example, the investment in excess material buffer stock, the stock held in queued kits, the workload to create and maintain multiple kits (because often materials are requisitioned from one kit to another), the space required to store the kits, and the need to tear down and remake the kits should there be a short-term change in the schedule.
All of these costs are a burden to the operation simply because accurate material inventories cannot be maintained and updated in ERP. If they could be accurate, then the majority of the needless buffer stock could be removed, with materials being prepared only as needed for immediate use on the production lines. Here is the opportunity to again use our “smart data” from the factory machines and processes.
The smart, or “Lean,” approach to material management is a simple concept. Collecting accurate material usage and consumption data from the machines and processes means that Lean material-management software can, with the help of the bill of materials and schedule data, calculate the rate at which materials are being used. They also can predict when new materials are needed, either as replenishment of existing reels in use or as part of a product changeover. Delivering materials on a Lean “just-in-time” basis reduces the amount of material WIP needlessly stored on the shop-floor by more than 95%.
Partially used materials have an automatically and accurately maintained count on a per carrier basis, and so they can be reliably returned directly to the warehouse for reallocation to other work orders. The material flow is qualified at the materials verification stage, as materials are loaded on to feeders and/or as feeders are loaded on to specific machine locations. This is normally a standard feature for the machine software using “smart feeders,” where the unique material IDs can seamlessly integrate the machine-centric material-management environment into that of the whole factory.
At a factory level, all of the material logistics jobs can be aggregated over all processes. These would include the put-away of materials into the warehouse, the pick of materials from the warehouse for production (including such rules as “first-in, first-out”), the transfer of materials to the machines and process, the return of the materials from the machine into the warehouse, and an integrity check of warehouse locations when there is available time. Logic within the logistics “engine” can again look forward at the expected material needs, predicting busy times for logistics operations and bringing forward certain tasks to smooth out the task loading. The implementation of such a logistics management system has been shown to reduce the need for material operators by around 30%.
All of this has been made possible through the use of the data collected from all of the machines and processes in the factory. Where a single format for the data collection has been adopted, such as the use of the Open Manufacturing Language (OML), it is quite a simple process to integrate all possible points of material consumption, including manual stations, repair stations, and even material quality-inspection processes.
However, this kind of solution has various layers. For example, machine vendors offer local material carousels or storage towers that store materials close to the line, which is of value when production of specific products is confined to specific lines. Moving materials from one line or shop-floor–area carousel to another should be avoided if possible. A simple kanban extension to the overall factory materials logistics engine, however, can also set up dynamic kanban controls for the flow of materials between warehouses, including even from external supplier warehouses as required. For many operations, a single warehouse is sufficient for a whole site. In other cases, a hierarchical series of warehouses may be used, especially in EMS companies that have dedicated lines to specific customer products.
As we can see, the smart Lean materials solution is quite distinct from the old-school material management practice. Rather than “pushing” materials out in kits based on a factory schedule well in advance, the Lean “pull” system ensures that only materials that are needed are on the shop-floor and that every consumption of material is accounted for. The ERP and associated MRP operation can now run far more efficiently, which can then typically help reduce warehouse stocks by around 50% because of increased inventory accuracy. With all of the other benefits realized, such as the reduction of WIP materials on the shop-floor, the space saving, the logistics savings, the removal of the need of physical stock check, and also the eliminated internal material shortages, a rapid ROI is assured, which, in some cases, has been demonstrated in a matter of a few weeks. Once again, this is clearly not just “smart for smart’s” sake. Here is a real, tangible benefit that is just as applicable to EMS manufacturers as OEMs, even where consigned materials are used. Few other examples can demonstrate where such a modest investment has such a significant impact on the operation.
This is just one more example of the advanced application of data that we are now able to collect using a factory-standard specification such as OML. In the first part of this series, we saw the justification of the use of an approach based only on asset utilization and productivity enhancement. Now, we can add the supply-chain benefits on top of that. Next time, we will look for even more.
More Columns from The Essential Pioneer's Survival Guide
If It's My Data, I Can Do What I Want, Right?The Essential Pioneer's Survival Guide: One Size Fits All?
Smart for Smart’s Sake, Part 3: Unification & Traceability
The 'New Face' of Automotive Traceability
Industry 4.0: Who Benefits?
To Be Lean is to Be Human
Stop the SMT Conspiracy, Part 2: Abduction
The Future of SMT: Welcome to the 4th Dimension