-
- News
- Books
Featured Books
- pcb007 Magazine
Latest Issues
Current IssueSales: From Pitch to PO
From the first cold call to finally receiving that first purchase order, the July PCB007 Magazine breaks down some critical parts of the sales stack. To up your sales game, read on!
The Hole Truth: Via Integrity in an HDI World
From the drilled hole to registration across multiple sequential lamination cycles, to the quality of your copper plating, via reliability in an HDI world is becoming an ever-greater challenge. This month we look at “The Hole Truth,” from creating the “perfect” via to how you can assure via quality and reliability, the first time, every time.
In Pursuit of Perfection: Defect Reduction
For bare PCB board fabrication, defect reduction is a critical aspect of a company's bottom line profitability. In this issue, we examine how imaging, etching, and plating processes can provide information and insight into reducing defects and increasing yields.
- Articles
- Columns
- Links
- Media kit
||| MENU - pcb007 Magazine
Advanced UV Lasers for Fast, High-Precision PCB Manufacturing
December 6, 2016 | Jim Bovatsek, SPECTRA-PHYSICSEstimated reading time: 2 minutes
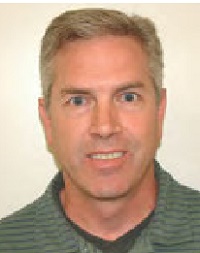
Introduction
For more than 30 years, lasers have played a significant role in the manufacturing of PCBs. It is not a coincidence that electronic devices have, at the same time, become increasingly miniaturized. The ability to tightly focus a laser beam much smaller than a mechanical tool has been an enabler of such dense, compact circuitry; and the elimination of consumables such as drilling and routing bits has reduced manufacturing costs.
The workhorse laser technology over the years has been the carbon dioxide (CO2) laser, which has provided manufacturers with reliable, cost-effective power for various applications. The most identifiable laser process in PCB manufacturing is what is referred to as via drilling, which involves laser drilling a hole through an electrically insulating dielectric layer on a copper substrate. Generally, if the substrate is left intact, the hole is a blind via; if it is also drilled through, it is a through via. Very small holes having diameters below about 150 micrometers are commonly referred to as microvias. After a subsequent copper plating step, an electrical interconnection through the dielectric layer is formed. By arranging these vias in various two-dimensional configurations and by implementing additional build-up, drilling, and plating steps to introduce a third dimension, the high-density interconnect (HDI) and packaging needs of today’s powerful yet compact electronic devices are satisfied.
Making it Smaller
As always there is a mandate for smaller: smaller mobile devices, smaller microchips, smaller electronics packages, and smaller interconnect vias. Vias drilled with CO2 lasers are generally limited to diameters of 60–80 µm or larger due to the long (~10 µm) wavelength of the light, which has a direct bearing on how small the beam can be focused. While smaller via sizes can technically be achieved, the business case quickly vanishes due to higher overall process complexity (and therefore cost).
Here is where shorter-wavelength pulsed ultraviolet (UV) diode-pumped solid-state (DPSS) laser technology enters the picture. The short UV wavelength—about 30 times shorter compared to CO2 wavelengths—can easily be focused to the small sizes necessary for the fabrication of increasingly small microvias. Since the mid-1990s, pulsed UV DPSS lasers with nanosecond (ns) pulse durations have been commercially available for industrial/OEM use. While during the early days of the technology the relatively high cost and troubling reliability issues limited their appeal, today’s products are vastly improved in both areas. Indeed, over the past decade, the cost per Watt for such lasers has fallen by an order of magnitude, and product lifetimes have improved dramatically, in some cases surpassing 20,000 operating hours at high power levels.
To read this entire article, which appeared in the November 2016 issue of The PCB Magazine, click here.
Suggested Items
I-Connect007 Editor’s Choice: Five Must-Reads for the Week
07/18/2025 | Nolan Johnson, I-Connect007It may be the middle of the summer, but the news doesn’t quit, and there’s plenty to talk about this week, whether you’re talking technical or on a global scale. When I have to choose six items instead of my regular five, you know it’s good. I start by highlighting my interview with Martyn Gaudion on his latest book, share some concerning tariff news, follow that up with some promising (and not-so-promising) investments, and feature a paper from last January’s inaugural Pan-European Design Conference.
Elephantech Launches World’s Smallest-Class Copper Nanofiller
07/17/2025 | ElephantechJapanese deep-tech startup Elephantech has launched its cutting-edge 15 nm class copper nanofiller – the smallest class available globally. This breakthrough makes Elephantech one of the first companies in the world to provide such advanced material for commercial use.
Copper Price Surge Raises Alarms for Electronics
07/15/2025 | Global Electronics Association Advocacy and Government Relations TeamThe copper market is experiencing major turbulence in the wake of U.S. President Donald Trump’s announcement of a 50% tariff on imported copper effective Aug. 1. Recent news reports, including from the New York Times, sent U.S. copper futures soaring to record highs, climbing nearly 13% in a single day as manufacturers braced for supply shocks and surging costs.
I-Connect007 Editor’s Choice: Five Must-Reads for the Week
07/11/2025 | Andy Shaughnessy, Design007 MagazineThis week, we have quite a variety of news items and articles for you. News continues to stream out of Washington, D.C., with tariffs rearing their controversial head again. Because these tariffs are targeted at overseas copper manufacturers, this news has a direct effect on our industry.I-Connect007 Editor’s Choice: Five Must-Reads for the Week
Digital Twin Concept in Copper Electroplating Process Performance
07/11/2025 | Aga Franczak, Robrecht Belis, Elsyca N.V.PCB manufacturing involves transforming a design into a physical board while meeting specific requirements. Understanding these design specifications is crucial, as they directly impact the PCB's fabrication process, performance, and yield rate. One key design specification is copper thieving—the addition of “dummy” pads across the surface that are plated along with the features designed on the outer layers. The purpose of the process is to provide a uniform distribution of copper across the outer layers to make the plating current density and plating in the holes more uniform.