-
- News
- Books
Featured Books
- smt007 Magazine
Latest Issues
Current IssueIntelligent Test and Inspection
Are you ready to explore the cutting-edge advancements shaping the electronics manufacturing industry? The May 2025 issue of SMT007 Magazine is packed with insights, innovations, and expert perspectives that you won’t want to miss.
Do You Have X-ray Vision?
Has X-ray’s time finally come in electronics manufacturing? Join us in this issue of SMT007 Magazine, where we answer this question and others to bring more efficiency to your bottom line.
IPC APEX EXPO 2025: A Preview
It’s that time again. If you’re going to Anaheim for IPC APEX EXPO 2025, we’ll see you there. In the meantime, consider this issue of SMT007 Magazine to be your golden ticket to planning the show.
- Articles
- Columns
Search Console
- Links
- Media kit
||| MENU - smt007 Magazine
Meeting Current and Future Requirements of the Automotive Industry
December 19, 2016 | Pete Starkey, I-Connect007Estimated reading time: 9 minutes
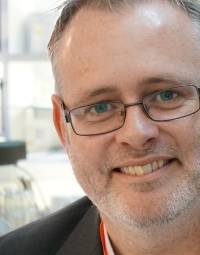
While at electronica in Munich recently, I spent time in Electrolube's booth with Phil Kinner, technical director of the company's Coatings Division. As the resident expert on conformal coatings, Kinner explained the role of conformal coatings in various applications of the automotive industry.
Starkey: Phil, thank you for inviting me to sit down with you today. We recognize you as the expert on conformal coating. And the automotive industry is very high profile, particularly in Europe, and in Germany. What sorts of things are the automotive industry demanding of you, the solutions people, in terms of the right conformal coatings for the right applications?
Kinner: That's an interesting question, the way that you phrased that. The right product is always a compromise. The requirements on the conformal coating are so many and so varied that probably the right product doesn't exist. Historically, automotive manufacturers may have used multiple coatings for different applications, but increasingly what we're seeing is a standardization on one or two coatings to cover all of the different applications.
What that really translates into for us is increased performance requirements from the coating because they're looking for the same level of protection ultimately in the cabin as they would for an under-hood or exterior kind of application. We're seeing a lot more challenges and a lot tougher performance requirements than we've ever seen, so it's a challenging time for us, but it's what we thrive on.
Starkey: What sort of materials are you formulating for these certain applications, without giving away too many trade secrets?
Kinner: Increasingly, the solvents emissions directive from 1999 is starting to become more of an issue.
Starkey: Right, so you're making solvent-free or aqueous based products?
Kinner: Solvent-free coatings yes; aqueous based, not so much, but mostly solvent-free. It definitely is the way the industry's looking to go. For us, we have a variety of different solutions from UV curable polyurethanes through to two-component polyurethane solvent-free coatings. What we've seen is that those materials in particular are giving us some outstanding properties and outstanding protection, and helping us to really be able to meet and more than meet and to really exceed the requirements of those automotive manufacturers.
Starkey: What sort of coating methods are they typically using?
Kinner: Increasingly we see selective coating being the primary application method, which is no real surprise. It's automated, it's repeatable, and the machine doesn't get tired. It doesn't generally have bad Monday mornings or lackadaisical Friday afternoons. It just does the same thing time after time, which is what the automotive industry's looking for. Then depending on the design of the part, we still see dip coating, but I think that's going to become more of a challenge with solvent-free materials. It's going to become more and more difficult, so I think selective coating is going to become more and more preferable.
Starkey: Would you effectively tune the formulation to suit the coating method?
Kinner: Absolutely. One of the key requirements really is that the material works in the equipment to give optimum results in the user’s process: defect-free, bubble-free, void-free, perfectly wetted and perfectly uniform. We've invested in buying coating equipment ourselves, so that we have it in our labs, and it's a key part of our development process to make sure that whatever we make is highly suitable for volume production.
Starkey: And do you form close working relationships with the manufacturers of the coating equipment?
Kinner: Absolutely. You can't separate one from the other. It's a bad material or a bad machine. Ultimately it's a bad process, so, for us, the focus is really having a good process. We do a lot of work, ourselves, then once we've got something we're happy with, we work very closely with the equipment guys to make sure that they can polish it and make it perfect.
Starkey: How do you see the requirements progressing into the future, and what sort of demands do you anticipate being expected to resolve for the future?
Kinner: I think traditionally thermal shock has been one of the hardest tests. In the past, with a coated assembly, it's a destructive test intended to find out weak points in design. That's really been our focus in making sure we can pass a thousand thermal shocks. I think we're now seeing 2,000, 3,000, 4,000 thermal shock cycles becoming normal requirements.
Starkey: When you say "thermal shock," can you put some numbers on that thermal shock?
Kinner: I guess the most recent one I've looked at was -40° to +140°C with a rate of change of greater than 30° per minute, so I guess it's designed to simulate a car that's been parked in North America somewhere during the winter. So the circuit was cold, and as soon as the car fires up, everything warms up and it hits its operating temperatures. Definitely a challenge. Like I said, we've just seen more and more cycles with harder and harder acceptance criteria, and then the temperature range. Not so long ago 105° was really the top end, now 140°C is normal for pretty much everything.
Starkey: I've heard people talking about 180°C this week.
Kinner: 180°C is next, and I don't think it getting any lower, and that's really where we see the two-component technology becoming more and more applicable because that's really exceeding the capabilities of single-component organic-based materials. Two-component materials enable us to achieve a much broader range of properties. The other thing that we're seeing a lot of is condensation testing.
Page 1 of 2
Suggested Items
Real Time with... IPC APEX EXPO 2025: Axxon—Leading Innovations in Dispensing Technology
04/04/2025 | Real Time with...IPC APEX EXPOAxxon-Mycronic showcases its four major divisions this year, highlighting their focus on dispensing technology and conformal coating for electronics. Jeff Leal, Director of Business Development and Strategy, explains how his company is expanding into North America, particularly in Mexico and Europe, backed by a strong customer service model.
Nordson Electronics Solutions Introduces ASYMTEK Select Coat SL-1040 Ultrasonic Cleaning Station for Maintaining Conformal Coating Equipment
02/13/2025 | Nordson Electronics SolutionsNordson Electronics Solutions, a global leader in reliable electronics manufacturing technologies, announces their latest technology innovation for conformal coating systems, the ASYMTEK Select Coat® SL-1040 Ultrasonic Cleaning Station (patent pending) to keep nozzles and needles clean, and prevent clogging during production
ViTrox Showcases Revolutionary Industry 4.0 Full Turnkey SMT PCBA Inspection Solutions at Productronica Germany 2023
09/13/2023 | ViTroxViTrox, which aims to be the world’s most trusted technology company, is thrilled to announce that we will be participating in Productronica Germany, at Booth #A2.504, from 14th to 17th November 2023, in International Congress Center München (ICM), Munich, Germany.
Dymax 9771 Conformal Coating Receives MIL-I-46058C Certification for PCBA
09/12/2023 | DymaxDymax, a leading manufacturer of light-curing materials and equipment, is pleased to announce that their ground-breaking AR conformal coating, 9771, has completed the rigorous qualification testing for Military Specification MIL-I-46058C. This UL94V0 and UL746E recognized dual-cure coating has also been approved to the IPC-CC-830B standard and fully complies with RoHS2 Directives 2015/863/EU.
Embark on an Innovative Journey: Mexico Technology Day 2023 by ViTrox & SMTo
09/12/2023 | ViTroxViTrox, which aims to be the world’s most trusted technology company, is thrilled to announce that we will be partnering with our trusted Sales Channel Partner (SCP) in Mexico, SMTo Engineering SA de CV, to bring to you our Mexico Technology Day 2023.