-
- News
- Books
Featured Books
- smt007 Magazine
Latest Issues
Current IssueSupply Chain Strategies
A successful brand is built on strong customer relationships—anchored by a well-orchestrated supply chain at its core. This month, we look at how managing your supply chain directly influences customer perception.
What's Your Sweet Spot?
Are you in a niche that’s growing or shrinking? Is it time to reassess and refocus? We spotlight companies thriving by redefining or reinforcing their niche. What are their insights?
Moving Forward With Confidence
In this issue, we focus on sales and quoting, workforce training, new IPC leadership in the U.S. and Canada, the effects of tariffs, CFX standards, and much more—all designed to provide perspective as you move through the cloud bank of today's shifting economic market.
- Articles
- Columns
- Links
- Media kit
||| MENU - smt007 Magazine
What to Look for When Auditing an Electronics Manufacturing Facility
January 26, 2017 | David Weekes, JJS ManufacturingEstimated reading time: 6 minutes
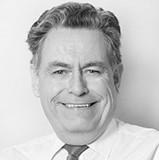
As an original equipment manufacturer (OEM), your company has worked tirelessly to narrow down the list of potential electronics manufacturing services (EMS) providers to two or three. They have spent hours trawling through web pages, downloaded technical resources and may have even talked to some of the sales and marketing staff at industry exhibitions.
This is all great preparation and, chances are, your company is now very close to making a final decision. But before they do, it falls to the quality department to carry out an assessment of each electronics manufacturing facility and capabilities.
Although a large amount of research can be carried out online, in our view, the only real way to satisfy yourself that an EMS provider will be a good fit is to meet the team and audit their processes. Having been audited ourselves numerous times, we thought it might be useful to share the approach many OEMs take and highlight some of the key questions they ask.
Background Preparation
If the decision to change supplier, or outsource for the first time, is being worked on by a cross-functional team, it’s likely that a number of previous meetings and requests for information will have already taken place. Quite often, the quality team are asked to "sense-check" the nominated EMS providers at the end of the process – i.e. just before a final decision is made. The purpose of the audit is usually to identify potential risks in transferring across to the chosen EMS provider and to understand how the team in place will help mitigate such risks.
Prior to visiting, many OEMs will send out a supplier questionnaire. These can be effective tools in gathering key pieces of information and because the responses are usually submitted back in the same format, quick comparisons can be made between multiple vendors.
Typical questions asked include:
- What is the number of employees in production/ inspection/ quality/ planning and purchasing roles?
- Do you have formal quality assurance approvals – i.e., BS EN ISO9001?
- Is the quality management system documented?
- Is a management review of the quality system carried out at regular intervals?
- Is there a documented supplier rating system in place? How is supplier approval managed?
- Is there a formal system for controlling the change of drawings and technical data?
- Are batch control procedures and inspection route cards used during all manufacturing processes?
- Are corrective action requirements documented and implemented?
- To what level are inspection processes carried out?
- Is non-conforming material recorded and quarantined?
- Do you carry out materials handling training?
- Do you operate a system for personnel training and development?
Some OEMs also send across an agenda for the day in advance to the EMS provider, outlining which areas of the business they will be focusing in on. There shouldn't be a need to go into great detail here but, by outlining the areas of interest, the EMS provider can ensure they have key staff members available throughout the day and, if required, reschedule other commitments they may already have in place.
Finally, if the EMS provider has multiple manufacturing facilities – for example, one in the UK and one in Central Eastern Europe – you should ask them to confirm that you are going to be auditing the correct site. Unless you or your team have already reached an agreement as to how and where your products will be assembled, tested and distributed then it's best not to make assumptions – otherwise, both parties may be left feeling confused and frustrated on the day.
Meet and Greet
On arrival, the majority of OEM quality managers will request a brief company overview. Despite having carried out their own background research, they will want to verify that the messages their teams have received so far (website visits, videos, sales brochures, face-to-face interaction, etc.) are consistent. It also gives them the chance to meet key members of the EMS team for the first time as previous discussions are likely to have taken place at a commercial level.
If it's not made clear to them from the outset, the quality manager should ask the EMS provider who is responsible for quality, who that person reports to and how many people are included in the quality team. In our opinion, the person responsible for quality should be allowed to work autonomously and report directly into the main board. This demonstrates that quality is taken seriously throughout the organization, driven by the senior management team and is not constrained by other internal departments. Be wary of any EMS company that wants to keep you in the boardroom with the sales team or the quality team that also appear to be responsible for sales, purchasing or operations.
During the company overview, many quality managers are keen to understand more about the key findings from the last third party audits that have taken place. Despite highly trained staff and robust procedures, things can wrong in a manufacturing environment, so perfect audit reports and zero customer complaints should be challenged a little more. They may also be interested in understanding staff turnover figures in more detail, particularly those relating to production and test. High turnover figures can suggest underlying issues, so they'll want to know what controls the EMS provider has in place to minimize risk when new starters are introduced to the manufacturing environment and, more importantly, their products.
Sampling the Process
Once a quality manager has satisfied themselves that the messages they have heard before are consistent with what they now see they will be keen to get out on the shop floor and into the detail. The majority of OEMs that audit our facility use "real-life" case study examples and follow the process all the way through from the initial request for quote and order stage, right through to inspection, test and final shipment.
During the audit, they will also pay close attention to how the operatives interact with them. Understandably, an audit situation can make some staff nervous but how engaged do they feel the staff are? Are they trying to help answer the questions or doing their best to lead the auditor down another path? Do they get the impression that the EMS provider cares about the products they are responsible for building and testing? Can they demonstrate they have the necessary controls in place to manage areas like:
- Electrostatic discharge
- Incoming material inspection
- Material traceability
- Build documentation
- Engineering change notes/ change control
- Test reports
- Calibration records
Page 1 of 2
Testimonial
"The I-Connect007 team is outstanding—kind, responsive, and a true marketing partner. Their design team created fresh, eye-catching ads, and their editorial support polished our content to let our brand shine. Thank you all! "
Sweeney Ng - CEE PCBSuggested Items
Electronic Components Market Update
10/04/2018 | Daniella Baldock, JJS ManufacturingUnfortunately, there is still no end in sight to the electronic component shortage, and some lead-times are being quoted with 2019 and even 2020 delivery dates! So if you are working with an EMS provider, it remains vital that you communicate and share forecast information with them. You may also want to start looking at the option of fitting, or designing in, smaller components to your PCB assemblies.
What SMT Component Shortages Mean for Design and Manufacturing Engineers
09/13/2018 | Russell Poppe, JJS ManufacturingMuch has been written about the increasing shortages of electronic components such as MLCCs, chip resistors and other semiconductor devices. And the manufacturing industry is now seeing price increases and greatly extended lead times. It seems the situation is likely to get rapidly worse rather than better. What can we do? Read on.
5 Supply Chain Questions to Ask Your Assembly Partner
08/16/2018 | Neil Sharp, JJS ManufacturingA key question for any OEM who may be considering outsourcing production is whether to maintain its existing supply chain or to hand those crucial purchasing decisions over to its assembly partner. This article highlights five questions to ask a potential assembly partner before handing over the responsibility for your supply chain management.
How Investment in Staff Well-Being Impacts Manufacturing Productivity
08/09/2018 | Sue Poole, JJS ManufacturingAs manufacturers seek to address the challenges of increasing efficiency, there's a greater emphasis on the value of high-performance working practices such as Lean manufacturing. But the emphasis on continual quality improvement processes can also have an indirect effect on employee health and well-being. Here's why manufacturers should invest in the well-being of its employees.
Overcoming Growth Challenges
07/19/2018 | Neil Sharp, JJS ManufacturingGrowth is usually seen by manufacturers as a good thing—a sign of success and a result of hard work. But if this growth isn’t planned for, or the manufacturer can’t react in time, growth can cause the same devastating results as if the business was in decline. This article looks at seven common areas that can cause manufacturers a headache when their business is growing, along with solutions to help ease the pain.