-
- News
- Books
Featured Books
- smt007 Magazine
Latest Issues
Current IssueSupply Chain Strategies
A successful brand is built on strong customer relationships—anchored by a well-orchestrated supply chain at its core. This month, we look at how managing your supply chain directly influences customer perception.
What's Your Sweet Spot?
Are you in a niche that’s growing or shrinking? Is it time to reassess and refocus? We spotlight companies thriving by redefining or reinforcing their niche. What are their insights?
Moving Forward With Confidence
In this issue, we focus on sales and quoting, workforce training, new IPC leadership in the U.S. and Canada, the effects of tariffs, CFX standards, and much more—all designed to provide perspective as you move through the cloud bank of today's shifting economic market.
- Articles
- Columns
- Links
- Media kit
||| MENU - smt007 Magazine
Continuous Improvement in Electronics Manufacturing
February 3, 2017 | James Wykes, JJS ManufacturingEstimated reading time: 4 minutes
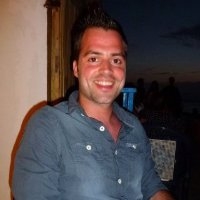
The unfortunate reality is that most, if not all, electronics manufacturing companies incur waste in the form of inefficient processes. However, without the desire to continuously improve, this waste can lead to a business becoming uncompetitive or their reputation damaged – both of which can lead to a loss of customers.
So, in order to succeed, all employees within a company must be operationally efficient and work towards a common goal of reducing waste.
With so many variables and "opportunities" to create waste, electronics manufacturing services (EMS) companies have an on-going challenge to identify, address and then eliminate inefficient processes. This is where a continuous improvement approach can help.
So, if you have ever wondered how an EMS provider manages this process and what the approach translates to on a practical, day-by-day basis, read on.
Data Collection
In order to identify areas for improvement, it is critical that the EMS provider has systems and procedures to collect accurate data. In an electronics manufacturing environment, there are multiple sources to collect data, including:
- Internal databases used to record incoming material quality issues
- Surface mount assembly and automated optical inspection (AOI) equipment
- New Product Introduction (NPI) reports
- Route/job cards out on the shop floor
- Test reports
- Internal process improvement schemes
The type of data can also vary greatly. For example, labor time fluctuations may be recorded against the route/ job card, whereas the number of defects may be captured within the automated assembly equipment software.
Data Analysis
Lean and Six Sigma tools are then used to analyse the data, in order to monitor performance, identify any spikes/ trends and help narrow potential root causes. With so much data available it's important that the EMS provider has a process internally to help prioritize their efforts. An effective way to do so is for the continuous improvement engineer to hold a monthly meeting with other stakeholders, so that agreement is reached on which projects should be worked on.
Project Implementation
In an ideal world, every project that is implemented would be able to demonstrate a clear return on investment (ROI). This is particularly true where investment in new equipment, tools or training are required. However, where "quick fixes" can be made, which clearly eliminate waste, a pragmatic approach by the EMS provider may be taken.
For example, if, via the in-house process improvement scheme, a staff member suggests moving packaging materials closer to the dispatch department does a ROI calculation really need to be made? Maybe it does, maybe this was an area crippling the rest of the business resulting in failed customer shipments. Or perhaps it will save the dispatch team a few minutes at the beginning of each day. There's not really a right or wrong answer here, except that common sense should prevail.
Project Management
It's likely the continuous improvement engineer will be working on a number of projects at any one time. To keep track of each project at a top level they will record these into some form of project tracker. The specific details of each project will then be recorded separately within a document, following the DMAIC (define, measure, analyze, improve, control) methodology.
Improvement Feedback
It's critical that there is a formal process for delivering feedback, not only to the business as a whole but to those individuals that have taken the time to input suggestions and ideas. The quickest way to kill any process improvement scheme dead in its tracks is failure to communicate progress. Ideally, this should be provided back to departments and individuals on a monthly basis. This installs confidence in the overall process and helps grow a culture of continuous improvement. In order to help staff members across the business relate to what is/ isn’t being worked on, the EMS provider may share the "Top 10" projects that have realized tangible results. Unfortunately, it's easy for individuals to dismiss process improvements, particularly within their own areas, so the EMS provider will need a system to inspire and invigorate suggestions.
Improving Improvement
If senior management do not support and encourage a continuous improvement approach, then it will be difficult for projects to move forward. A successful approach takes time and dedication, which, of course, comes at a cost. If the senior management don't really see value, or believe it's a box they can tick once a year, the rest of the company will follow suit.
Senior managers within proactive EMS providers will, however, hold quarterly meetings to discuss improvement projects and will be keen to understand how they are progressing. They will also be challenging the in-house team on how to improve the improvement process and continue to involve more and more staff.
Training
On-going education and training for all staff is essential in creating a successful continuous improvement scheme. The continuous improvement engineer within the EMS provider will be expected to lead in this area and develop training programs designed to teach employees about waste and how to implement a DMAIC project, utilizing Lean and Six Sigma tools. Following these training sessions, attendees will be encouraged to identify their own improvement projects and take ownership in seeing these through.
Hopefully, this short article has helped demonstrate how EMS providers can, and should be, approaching continuous improvement. As a customer, you may not always be party to the finding or the solutions that are put in place as many improvements are likely to relate to internal processes. However, if you are interested in finding out more about example projects, or the finer details of the program, we recommend getting in touch with the quality representative within the EMS provider so they can explain some more.
This post originally appeared on the JJS Manufacturing blog, which can be found here.
Testimonial
"Advertising in PCB007 Magazine has been a great way to showcase our bare board testers to the right audience. The I-Connect007 team makes the process smooth and professional. We’re proud to be featured in such a trusted publication."
Klaus Koziol - atgSuggested Items
The Art and Science of PCB Floor Planning: A Comprehensive Guide
08/14/2025 | Cory Grunwald and Jeff Reinhold, Monsoon SolutionsPCB design is an intricate and crucial part of developing electronic products. One of the foundational stages of PCB design is floor planning, a phase where the placement of components and the flow of signals are meticulously mapped out. A good floor plan ensures that the PCB performs well, is easy to manufacture, and meets all mechanical and electrical requirements. We’ll explore the essential aspects of floor planning, from its objectives and process to the challenges that designers face.
Advint and SanRex Expand High-Performance DC Rectifier Access for North American PCB Fabricators
08/12/2025 | Advint IncorporatedAdvint Incorporated has entered a strategic partnership with SanRex Corporation, enhancing access to industrial-grade DC rectifiers for the US printed circuit board industry. With a legacy of power innovation and performance across the globe, SanRex rectifiers are available through Advint’s proficient distribution network.
Advint and Sayron Bring Advanced Rectifier Solutions to High-Reliability PCB Manufacturers
08/01/2025 | Advint IncorporatedAdvint Incorporated has partnered with Sayron, a leading global rectifier manufacturer, to supply cutting-edge IGBT-based DC rectifiers to high-performance PCB manufacturers across North America and beyond. Sayron’s precision-engineered rectifiers align with the stringent requirements of advanced PCB processes.
Trouble in Your Tank: Metallizing Flexible Circuit Materials—Mitigating Deposit Stress
08/04/2025 | Michael Carano -- Column: Trouble in Your TankMetallizing materials, such as polyimide used for flexible circuitry and high-reliability multilayer printed wiring boards, provide a significant challenge for process engineers. Conventional electroless copper systems often require pre-treatments with hazardous chemicals or have a small process window to achieve uniform coverage without blistering. It all boils down to enhancing the adhesion of the thin film of electroless copper to these smooth surfaces.
Magnalytix’s Dr. Mike Bixenman to Guide PDC at SMTA High-Reliability Cleaning and Conformal Coating Conference
07/31/2025 | MAGNALYTIXMagnalytix, providing real-time reliability solutions for electronics manufacturing, is excited to announce that Dr. Mike Bixenman will present the professional development course “The Effects of Flux Residues and Process Contamination on the Reliability of the Electronic Assembly” on Wednesday, Aug. 13 at 9:00 AM CST to open the second day of the STMA High-Reliability Cleaning and Conformal Coating Conference.