-
- News
- Books
Featured Books
- smt007 Magazine
Latest Issues
Current IssueIntelligent Test and Inspection
Are you ready to explore the cutting-edge advancements shaping the electronics manufacturing industry? The May 2025 issue of SMT007 Magazine is packed with insights, innovations, and expert perspectives that you won’t want to miss.
Do You Have X-ray Vision?
Has X-ray’s time finally come in electronics manufacturing? Join us in this issue of SMT007 Magazine, where we answer this question and others to bring more efficiency to your bottom line.
IPC APEX EXPO 2025: A Preview
It’s that time again. If you’re going to Anaheim for IPC APEX EXPO 2025, we’ll see you there. In the meantime, consider this issue of SMT007 Magazine to be your golden ticket to planning the show.
- Articles
- Columns
Search Console
- Links
- Media kit
||| MENU - smt007 Magazine
Electrolube Talks Technologies Targeted at Automotive and LED Applications
March 31, 2017 | Stephen Las Marias, I-Connect007Estimated reading time: 8 minutes
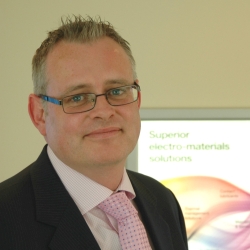
Electrolube's Phil Kinner, global head for the conformal coatings business, talks about the trends shaping the company’s product innovation strategies, and their latest solutions and technologies to help address their customers’ greatest challenges.
Stephen Las Marias: From a conformal coating standpoint, what are the greatest challenges that your customers face?
Phil Kinner: Many of our customers increasingly face challenges regarding environmental protection, with more and more applications taking electronics to places where they wouldn’t previously have gone before. So we have seen a lot of opportunities for coatings and encapsulation resins to help protect customer devices from even the harshest of operating environments. These opportunities have largely arisen from automotive and LED customers who consistently face challenges with corrosion, condensation and high humidity. We’ve also seen an increase in customers enquiring about reducing tin whisker growth, eliminating VOCs, reducing conductor spacing and ultimately increasing productivity. Everything’s got to be smaller, more tightly spaced, faster, more powerful and has to last longer. We are also frequently asked about coverage, if the coating doesn’t cover, it can’t protect and that is certainly an issue facing customers.
Las Marias: How is Electrolube helping customers address their issues above?
Kinner: Our strength lies in our ability to resolve problems and find suitable solutions for our customers. In the last year, we have made significant investment in the very latest testing equipment for our laboratories and a top of the range selective conformal coating system, which definitely gives us an edge over competitors when it comes to helping our customers. Our new thermal shock chamber is state-of-the-art and most chemical protection manufacturers don't have this kind of machine at their disposal, and need to first send their products off to a third party test house before they understand the capabilities of their products. If we have a specific technical enquiry from a customer who wants to know whether or not something will meet a specific number of cycles, or a specific range, then we can run it for them. For instance, we had an enquiry where the customer was looking at a -40°C to 160°C temperature range for a product and had three weeks to make a decision and we managed to turn the testing around in just two weeks giving the customer a whole week to evaluate the data. The new system is also becoming increasingly beneficial for automotive customers, especially as they transition from solvent-based materials to VOC-free alternatives. Given that most of the products that we're developing are VOC-free, and thermal shock is one of the main challenges to this technology, it naturally makes sense to invest in the equipment not only for customers, but for our own product development, to help us reduce the time to market of reliable, high-performance materials. Testing our products before they go to market is everything, and ultimately positions us well as a reliable and complete solutions provider across all areas of the production process.
Las Marias: What are some of the latest technologies released by Electrolube over the past year that are helping customers address their specific problems?
Kinner: Traditionally, we have our resin business and we have our coating business. What we've done is merge the two divisions together to make a hybrid product called 2K, so it has the protection of an encapsulation resin with the ease of application and reduced weight demands of a conformal coating. It’s a pretty revolutionary product—it’s green, solvent-free, easy to apply, cures quickly and gives superior protection to any other coatings that are available on the market right now. The product helps customers save time, reduce cost and improve productivity. It’s a thicker material that enables better edge coverage without compromising on thermal shock or other performance parameters. It helps increase productivity by reducing material usage, cost and cycle time and improves process optimization and reliability. 2K features all the advantages of the coating and all the advantages of encapsulation resins combined into one package, which really solves both environmental performance and process issues that relate to all of these issues. The 2K two part conformal coating range currently consists of three products; 2K100, 2K300 and 2K500, and we are in the process of developing new products to extend the series.
We have also developed an ultra-thin coating called FPC, which also helps boost productivity. FPC is a specialist fluorinated polymer coating that repels hydrocarbon and silicone oils, synthetic fluids and aqueous solutions due to its very low surface energy. It performs extremely well, offering excellent protection for printed circuit boards and electronics in exposed environments. Once dried, FPC has a low film strength and is easily removed, allowing assemblies to be coated without masking. It’s also very easy to apply and has an exceptionally fast-touch dry time.
Our new selective conformal coating system, equipped with both film coat and spray valves, is an advanced conveyorized platform providing the highest quality and productivity for automated coating processes. A wide range of conformal coating process parameters can be monitored for both statistical process control and traceability purposes. Many of our customers now prefer to use selective coating methods in order to minimize their materials and process costs, and to meet specific design issues. We are very keen to ensure that our latest products are fully optimized in terms of viscosity, chemical composition and associated work time, as appropriate for selective coating. Having such advanced production grade equipment in a laboratory setting will help us further strengthen our capacity to replicate customer issues and develop materials for optimum performance in selective coating equipment, which in turn will also help us provide the very best support and guidance on product and process selection. We are also using the new equipment for customers engaging in product trials. Our customers are given independent access to Electrolube's facilities, bringing their samples to the laboratory to evaluate the performance of new products, application techniques or processes. In this way, later disruptions to production from unsuitable product or process selection can be avoided.
Las Marias: What makes these products unique in the market?
Kinner: The 2K series of conformal coatings is particularly revolutionary and unique as it offers the distinctive protection of an encapsulation resin with the ease of application and reduced weight demands of a conformal coating. There is no other solvent-free, high-performance, thick-film, 2K coating material on the market like it. Our FPC fluorinated polymer coating is unique in terms of its lower insertion force required to remove coating during connector mating, hence providing a more reliable connection. It also received UL94V-0 recognition and has a UV trace to aid inspection.
Las Marias: What market development trends and which end-applications are shaping product innovation strategies at Electrolube?
Kinner: The automotive market is currently a major driver of product development, particularly in conformal coatings and encapsulants for electronics in hostile environments, and there are numerous new applications associated with power management in hybrid and electric drive systems. The rapid growth of LED technology in automotive, domestic and municipal lighting applications has also been a catalyst for accelerating our development of new thermal transfer materials and UV stable coatings for this market. The protection provided by conformal coatings allows for higher power and closer track spacing, in turn enabling designers to meet the demands of miniaturization and reliability.
Las Marias: What new technologies should we expect from Electrolube this year?
Kinner: We will be introducing new encapsulation resins, thermal management materials and conformal coating systems, particularly with emphasis on extending the 2K series.
Page 1 of 2
Suggested Items
Department of the Air Force Outlines Fiscal 2026 Budget Priorities to Congressional Panel
05/07/2025 | United States Space ForceThe three most senior civilian and military officials from the Department of the Air Force told a congressional panel May 6 that “the strategic landscape has shifted dramatically” and that the Air Force and Space Force need the resources and creative thinking, along with modern capabilities, to meet emerging threats.
RTX's Collins Aerospace Enhances Capabilities to Speed Marine Corps Decision-making in Battle
04/22/2025 | RTXCollins Aerospace, an RTX business, successfully demonstrated new technology that helps the military gather and use information from a wider range of sources at Project Convergence Capstone 5, a large-scale military exercise.
Real Time with... IPC APEX EXPO 2025: GreenSource's Growth and Future Developments
04/15/2025 | Real Time with...IPC APEX EXPOThings are looking bright for GreenSource. Michael Gleason shares an update on GreenSource's recent growth and upcoming changes. A recipient of a Defense Production Act Investment Program award, GreenSource is planning for new substrate capabilities. Current investments continue to enhance equipment and sustainability initiatives such as water quality. And their unique collaboration with the University of New Hampshire continues to aid their workforce development, despite recruitment challenges.
Acquisition of MADES Strengthens Cicor's Pan-European Leadership in the Aerospace & Defense Sector
04/03/2025 | CicorCicor Group announces that it has signed an agreement to acquire 100% of the shares of Spanish electronics company Malaga Aerospace, Defense & Electronics Systems S.A.U. (MADES). The company focuses on electronic solutions for the aerospace and defense industry, which accounts for well over half of its business.
Real Time with... IPC APEX EXPO 2025: Discover Comprehensive PCB Solutions with American Standard Circuits
04/01/2025 | Real Time with...IPC APEX EXPOAnaya Vardya, CEO of American Standard Circuits, highlights the company's dedication to offering complete PCB solutions. The company provides free design packages and caters to various sectors, including military and telecommunications.