-
- News
- Books
Featured Books
- smt007 Magazine
Latest Issues
Current IssueIntelligent Test and Inspection
Are you ready to explore the cutting-edge advancements shaping the electronics manufacturing industry? The May 2025 issue of SMT007 Magazine is packed with insights, innovations, and expert perspectives that you won’t want to miss.
Do You Have X-ray Vision?
Has X-ray’s time finally come in electronics manufacturing? Join us in this issue of SMT007 Magazine, where we answer this question and others to bring more efficiency to your bottom line.
IPC APEX EXPO 2025: A Preview
It’s that time again. If you’re going to Anaheim for IPC APEX EXPO 2025, we’ll see you there. In the meantime, consider this issue of SMT007 Magazine to be your golden ticket to planning the show.
- Articles
- Columns
Search Console
- Links
- Media kit
||| MENU - smt007 Magazine
How to Solder SMT Components with Varying Solder Paste Heights
April 13, 2017 | Danielle Olivier, JJS ManufacturingEstimated reading time: 6 minutes
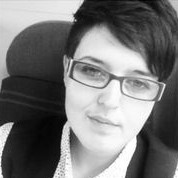
The rise in demand for miniaturized components within consumer electronics is forcing designers of industrial electronics to work with smaller component packages.
While miniaturized components offer product designers some benefits, such as energy efficiency and the ability to build in greater functionality, mixing "old and new" technology together on the same printed circuit board (PCB) design can add complexity at the build stage.
This is a particular challenge for products that are “upgraded” over time with changes made on a component-by-component basis, rather than in consideration of the overall design.
As a result, it is sometimes necessary to change the way solder paste is applied to the PCB during production. This article focuses on two techniques that can help to overcome these potential challenges during the build process.
Why a Single Level Solder Stencil May Not Be Appropriate
To create a successful solder joint after reflow, the solder paste needs to be applied at an appropriate height for the components that are being mounted. This is controlled by the thickness of the stencil and the apertures within. Over the years, stencil manufacturers have had to adapt their products to reflect the growing trend in making products smaller, faster, etc. As an example, we have seen standard thickness stencils of eight thou reduce down to six, five and now four thou (0.001 inch) and below.
Traditionally, applying a standard height of solder paste across the entire board was sufficient to create a successful solder joint – one size (solder stencil) tended to fit all. However, the increasing popularity of miniaturized components, used in tandem with much larger components, means that this solution is not always suitable. As the solder paste height required for parts on the same board can now vary significantly, manufacturers are increasingly finding themselves having to invest in multi-level (or multi-height) solder paste printing techniques to avoid the risk of shorts or open joints occurring post reflow.
At this stage, it is important to note that screen-printing solder paste is not your only option when it comes to applying solder paste to a board. Solder paste can also be dispensed at varying heights in one sitting, from a dispensing unit. However, this process is considerably more time consuming – for example, a medium complexity small PCB can take approximately two and a half minutes to complete, compared to the forty seconds or so screen printing takes. Therefore, electronics manufacturers must consider their options wisely to avoid the process becoming costly, particularly if they are building PCBAs in large volumes.
Multi-level Stencils
Two common methods in creating multi-level stencils include "stepped" and "additive" techniques. The conventional way to create a stepped stencil is to start with a standard thickness - for example 5 thou - and etch away small areas to reduce the thickness for specific components. Additive stencils are created in a similar way - however, they start with a greater thickness stencil and the majority of the surface area is then etched away to a lower thickness, leaving one section slightly higher than the rest. Additive stencils can also be produced by layering sections of stencil on top of each other – adding sections to make it higher – hence the name.
As with most things, there are pros and cons to using multi-level stencils - regardless of which way they are made. To help with decision-making, here are a few factors you may want to consider:
1. Development time
Do you have the time to test, re-test and develop your stencil? It is possible that your first stencil design will not transfer a perfect solder print. For example, if the step created is not large enough the solder paste can gather in the corners of the step when the squeegee attempts to clean the top surface of the stencil. This can become a problem during continuous production as you run the risk of excess paste blocking the apertures of the stencil, which has the potential to inhibit the smooth flow of solder paste through the openings and reduce the level of transference onto the PCB. As a result, you may need to re-design and re-test the stencil until the correct dimensions are achieved, making the stencil design process somewhat costly and time-consuming.
2. The proximity of the mixed technology
As already discussed, the multi-level section needs to be large enough that the squeegee can adequately clean the top face of the stencil. This may mean that you find it necessary to include apertures for other components within the etched section. However, this is also likely to mean that those extra components will receive a lower height of solder paste in line with the miniaturized component, which may not be sufficient.
3. Cost
Taking into account the time, labor and stencil design process, creating the perfect multi-level stencil can become a costly exercise. If you intend to manufacture PCBs on a regular basis in medium to high volumes then you will probably find the upfront cost soon pays for itself. However, if you decide on an alternative approach – for instance hand placement – you will need to factor in the extra hours this method takes and the costs associated with it.
Direct Flux Application
Direct flux application as a soldering technique can only be used for ball grid array (BGA) components – regardless of size. Applying the correct height of flux to a BGA presents similar challenges to applying the correct height of solder paste to a PCB. Too much and the gaps between the joints could fill with flux residue post reflow, limiting your ability to under fill the component. Likewise, not enough flux and the solder will not flow to its optimum and you could be left with dry or open joints. Based on experience, we recommend to cover 50-75 per cent of the solder ball height in flux.
Two common techniques to apply flux during SMT assembly include:
1. Dispensing
2. Dipping
There are reasons for and against using both techniques. The main argument against dispensing flux onto a PCB is simple - it takes more time. Unlike dipping, where components are dipped directly into a pre-set height of flux within a transfer plate, dispensing applies a level of flux directly onto the PCB at the stencil print stage before the components are placed.
While the time needed to prepare each board increases, dispensing can be a suitable alternative when dipping is not possible – i.e. when there are SMT production equipment restrictions. Flux dispensing units are also considerably cheaper than flux transfer plates.
The dipping technique consists of a squeegee and a flux transfer plate that has several cavities of varying depths etched out. The squeegee wipes the flux across the cavities, leaving them filled with flux. The unit is then ready for the SMT equipment to pick up the components, dip them in the specified cavity of flux, and then place them on the board. This process, compared to the dispensing alternative, is much faster and therefore lowers the total manufacture time and has the ability to improve accuracy and consistency.
Inspecting the Results
As the saying goes, "the proof is in the pudding", so once you have built a first off board using either technique it is best practice to inspect and test the output. X-ray images of the board can highlight any shorts or solder bridging - however, for optimum reassurance we also recommend horizontal and vertical sectioning. This method of inspection highlights the connections between the pad, solder and component allowing you to see even the smallest defect.
As we have explored in this blog post, the race to make products smaller, faster, with greater functionality in the consumer world is continuing to impact industrial electronics. Thankfully, many of the challenges associated with consistently soldering SMT components with varying solder paste heights can be overcome with time, experience and robust build, test and inspection processes.
This article originally appeared on the JJS Manufacturing blog, which can be found here.
Suggested Items
Indium’s Karthik Vijay to Present on Dual Alloy Solder Paste Systems at SMTA’s Electronics in Harsh Environments Conference
05/06/2025 | Indium CorporationIndium Corporation Technical Manager, Europe, Africa, and the Middle East Karthik Vijay will deliver a technical presentation on dual alloy solder paste systems at SMTA’s Electronics in Harsh Environments Conference, May 20-22 in Amsterdam, Netherlands.
SolderKing Achieves the Prestigious King’s Award for Enterprise in International Trade
05/06/2025 | SolderKingSolderKing Assembly Materials Ltd, a leading British manufacturer of high-performance soldering materials and consumables, has been honoured with a King’s Award for Enterprise, one of the UK’s most respected business honours.
Knocking Down the Bone Pile: Gold Mitigation for Class 2 Electronics
05/07/2025 | Nash Bell -- Column: Knocking Down the Bone PileIn electronic assemblies, the integrity of connections between components is paramount for ensuring reliability and performance. Gold embrittlement and dissolution are two critical phenomena that can compromise this integrity. Gold embrittlement occurs when gold diffuses into solder joints or alloys, resulting in mechanical brittleness and an increased susceptibility to cracking. Conversely, gold dissolution involves the melting away of gold into solder or metal matrices, potentially altering the electrical and mechanical properties of the joint.
'Chill Out' with TopLine’s President Martin Hart to Discuss Cold Electronics at SPWG 2025
05/02/2025 | TopLineBraided Solder Columns can withstand the rigors of deep space cold and cryogenic environments, and represent a robust new solution to challenges facing next generation large packages in electronics assembly.
BEST Inc. Reports Record Demand for EZReball BGA Reballing Process
05/01/2025 | BEST Inc.BEST Inc., a leader in electronic component services, is pleased to announce they are experiencing record demand for their EZReball™ BGA reballing process which greatly simplifies the reballing of ball grid array (BGA) and chip scale package (CSP) devices.